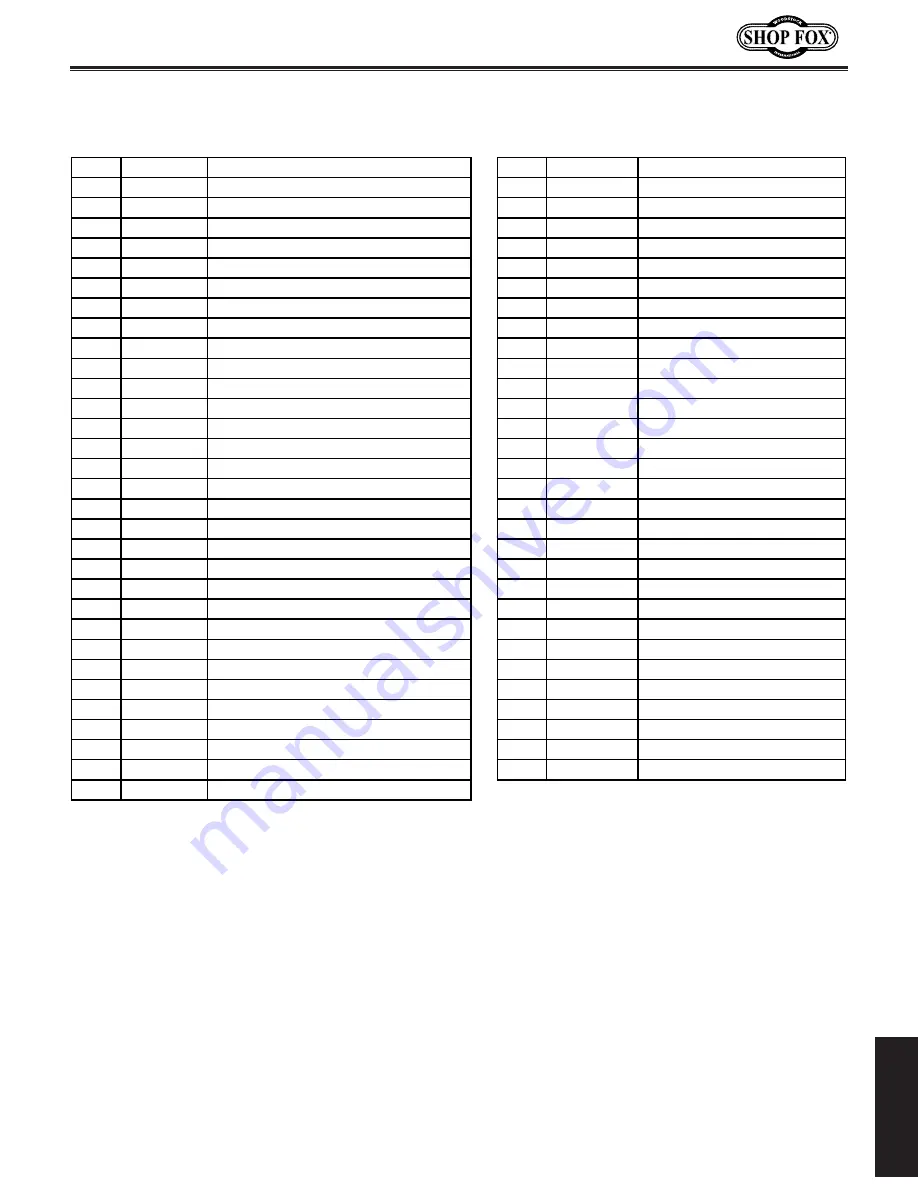
-27-
Model W1767 (For Machines Mfd. Since 08/15)
PA
RT
S
Main.Parts.List
REF PART #
DESCRIPTION
REF PART #
DESCRIPTION
1
X1767001
BALL BEARING 6203 OPEN
38
X1767038
DOUBLE SPROCKET
2
X1767002
GREASE FITTING
39
X1767039
CHAIN (40S)
3
X1767003
SPROCKET CASE
44
X1767044
WORM GEAR
4
X1767004
TORSION SPRING 3.8 X 102
50
X1767050
O-RING 101.19MM X 3.53MM
5
X1767005
CASE COVER
51
X1767051
WORM GEAR BOX COVER
6
X1767006
GREASE NIPPLE
52
X1767052
OIL SEAL
7
X1767007
SPROCKET CASE
53
X1767053
CAP SCREW M5-.8 X 16
8
X1767008
TORSION SPRING 3.8 X 102
55
X1767055
FLAT WASHER 1/2
9
X1767009
CASE COVER
56
X1767056
HEX NUT M12-1.75
10
X1767010
ROLLER SUPPORT
57
X1767057
WORM GEAR SHAFT
11
X1767011
SPROCKET
58
X1767058
WORM GEAR KEY
12
X1767012
LOCK WASHER 6MM
62
X1767062
GEAR 25T
13
X1767013
CAP SCREW M6-1 X 16
63
X1767063
CAP SCREW M8-1.25 X 40
14
X1767014
LOCK WASHER 8MM
64
X1767064
GEAR 40T
16
X1767016
CHAIN (26S)
68
X1767068
LUBRICATOR
17
X1767017
TUBE
70
X1767070
MOTOR 220V 2SPD 1PH
18
X1767018
EXT RETAINING RING 24
70-1
X1767070-1 SWITCH W/ELECTRICAL BOX
19
X1767019
SPROCKET SHAFT
70-2
X1767070-2 BOX COVER
20
X1767020
EXT RETAINING RING 13MM
70-3
X1767070-3 FAN COVER
22
X1767022
FLAT WASHER 1/2
70-4
X1767070-4 MOTOR FAN
23
X1767023
HEX NUT M12-1.75
70-5
X1767070-5 CAPACITOR 35MFD 250VAC
24
X1767024
GREASE NIPPLE
70-6
X1767070-6 SEALING RING
25
X1767025
ROLLER SPINDLE
75
X1767075
O-RING 27.5 X 2.0 S28
26
X1767026
SPROCKET CASE HEX BOLT M12-1.75
77
X1767077
CAP
27
X1767027
KNOB
79
X1767079
CAP SCREW M5-.8 X 10
28
X1767028
OIL CAP
81
X1767081
BACK COVER
29
X1767029
O-RING 14.8 X 2.4 P15
87
X1767087
ROLLER
30
X1767030
CASTING
88
X1767088
LOCK WASHER 12MM
31
X1767031
BUSHING
89
X1767089
EXT RETAINING RING 20MM
32
X1767032
SET SCREW M6-1 X 10
90
X1767090
HEX BOLT M8-1.25 X 20
36
X1767036
SPROCKET
91
X1767091
LOCK WASHER 8MM
37
X1767037
CHAIN (62S)
Summary of Contents for W1767
Page 33: ...30 Model W1767 For Machines Mfd Since 08 15 PARTS Notes...
Page 34: ...Model W1767 For Machines Mfg Since 5 07...
Page 37: ......