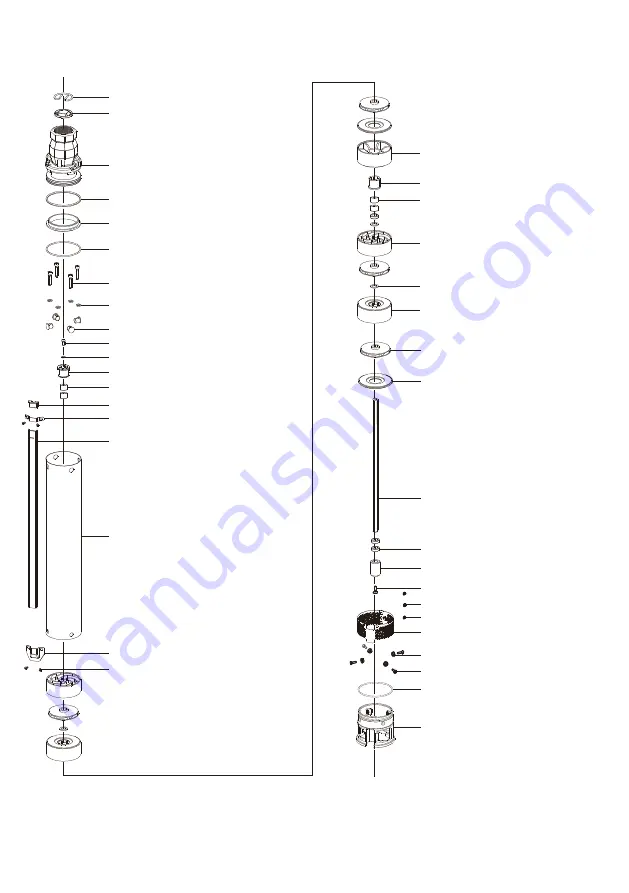
1 Inlet joint
2 Oring
7 Screw and spring washer set
8 Countersunk head screw
Pump Part of SE (m) Series
III. Structure diagram
3 Countersunk head screw
4 Locating bush
5 Mesh enclosure
6 Screw
9 Coupling
10 Sleeve
11 Pump Shaft
12 Guide vane cover
13 Impeller
14 Fluid director
15 Wear washer
16 Guide vane
17 Ceramic shaft sleeve
18 Middle rubber bearing
19 Middle bearing block
20 Screw
21 Small press plate (ii)
22 Pump sleeve
23 Press plate for the cable
24 Small press plate (i)
25 Cable sheath
26 Ceramic shaft sleeve
27 Rubber bearing
28 Spring washer
29 Screw
30 Locating pin
31 Spring washer
32 Screw
33 Oring
34 Discharge chamber back ring
35 Adjusting washer
36 Discharge chamber
37 Valve cover
38 Retaining ring