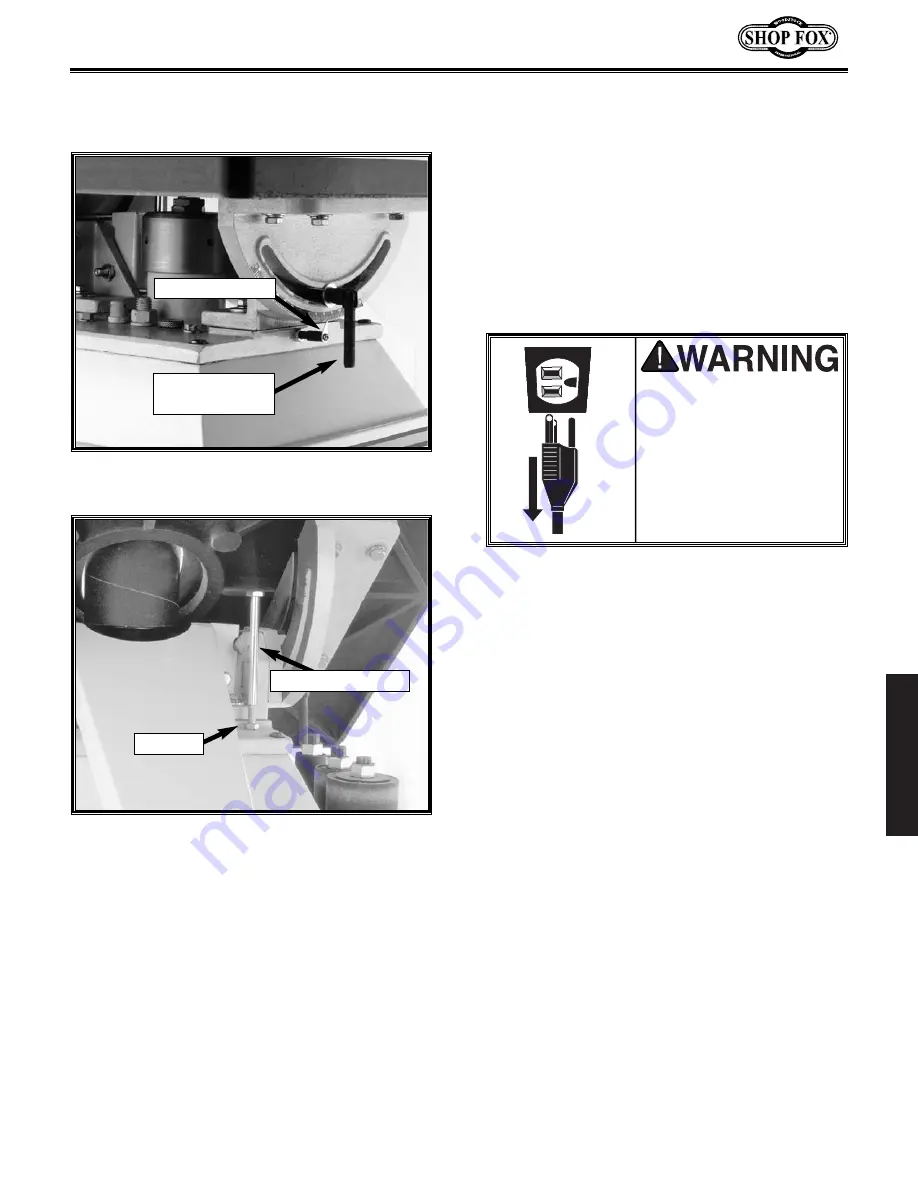
ADJUSTMENTS
-19-
ADJUSTMENTS
Figure 15.
Loosen the locking handles on the
trunnions.
Locking Handle
(1 of 2)
Retainer Screw
Positive Stop Bolt
There is a positive stop bolt located under the
back right-hand side of the table. When adjust-
ed correctly, this stop allows the table to be
returned square to the spindle with speed and
accuracy.
To adjust the positive stop bolt:
1.
Loosen both locking handles (
Figure 15
)
located on each side of the table trunnion
assembly and tilt the table forward.
2.
Loosen the jam nut and lower the head of the
positive stop bolt as shown in
Figure 16
.
The
positive stop bolt is located on the back left
corner of the machine.
Make sure that your
machine remains
unplugged during any
adjustments or mainte-
nance procedures.
Ignoring this warning may
result in serious personal
injury!
Figure 16.
Loosen the jam nut to allow the
positive stop bolt to be adjusted.
Jam Nut
Positive Stop Bolt