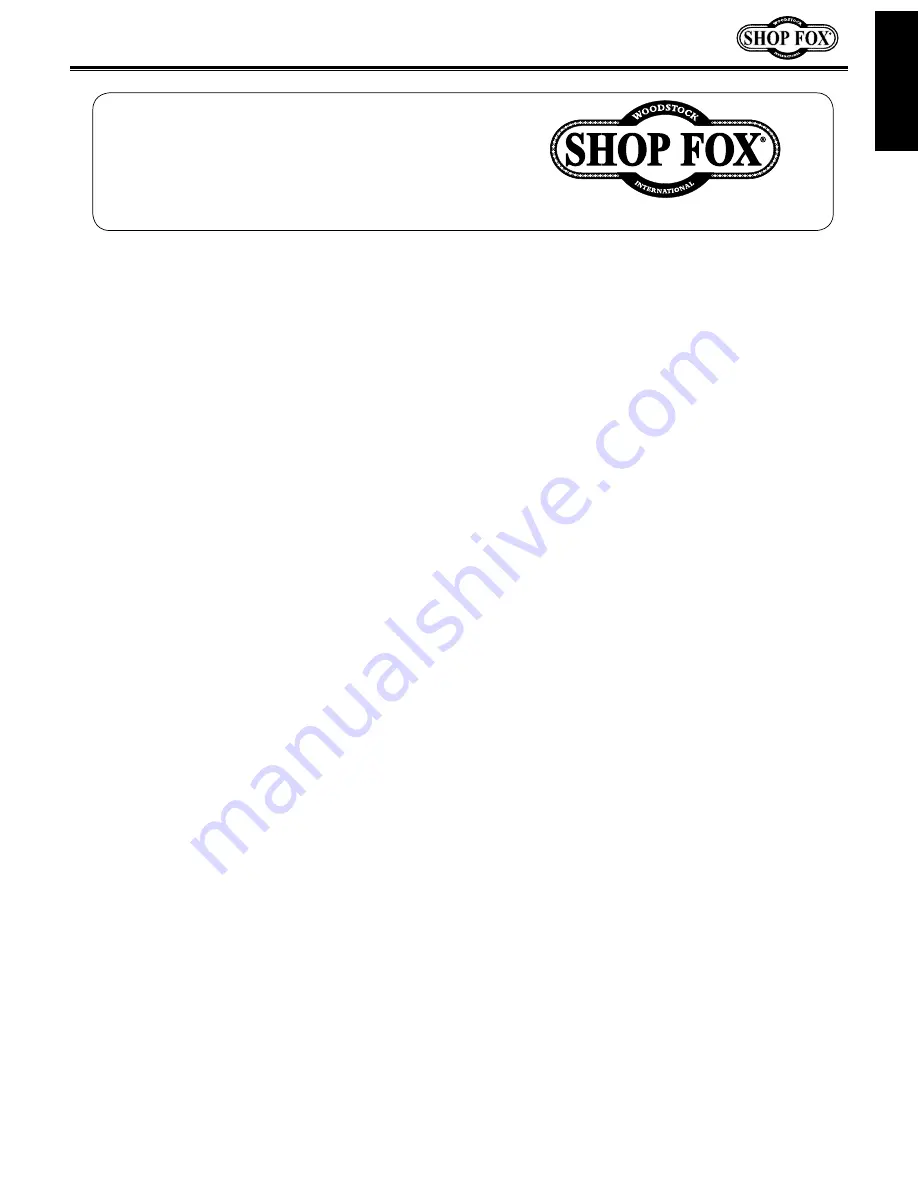
-3-
IN
TR
O
DU
CT
IO
N
Model W1764 (For Machines Mfg. Since 1/14)
MACHINE
SPECIFICATIONS
Phone #: (360) 734–3482 • Online Tech Support: tech–[email protected] • Web: www.shopfox.biz
MACHINE
SPECIFICATIONS
Motor
Type ................................................................................................. Universal Variable Speed
Horsepower .............................................................................................................. 1/8 HP
Voltage ...................................................................................................................... 120V
Prewired ..................................................................................................................... 120V
Phase ....................................................................................................................... Single
Amps ......................................................................................................................... 1.2A
Speed ............................................................................................................550—3300 RPM
Cycle ........................................................................................................................ 60 Hz
Number of Speeds .................................................................................................... Variable
Power Transfer ...................................................................................................... Gear Box
Bearings ................................................................................................... Lubricated for Life
Main Specifications
Operation Info
Minimum Workpiece Length ....................................................................................... 5 in.
Number of Feed Speeds ....................................................................................... Variable
Feed Speeds ................................................................................................. 6.5—39 FPM
Swing ............................................................................................................ 360 deg.
Vertical Movement ........................................................................................... 10-1/4 in.
Horizontal Movement ........................................................................................ 10-1/4 in.
Rotation .............................................................................................. Forward, Reverse
Roller Info
Number of Rollers ....................................................................................................... 3
Roller Width ................................................................................................... 1–3/16 in.
Roller Diameter ..................................................................................................... 3 in.
Roller Suspension Travel ...................................................................................... 5/16 in.
Maximum Height of Rollers ....................................................................................... 6 in.
Distance Between Rollers .................................................................................... 3–3/4 in.
Overall Dimensions
Weight.............................................................................................................. 20 lbs.
Length/Width/Height ................................................................................. 31 x 11 x 12 in.
Arm Diameter ................................................................................................. 15/16 in.
Construction Materials
Roller Construction ................................................................................. Synthetic Rubber
Housing Construction .................................................................................. Cast Aluminum
Supports Construction ................................................................................. Cast Aluminum
Column Construction .............................................................................................. Steel
Paint ................................................................................................................. Epoxy
MODEL W1764
1/8 HP POWER FEEDER
Model W1764 Specifications, Page 1 of 2, Last Updated 1/24/14