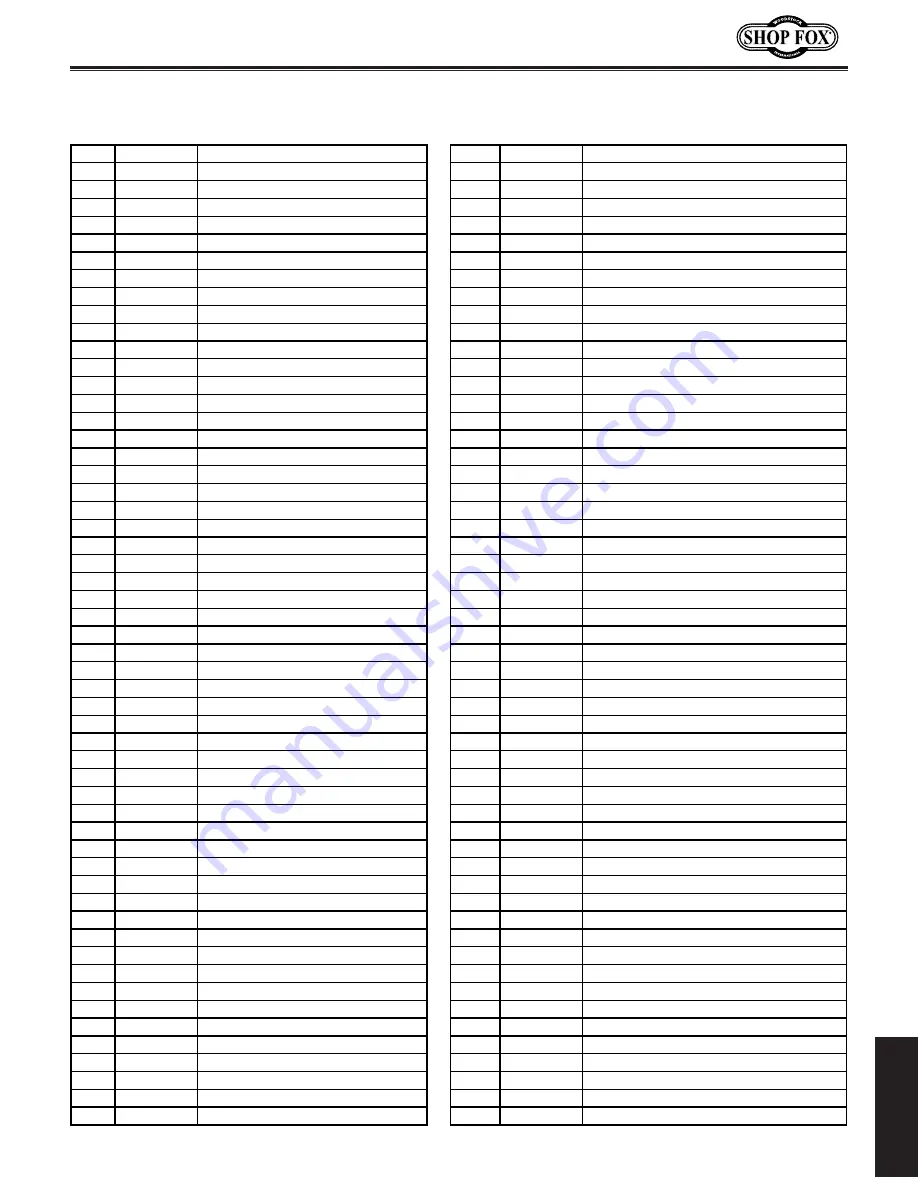
-59-
W1772/W1773 37" Drum Sander
PA
RT
S
Frame
REF PART #
DESCRIPTION
REF
PART #
DESCRIPTION
122
X1772122
SIDE PANEL
182
X1772182
HEX NUT M10-1.5
123
X1772123
HEX BOLT M8-1.25 X 30
183
X1772183
FLAT WASHER 10MM
125
X1772125
GAS STRUT
184
X1772184
DRIVING LIFT SCREW M20-2.5
127
X1772127
FRONT UPPER FRAME ANGLE
185
X1772185
HEX NUT M20-2.5
128
X1772128
BUTTON HD CAP SCR M6-1 X 12
304
X1772304
MOTOR JUNCTION BOX STRAIN RELIEF
129
X1772129
FLAT WASHER 6MM
305
X1772305
CABLE CLAMP
130
X1772130
MOUNTING BRACKET
306V2 X1772306V2 ELECTRICAL BOX V2.08.13
131
X1772131
EMERGENCY STOP SWITCH MJ2-1307
307
X1772307
FLAT WASHER 8MM
132
X1772132
EMERGENCY STOP BAR
308
X1772308
HEX BOLT M8-1.25 X 25
133
X1772133
BUTTON HD CAP SCR M6-1 X 12
309V2 X1772309V2 CONTROL PANEL PEDESTAL ARM V2.08.13
135
X1772135
COMPRESSION SPRING
310
X1772310
SUPPORT STRAP
136
X1772136
FLAT WASHER 6MM
311
X1772311
HEX BOLT M8-1.25 X 30
137
X1772137
HEX NUT M6-1
312
X1772312
HEX NUT M8-1.25
138
X1772138
HEX NUT M6-1
313
X1772313
GEARBOX
139
X1772139
REAR UPPER FRAME ANGLE
314
X1772314
CONNECTING SHAFT
140
X1772140
SUPPORT PLATE (LH)
315
X1772315
BUSHING
141
X1772141
SUPPORT PLATE (RH)
316
X1772316
GEAR 20T
142
X1772142
CAP SCREW M6-1 X 12
317
X1772317
SET SCREW M6-1 X 10
143
X1772143
FLAT WASHER 6MM
318
X1772318
FLAT WASHER 10MM
148
X1772148
RUBBER PLATE 1005 X 65 X 2MM
319
X1772319
WORM SHAFT
149
X1772149
PLATE
320
X1772320
BUSHING
150
X1772150
PHLP HD SCR 10-24 X 1/2
321
X1772321
WORM GEAR
150-1 X1772150-1 HEX NUT 10-24
322
X1772322
SET SCREW M6-1 X 6
151
X1772151
KNOB M8-1.25 X 55
323
X1772323
WRENCH 12 X 14MM OPEN-ENDS
152
X1772152
LOCK BUSHING
324
X1772324
HEX WRENCH 4MM
155
X1772155
TOP COVER
324-1 X1772324-1 SET SCREW M6-1 X 10
156
X1772156
DUST SCOOP
325
X1772325
HEX WRENCH 5MM
157
X1772157
BUTTON HD CAP SCR M6-1 X 10
