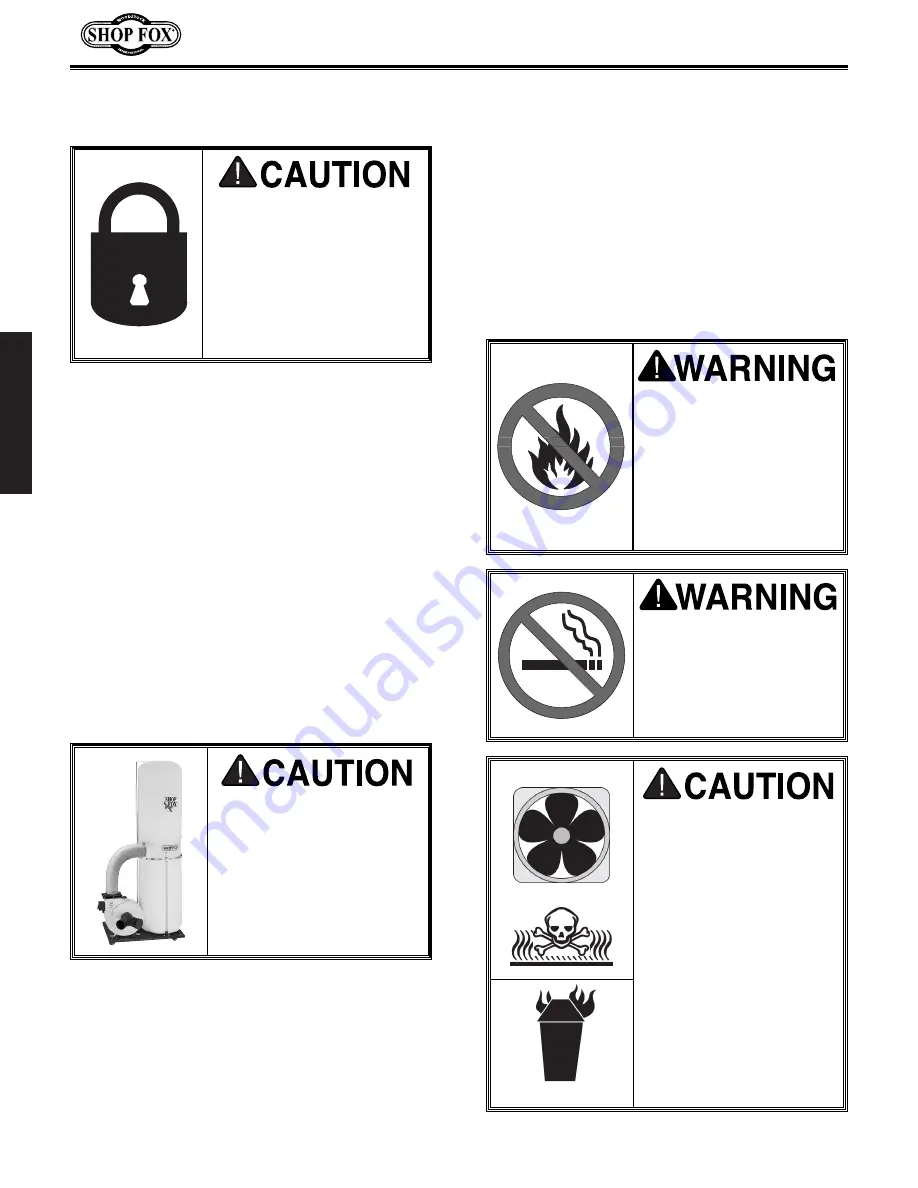
ASSEMBLY
-10-
•
Lighting:
Lighting should be bright enough
to eliminate shadows and prevent eye
strain.
•
Working Clearances:
Consider your current
and future shop needs with respect to the
safe operation of this machine.
•
Outlets:
Make sure the electrical circuits
have the capacity to handle the amperage
requirements for your Model W1712. Refer
to
page 8
for more information. Electrical
outlets should be located near the sander,
so power or extension cords are clear of
high-traffic areas.
The exposed and unpainted sander surfaces are
coated with a waxy oil to prevent rust during
storage and shipment. DO NOT use chlorine
based solutions or solvents to remove this waxy
oil or you will damage the painted surfaces.
Remove the waxy oil with a solvent based
degreaser before you use the sander. Always
follow all usage and safety instructions of the
product that you are using.
ONLY ALLOW TRAINED
PEOPLE in your shop! Make
sure shop entrances are
locked and machines are
correctly turned off with
lock-out devices when not
in use. Otherwise, injury
or death can occur.
DO NOT use flammables
such as gas or other
petroleum-based solvents
to clean your machine.
These products have low
flash points and present
the risk of explosion and
severe personal injury!
DO NOT smoke while
using cleaning solvents.
Smoking may cause
explosion or risk of fire
when exposed to these
products!
ALWAYS work in a well
ventilated area when
using solvents with
fumes, and keep away
from any potential igni-
tion sources (pilot
lights). Most solvents
used to clean machinery
are toxic when inhaled
or ingested. Always dis-
pose of waste rags in a
sealed container to
make sure they do not
cause fire or environ-
mental hazards.
For information on the correct dust collection
components for sanders, contact your
Woodstock International dealer for a copy of
the Dust Collection Basics handbook and avail-
able accessories.
Some wood dust may
cause allergic reactions
or respiratory illness.
Use a dust collection sys-
tem and respirator in
your shop to help protect
yourself from these long-
term hazards.
Initial Cleaning
Dust Collection
Shop Preparation
Summary of Contents for SHOP FOX W1712
Page 37: ...PARTS 25 76 68 1 57 66 58 76 68 1 55 66 58 55 57 66 58 68 66 30 30 31 105 113 31 PARTS...
Page 41: ...PARTS 29 Notes...
Page 42: ...PARTS 30 Notes...
Page 45: ......
Page 46: ......