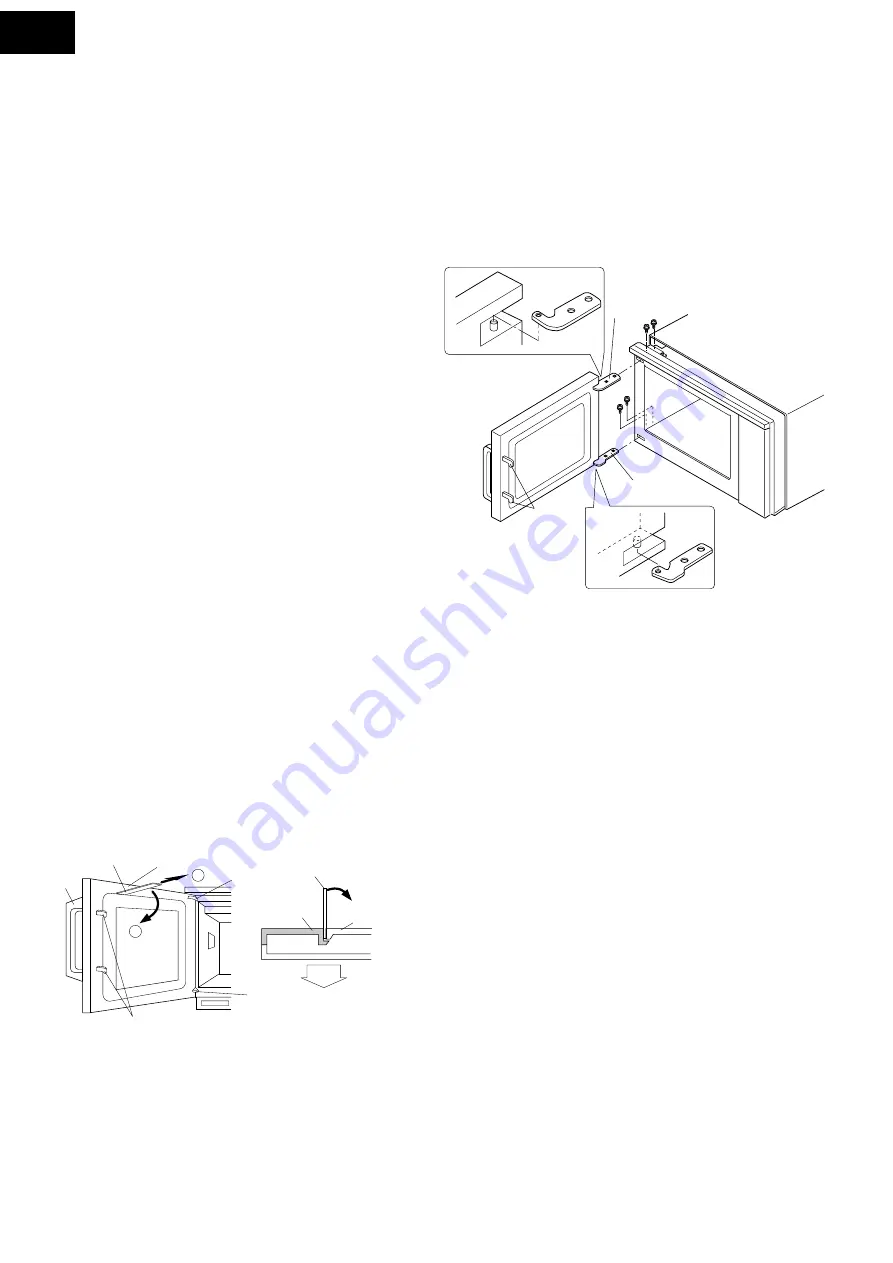
R-25JT-F
36
UPPER
OVEN HINGE
LOWER
OVEN HINGE
CHOKE COVER
DOOR
HANDLE
LATCH HEAD
BENT
2
1
PUTTY KNIFE
PUTTY KNIFE
CHOKE COVER
DOOR PANEL
FRONT
BENT
Note: After any service to the door;
(A) Make sure that door sensing switch, secondary
interlock switches (1), (2) and monitor switches (1), (2)
are operating properly. (Refer to chapter "Test
Procedures".).
(B) An approved microwave survey meter should be used
to assure compliance with proper microwave radiation
emission limitation standards.
DOOR ADJUSTMENT
Door adjustment is performed with the door properly installed
and closed and while the oven hinges are loose.
1. Loosen upper and lower oven hinges with phillips head
screw driver.
2. Adjust the door by moving it vertically so that the top right
hand corner of the door is in line with the top of the control
panel frame assembly.
3. Tighten the upper and lower oven hinge screws.
After adjustment, make sure of the following:
1. Door latch heads smoothly catch the latch hook through the
latch holes, and the latch head goes through the center of
the latch hole.
2. Deviation of the door alignment from horizontal line of cavity
face plate is to be less than 1.0mm.
3. The door is positioned with its face depressed toward the
cavity face plate.
4. Re-install outer case and check for microwave leakage
around door with an approved microwave survey meter.
(Refer to Microwave Measurement Procedure.)
Note: The door on a microwave oven is designed to act as an
electronic seal preventing the leakage of microwave
energy from oven cavity during cook cycle.
This function does not require that door be air-tight,
moisture (condensation)-tight or light-tight. Therefore,
occasional appearance of moisture, light or sensing
of gentle warm air movement around oven door is not
abnormal and do not of themselves, indicate a leakage
of microwave energy from oven cavity. If such were
the case, your oven could not be equipped with a
vent, the very purpose of which is to exhaust the
vapor-laden air from the oven cavity.
Figure C-4. Door Replacement
OUTER CASE
CABINET
UPPER
OVEN HINGE
LOWER
OVEN HINGE
LATCH
HEADS
3. Remove choke cover from door panel, referring to "CHOKE
COVER REMOVAL".
4. Remove two (2) screws holding the door handle to door.
5. Remove the door handle from door panel.
6. Now, door handle is free.
UPPER AND LOWER LATCH HEADS REMOVAL
7. Remove the door release lever from the door assembly.
8. Remove the three (3) screws holding the joint plate to the
door panel.
9. Release the latch spring from the tab of the joint lever and
joint plate.
10. Release the latch heads from joint lever and joint plate.
11. Now, the latch heads are free.
DOOR CASE REMOVAL
1. Remove the door assembly from oven cavity, referring to
"DOOR REMOVAL".
2. Remove choke cover from door panel, referring to "CHOKE
COVER REMOVAL".
3. Remove door handle from door panel, referring to "DOOR
HANDLE REMOVAL".
4. Bend up four (4) nails of door case.
5. Remove door case from door panel.
6. Now, the door case is free.
DOOR GLASS REMOVAL
7. Remove the four (4) screws holding two (2) outside window
fixing plates to door panel.
8. Now, the door glass is free.
DOOR DISASSEMBLY
CHOKE COVER REMOVAL
1. Open the door and insert a putty knife (thickness of about
0.5mm) in gap between the choke cover and corner portion
of door panel to free engaging parts. Refer to Fig. C-5.
NOTE:As the choke cover and door panel are engage at 16
places, do not force any perticular part.
2. Remove the choke cover carefully. (If choke cover is
broken, replace with a new one.)
Figure C-5. Choke cover
DOOR COMPONENTS REMOVAL
DOOR HANDLE REMOVAL
1. Remove the door assembly from oven cavity, referring to
"DOOR REMOVAL".
2. Place door assembly on a soft cloth with latches facing up.