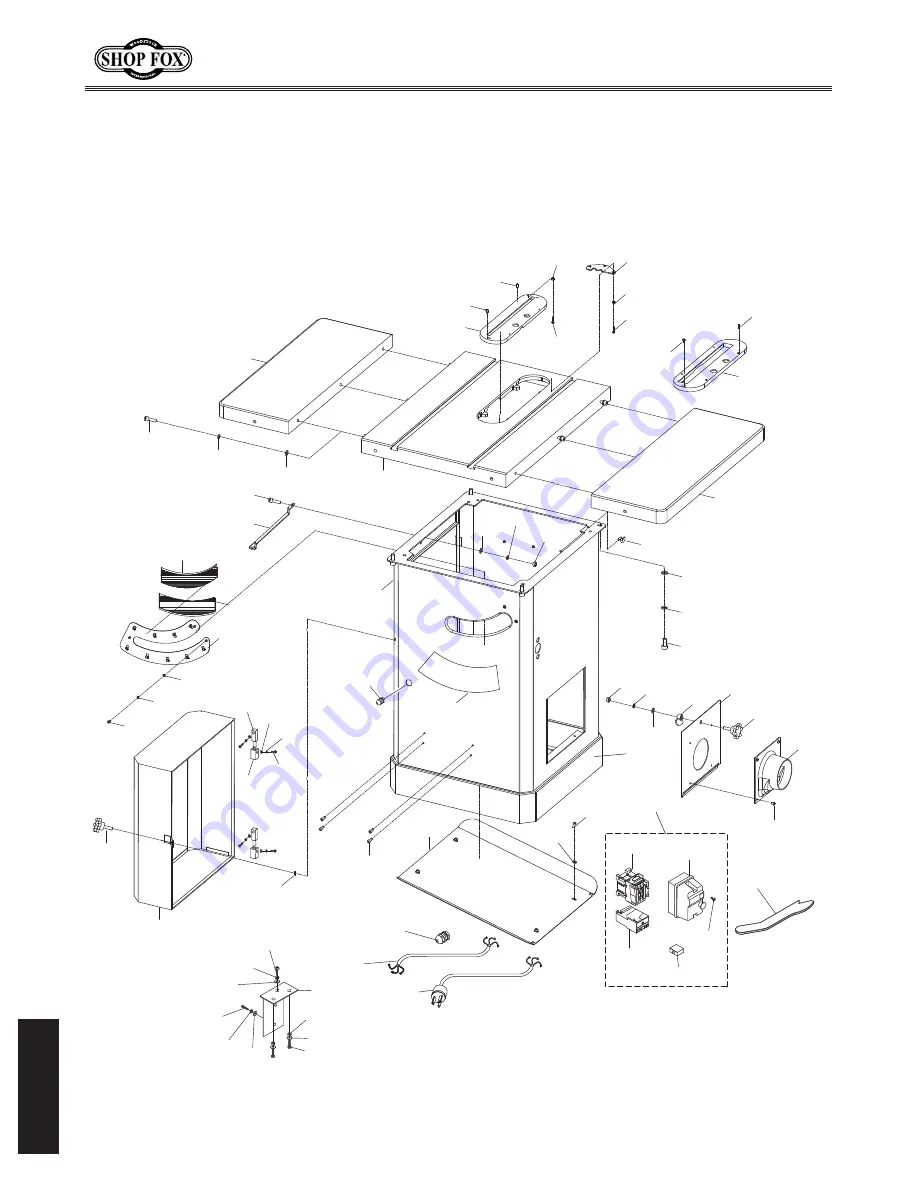
-78-
Df[\cN(/(0&N(/)'=fiDXZ_`e\jD]^%J`eZ\*&('
G8
I
K
J
155
155-1
155-2
155-3
155-4
155-5
108
109
109
156
110
110
168
169
170
171
101
102
103
104
105
106
107
108
109
114
115
118
119
120
121
122
123
124
125
126
127
127
128
129
130
131
132
132
133
133
134
136
140
141
142
143
144
145
146
146-1
146-2
147
148
149
150
151
152
153
153
154
164
163
172
166
165
173
177
174
175
176
G8IKJ
9f[p