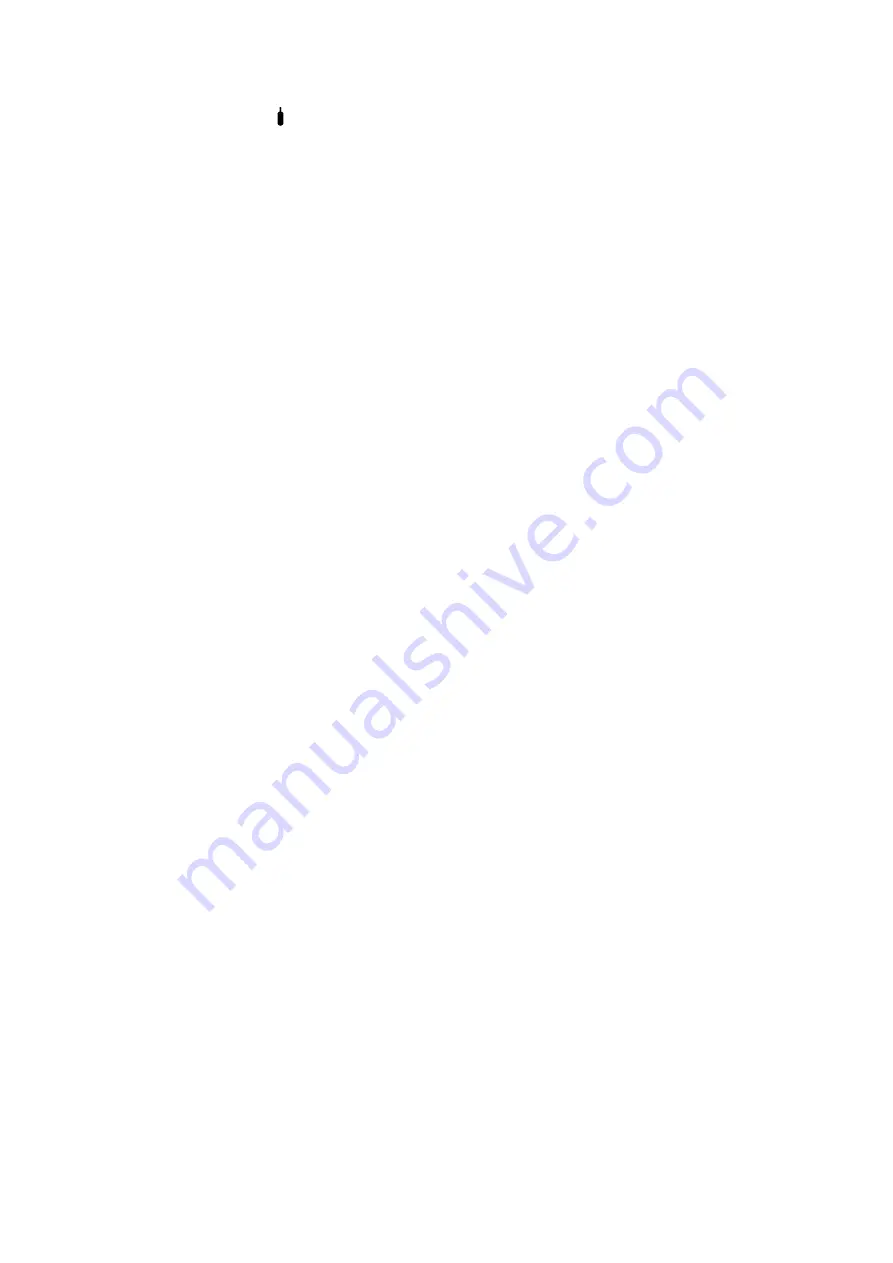
11
Gas pre-flow time ( ) -
time from pressing the button on the handle of the handle and opening the gas valve until the arc strikes. Usually it should be
Gas pre-flow time ( ) -
time from pressing the button on the handle of the handle and opening the gas valve until the arc strikes. Usually it should be
Gas pre-flow time ( ) -
time from pressing the button on the handle of the handle and opening the gas valve until the arc strikes. Usually it should be
Gas pre-flow time ( ) -
time from pressing the button on the handle of the handle and opening the gas valve until the arc strikes. Usually it should be
longer than 0.5 s to provide shielding gas to the torch nozzle outlet to shield the welding start and the tungsten electrode. For a longer gas supply pipe
from the cylinder, the pre-flow time should be longer.
