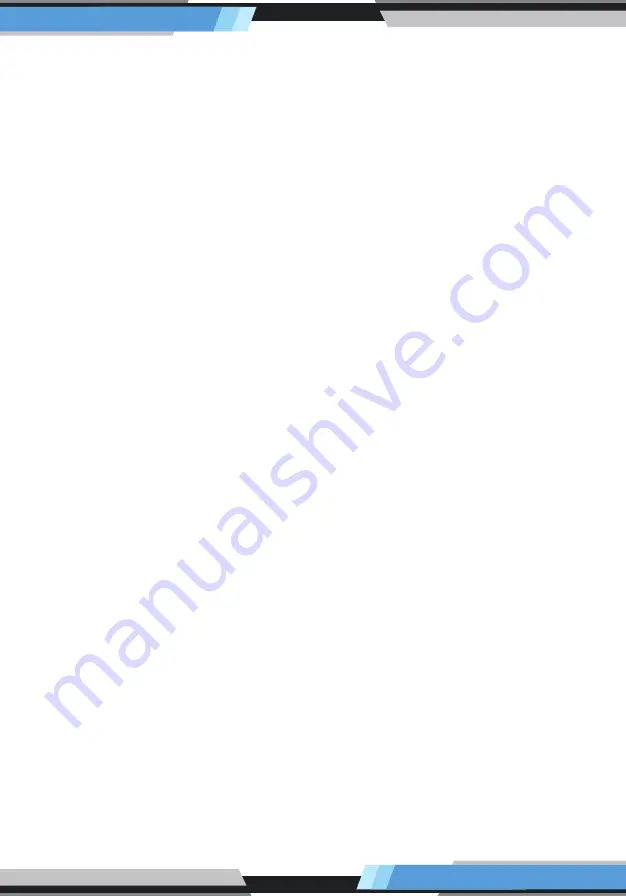
FIRE PRECAUTIONS
•
All flammable materials
MUST
be removed from the welding area.
•
DO NOT
strike an Arc on or near the gas cylinder.
•
DO NOT
attempt to weld fuel or gas containers unless adequate procedures have
been taken to ensure that no vapour remains. Fuel tanks should be thoroughly
steam cleaned before welding.
WELDING FUMES
Toxic gases are given off during the MIG welding process. Always use in a well
ventilated area.
ARC GLARE
Always use face shield or welding helmet fitted with the correct glass filter.
Never use damaged safety equipment.
HEAT
Wear welding gloves at all times whilst welding. They will protect the hands from
ultra-violet radiation and direct heat of the arc. It is also recommended that overalls
are worn.
ADDITIONAL PROTECTIVE CLOTHING
•
When welding at higher settings wear a leather apron to protect the operator
from spatter
•
When welding in the overhead position, a suitable cap should protect the head
and neck.
•
We recommend that you wear industrial foot wear including steel toes caps.
IMPORTANT:
1. These units should never be exposed to rain or snow.
2. Do not use in a wet or damp environment.
3. Never use to thaw or heat up frozen pipes.
4. These unit should be connected to the mains supply through a circuit breaker.
www.SereneLifeHome.com
3