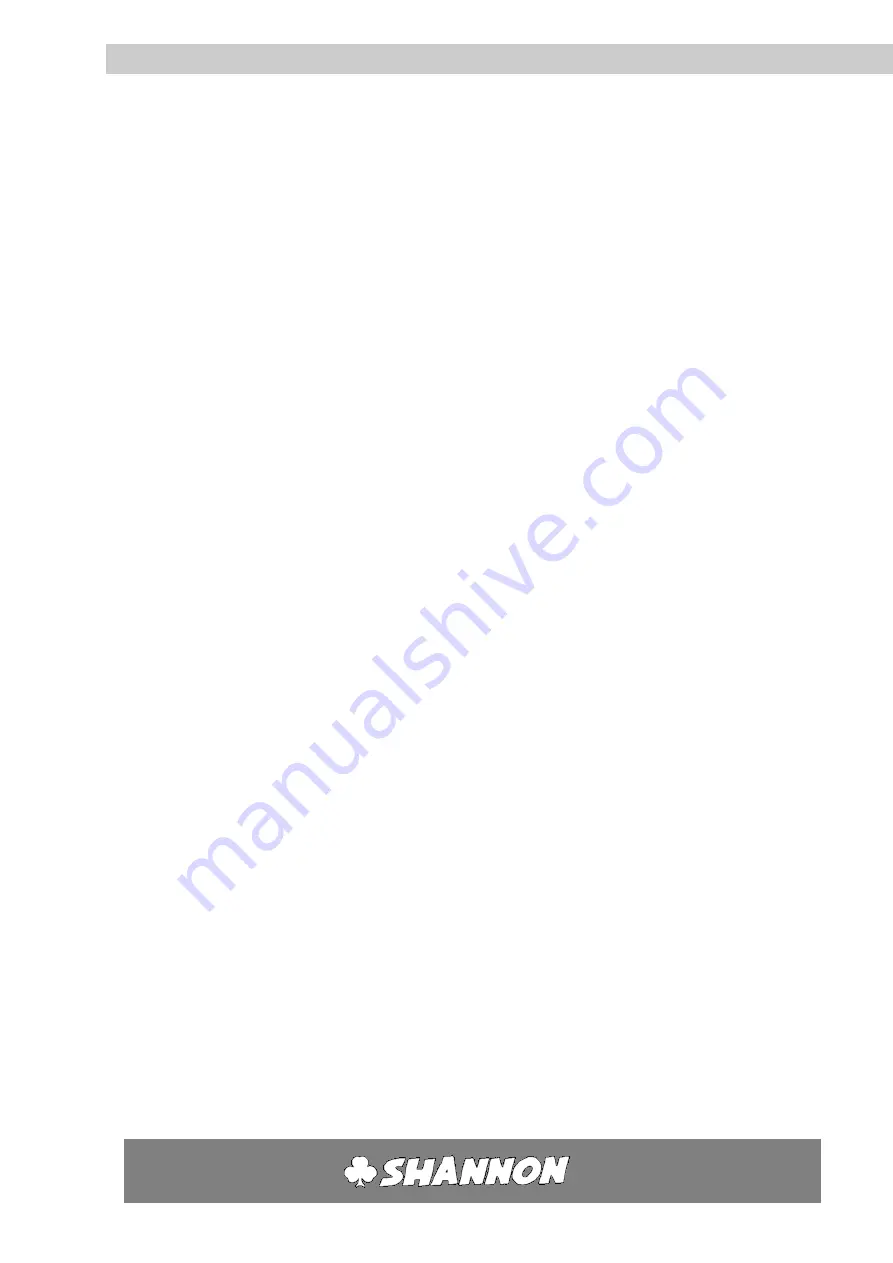
User’s Guide
HRT 65-125
-
20
-
hs
Annex
A
ACCESORIES
Shannon BV
can supply various accessories and production
equipment for the processing of plastic sheets.
Working length reducing set
Working length reducing set for heating one or more zones per bending
time.
Foil bending profile
A contact profile with anti-stick coating, suitable for bending thin sheets from
0.3
– 2mm.
Profile length:
500, 650, 1.000 and 1.250 mm.
Ridge widths:
1 to 10 mm.
Number of ridge widths:
Single and double.
Special versions:
On request.
Mould
In which to allow the bent product to cool. Adjustable to any desired angle.
Available lengths:
650, 1.250, 2.200 and 3.000 mm.
EQUIPMENT
Flame polishing equipment
To provide a glossy finish to edges, holes and slots in clear acrylic sheets.
Diamantpoliermaschinen
To provide a glossy finish to edges of acrylic sheets up to 20 mm
thickness.
With ground tracks and adjustable feed speed control.
Also available with specially developed frame for stable feed of long
sheets.