Adjustment range: 0.1 - 15s.
Inrush current (
I Start) - current appearing in the circuit after pressing the button on the handle of the handle. The higher the starting current, the
Inrush current (
I Start) - current appearing in the circuit after pressing the button on the handle of the handle. The higher the starting current, the
easier it will be to look at the arc. However, when welding thin sheets, too high an initial current can lead to burning of the sheet. In some welding
modes, the current does not increase to heat the work piece. Adjustment range: 5 - 200A.
Welding current (
Current) Adjustment
Welding current (
Current) Adjustment
range: 5 - 200A.
Pulse width (
PULSE Duty) - pulse duration, allows you to adjust the depth of penetration. The increase in width increases the depth of penetration, the
Pulse width (
PULSE Duty) - pulse duration, allows you to adjust the depth of penetration. The increase in width increases the depth of penetration, the
reduction limits the amount of heat introduced into the material, reducing the risk of burning thinner sheets or smaller elements.
Lower pulse width values should be used for higher currents. A larger pulse width should be used for small currents, for example a width above 50%
should be used for currents below 100A.
Adjustment range: 10 - 90%.
Base current (
Base Current) - current responsible for maintaining the welding process, lower value of the current pulse. Facilitates the control of the
Base current (
Base Current) - current responsible for maintaining the welding process, lower value of the current pulse. Facilitates the control of the
amount of heat introduced into the material. Base current adjustment is only possible during pulse welding. Adjustment range: 10 - 90% of welding
current.
Falling time (
Slope Down) - welding current decrease time from the set value to zero or the crater current value. Adjustment range: 0 - 15s.
Falling time (
Slope Down) - welding current decrease time from the set value to zero or the crater current value. Adjustment range: 0 - 15s.
Crater current (
I Stop) - current used in some welding modes when the arc is not quenched immediately after the welding current has fallen. It allows
Crater current (
I Stop) - current used in some welding modes when the arc is not quenched immediately after the welding current has fallen. It allows
you to fill the crater and the end of the weld. Adjustment range: 5 - 200A.
Rise Time (
Slope Up) - welding current rise time from the initial current to the set welding current value. Adjustment range: 0 - 15s.
Rise Time (
Slope Up) - welding current rise time from the initial current to the set welding current value. Adjustment range: 0 - 15s.
Pulse frequency (
PULSE Frequency) - the frequency with which the value of the current pulse changes between the welding current and the
Pulse frequency (
PULSE Frequency) - the frequency with which the value of the current pulse changes between the welding current and the
base current.
Adjustment range: 0.5 - 999 Hz, 200 Hz is recommended as standard.
Gas post-flow time -
time from quenching the arc to closing the gas valve to shield the solidifying weld pool from air and to cool the tungsten
Gas post-flow time -
time from quenching the arc to closing the gas valve to shield the solidifying weld pool from air and to cool the tungsten
Gas post-flow time -
time from quenching the arc to closing the gas valve to shield the solidifying weld pool from air and to cool the tungsten
electrode. Too short an afterflow time can result in weld oxidation. When welding in TIG AC (alternating current) mode, this time should be longer.
Adjustment range: 0.1 - 15s.
10. WELDING
10.1 Welding with coated electrode (MMA)
10.1.1 Arc initiation
Arc initiation when welding with coated electrodes involves touching the electrode to the workpiece, short rubbing and tearing. In the case of arc
initiation with electrodes, which the coating forms after solidification