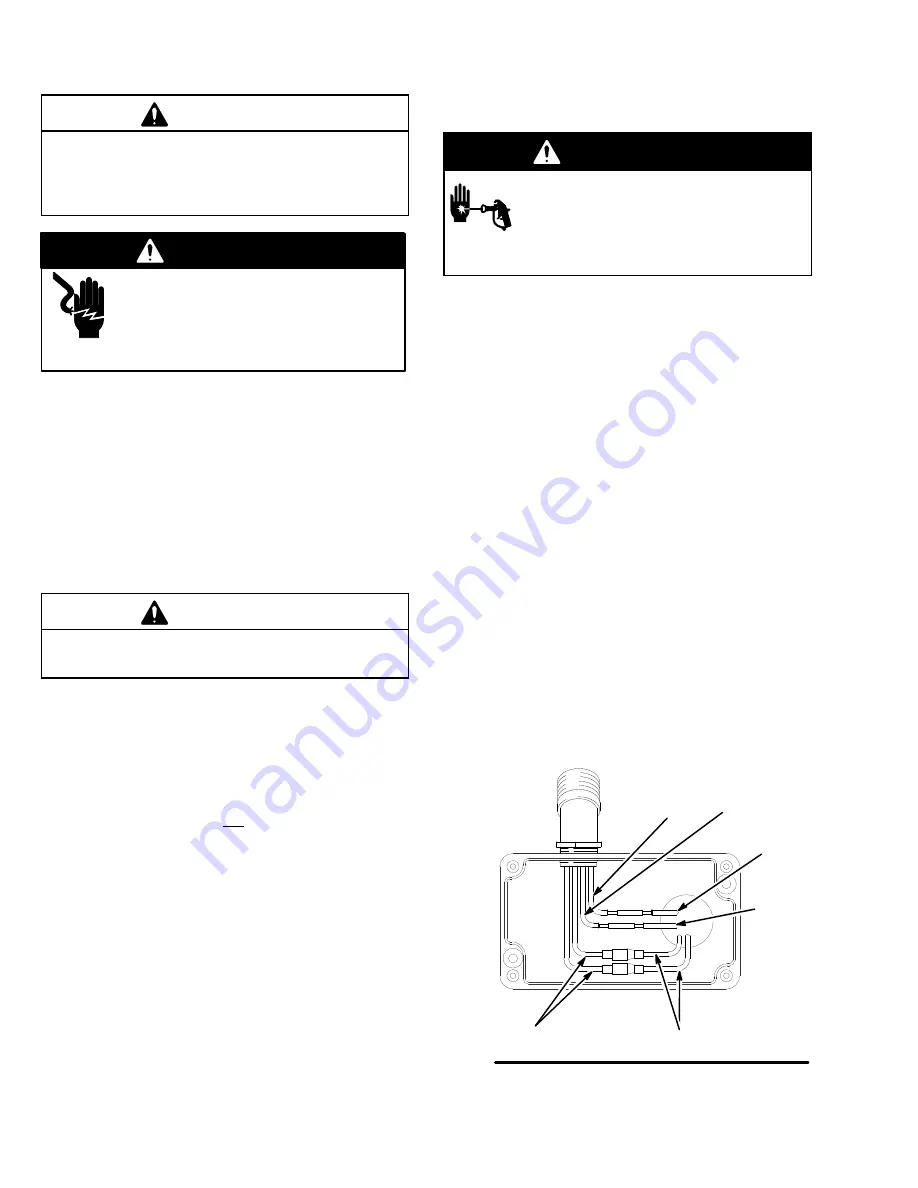
16
824-033
Pressure Control
CAUTION
Do not install the pressure control until motor is
checked. A defective motor may damage the pres-
sure control. Make sure to test the motor prior to
pressure control installation.
WARNING
ELECTRIC SHOCK HAZARD
To reduce the risk of Electric Shock: wait
5 minutes after turning sprayer off before
servicing to allow stored current to dis-
charge.
Motor Test
With motor shield off and four motor leads discon-
nected:
1.
Check continuity with multimeter from each black
motor lead to ground (one at a time). Any reading
less than infinite resistance – even very high re-
sistance – means motor is shorted to ground. Re-
place motor.
CAUTION
A motor that is shorted to ground will damage the
pressure control.
2.
Remove fan cover from motor.
3.
Remove pump pin ( See page 15 for instructions to
remove pin).
4.
With black motor leads not connected, use motor
fan to spin motor quickly. Motor should spin freely
in both directions. If not, replace motor.
5.
Connect black motor leads together.
6.
Use motor fan to turn motor. It should be much
harder to turn than in step 4. If there is uneven or
no resistance to turning, check brushes and re-
place if necessary.
7.
If there is still uneven or no resistance to turning,
replace motor.
8.
Install pump pin and fan cover.
WARNING
INJECTION HAZARD
To reduce the risk of serious injury,
whenever you are instructed to relieve
pressure, follow the Pressure Relief
Procedure on page 7.
1.
Relieve pressure.
2.
Remove ten screws (64) and motor shield (14).
See Fig. 15 and parts list, except as noted.
3.
Loosen outlet cover on pressure control wiring
box. Disconnect motor leads. See Fig 14.
4.
Loosen black conduit (22) from pressure control
fitting and pull out wires
5.
Remove hose (47) from rear of pressure control
(116).
6.
Remove hose (121) and 45
swivel union (119)
from front of pressure control (116).
7.
Support pressure control (116) and carefully re-
move motor mount screws (37). Remove pressure
control.
8.
Install new pressure control (116) with screws (37).
9.
Continue to assemble sprayer.
7145A
Fig 14
Yellow
Red
Black
Black/White
Black
Black/
White
Summary of Contents for ULTIMATE 824-030
Page 27: ...Notes...