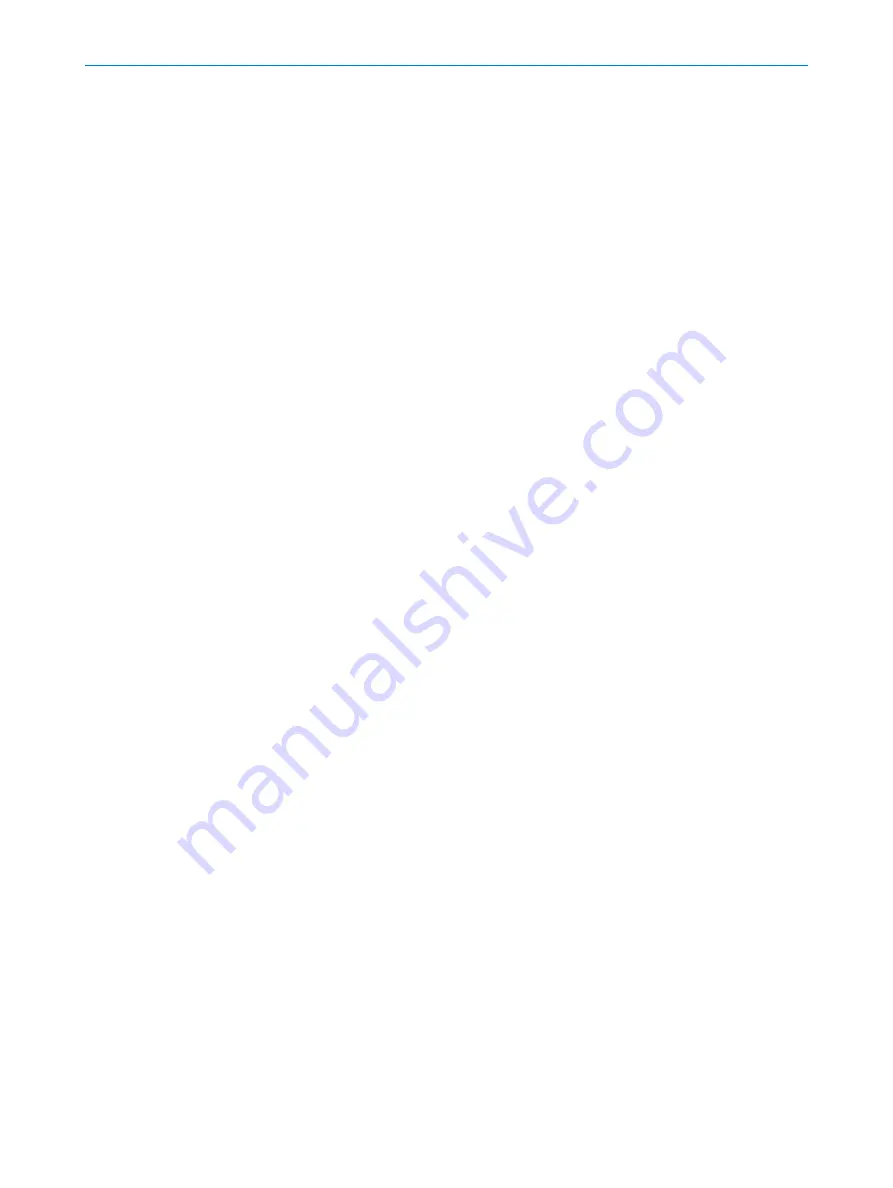
3.5.3.2
Triggered output of measured values
During triggered measurement, the start and end of the measurement are determined
by a reading gate.
First, the trigger source is selected via the laser control settings,
.
After this, measured values are initially requested with the
sEN LMDscandata 1
telegram,
, in the same way as for the continuous out‐
put of measured values.
Measured values are only output if the laser is switched on (to open the reading gate). If
the reading gate is closed, the laser will switch off, thereby terminating the measure‐
ment process and the output of measured values.
A software trigger or the digital inputs input 1 or 2 can be used for triggering purposes.
3.5.3.3
Connecting encoders
If the device is mounted for mobile use or if the objects to be measured are in motion,
the application will usually also need position data to further process the measured val‐
ues.
Encoders can be connected for this purpose. The encoder data is then available with
the other measured values in a single scan and at the same interface. A volume,
for example, can be calculated by evaluating the measurement data. The input fre‐
quency of the encoder signal must not exceed 50 kHz.
The following encoders with push-pull output stage can be used:
•
Single-channel, only connected at encoder A, no direction detection.
•
Dual-channel (phase), connected at encoder A and encoder B; the pulses have a
phase shift of 90°, making direction detection possible. By definition, during for‐
ward motion (CW = clockwise) phase A precedes phase B; conversely, during
reverse motion (CCW = counterclockwise) edge A rises before edge B.
•
Dual-channel (level), connected at encoder A and encoder B; the pulses are at
encoder A; at encoder B, the direction is indicated by level 0 or level 1 (rarely).
3.5.4
Laser control
Laser control is used to switch the laser on and off. Measurement data is only transmit‐
ted when the laser is switched on. To initiate the transmission of measurement data,
the telegram command
sEN LMDscandata 1
(hexadecimal:
73454E204C4D447363616E646174612001
must be
sent once after switching on the device.
Since the motor turns constantly at the scan speed as long as the device is ready for
operation, the device is ready to start taking measurements immediately after the laser
has been switched on.
Laser control reduces the data load at the Ethernet interface. Switching the laser on
and off specifically when required also increases the service life of the laser diode.
The “switch-on delay” and “switch-off delay” parameters can be set to switch the laser
on subject to a time delay and/or to leave it switched on longer for a defined period
after the trigger signal has dropped out.
Following login (minimum
Authorized customer
), it is possible to select between various
modes on the
Basic settings
tab in SOPAS ET or using a corresponding terminal program.
In free-running mode, the laser is permanently switched on and the device detects
measurement data permanently (default setting). This mode is intended specifically for
test purposes or for aligning a device with the laser line.
PRODUCT DESCRIPTION
3
8023198//2018-06-18 | SICK
O P E R A T I N G I N S T R U C T I O N S | LMS4000
17
Subject to change without notice