340
X1772340
SCREWDRIVER PHILLIPS #2
158
X1772158
FLAT WASHER 6MM
348
X1772348
PHLP HD SCR M4-.7 X 10
159
X1772159
ACORN NUT M6-1
352
X1772352
GAS STRUT PIVOT SCREW
160
X1772160
ADHESIVE FOAM STRIP 15 X 95
353
X1772353
CONTROL ELECTRICAL BACK PLATE
161
X1772161
ADHESIVE FOAM STRIP 15 X 130
353-1 X1772353-1 SANDING MOTOR CORD 10G 4W 98"
164
X1772164
HANDLE
353-2 X1772353-2 FEED MOTOR CORD 14G 3W 79"
165
X1772165
CAP SCREW 5/16-18 X 3/4
353-3 X1772353-3 CORD 16G 2W 98"
166
X1772166
FLAT WASHER 5/16
354
X1772354
CORD 6G 3W 98"
167
X1772167
HEX NUT 5/16-18
355
X1772355
GROUND WIRE 8G 1C 2.5" (GREEN)
168
X1772168
HINGE
356
X1772356
CONTROL PANEL PLATE
169
X1772169
BUTTON HD CAP SCR M6-1 X 12
363
X1772363
POWER JUNCTION BOX COVER
170
X1772170
KNOB BOLT M6-1 X 12
364
X1772364
POWER JUNCTION BOX
171
X1772171
HANDWHEEL HANDLE
366
X1772366
STRAIN RELIEF LT STRAIGHT
172
X1772172
SET SCREW 3/8-16 X 1/2
367
X1772367
FLANGE SCREW M5-.8 X 10
173
X1772173
HANDWHEEL
369
X1772369
CORD 6G 3W 86"
174
X1772174
HANDWHEEL SLEEVE
370
X1772370
FLAT WASHER 16MM
175
X1772175
SET SCREW M6-1 X 10
371
X1772371
BUTTON HD CAP SCR M6-1 X 10
176
X1772176
HEX NUT M6-1
373
X1772373
TERMINAL BAR 1P
177
X1772177
LIFT SCREW M20-2.5
374
X1772374
GROUND TERMINAL BAR 1P
178
X1772178
THRUST BEARING 51103
375
X1772375
TERMINAL BAR LOCKING SEGMENT
179
X1772179
CHAIN 3/8" PITCH
376
X1772376
TERMINAL BAR MOUNT
180
X1772180
SPROCKET
377
X1772377
HEX NUT M6-1
180-1 X1772180-1 SPROCKET
378
X1772378
POWER CORD CONDUIT COVER
180-2 X1772180-2 KEY 5 X 5 X 20
379
X1772379
POWER CORD CONDUIT
180-3 X1772180-3 SET SCREW 1/4-20 X 1/4
380
X1772380
STRAIN RELIEF PGB 29-25 ST PLASTIC
181
X1772181
SHAFT
381
X1772381
EXT TOOTH WASHER 5/16
181-1 X1772181-1 BALL BEARING 6000-2RS
382
X1772382
HEX NUT 5/16-18
181-2 X1772181-2 INT RETAINING RING 10MM
553
X1773553
480V CONVERSION KIT (W1773)