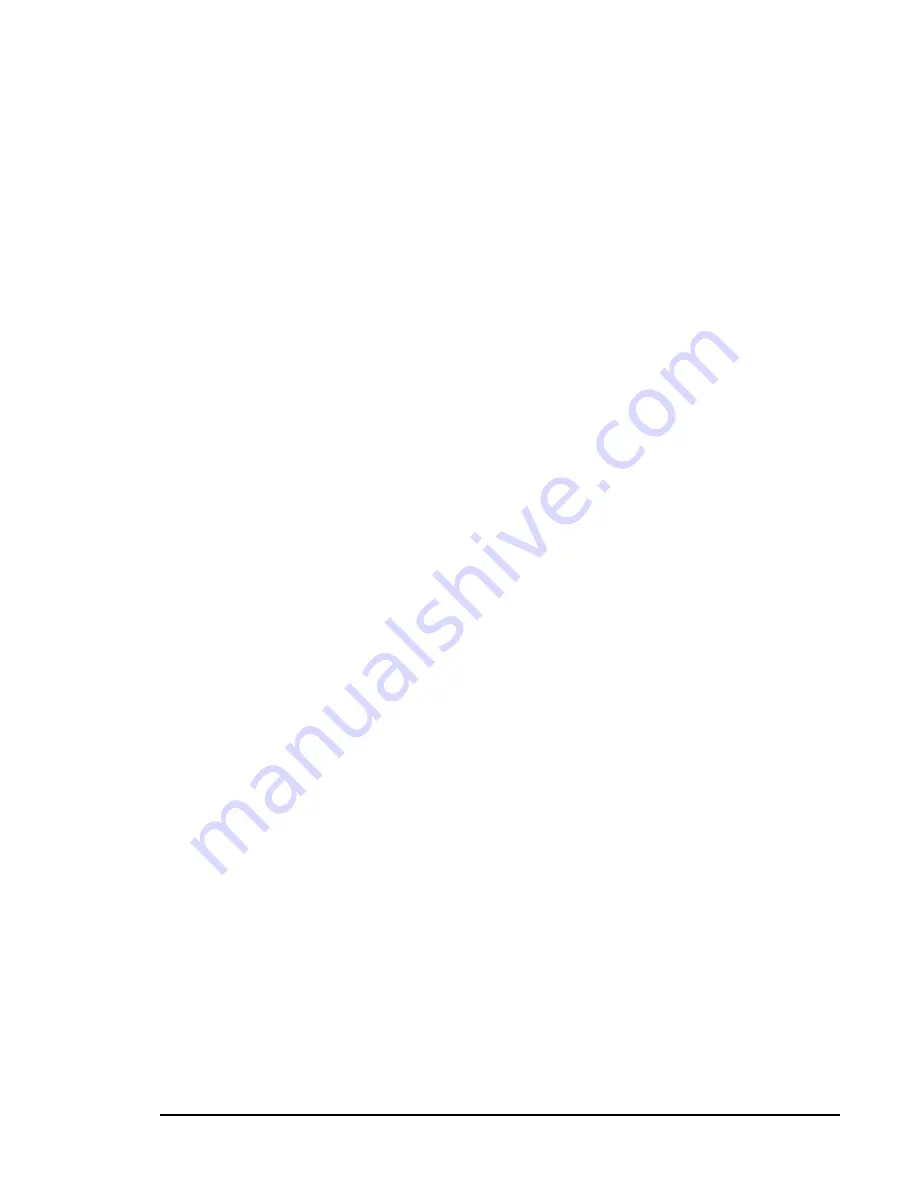
Sample Gas Preparation and Delivery DF-310E
41
long periods of time (between 6 and 24 months) where steel cylinders should
be recalibrated every three months.
6.5.2 Calibration Cylinder Regulators
Regulators used on bottled calibration standards are typically equipped with
two Bourdon pressure gauges, one to measure the cylinder pressure, and the
other to measure the outlet pressure. The regulator must have a metal
(preferably stainless steel) diaphragm. Install a flow control valve after the
regulator to adjust the flow.
6.5.3 Purge Procedure
Before the calibration gas is connected to the analyzer follow the procedure
listed below to purge ambient air from the regulator which prevents
contamination of the gas in the cylinder rendering it useless:
After securely attaching the regulator to the cylinder,
1. Open the regulator flow control valve slightly.
2. Open the cylinder valve.
3. Set the regulator to its maximum delivery pressure.
4. Adjust the flow control valve to allow a modest flow rate
(hissing sound).
5. Close the cylinder valve until the cylinder pressure falls to
zero. If equipped with gauges, allow the secondary (output)
gauge to approach zero. Otherwise wait for the hissing to
nearly stop.
6. Immediately open the cylinder valve to restore full delivery
pressure.
7. Repeat steps 5 and 6 five to ten times to thoroughly purge the
regulator and gauges.
8. Close the shut off valve on the outlet side of the regulator to
isolate the purged regulator from atmospheric contamination.
9. Set the delivery pressure to 5 psig (15 psi for welded sample
line with VCR connection.
Once the regulator is mounted and purged, do not remove it from the cylinder
until a fresh cylinder is required.
6.5.4 Sample Gas Delivery and Vent Pressure during
Calibration
The most accurate calibration is obtained when the analyzer is plumbed into
the gas sample system so that the analyzer is under actual process operating
conditions. But when the process sample is being delivered to the analyzer
under Vacuum conditions, or being returned from the sample outlet under
either positive pressure or Vacuum conditions the operating pressure at the
sensor is likely to be quite different than under factory calibration conditions.
For systems where the gas sample is not vented to atmosphere, the analyzer
outlet should remain connected in the same manner during calibration, if
possible. This ensures that downstream pressure effects on the sensor are the
Summary of Contents for DF-310E
Page 1: ...Oxygen Analyzer DF 310E OPERATOR MANUAL...
Page 10: ......
Page 26: ...22 DF 310E Options Figure 7 Plumbing Configuration Options...
Page 36: ......
Page 62: ......
Page 66: ...62 DF 310E User Interface 3 43 ppm...
Page 96: ......
Page 108: ......
Page 118: ......
Page 122: ......
Page 124: ......
Page 129: ......