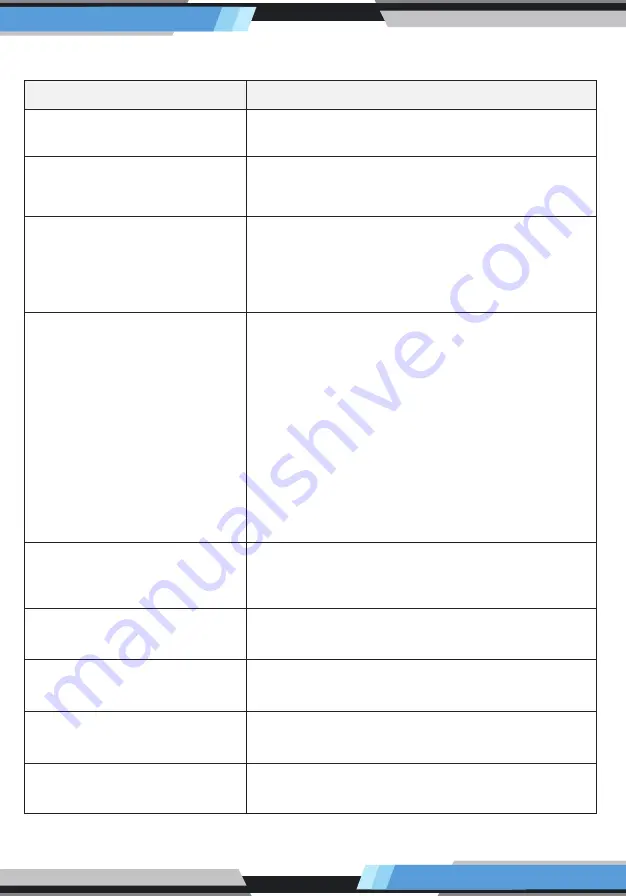
TROUBLESHOOTING
www.SereneLifeHome.com
11
PROBLEM
POSSIBLE CAUSES
Weld deposit too thick
• Welding voltage too low.
• Torch moved over the work piece too slowly.
Weld deposit incomplete
and stringy
• Torch moved over the work piece too quickly.
Rust, paint or grease on the work piece.
Arc unstable, excessive spatter
and weld porosity
• Torch held too far from the work piece.
• No gas - check bottle content, connections and
regulator settings.
• Incorrect gas for material.
Wire repeatedly burns back
•
Torch held too close to the work piece.
•
Break in the welding circuit
Possible causes:
•
Incorrect size of contact tip for wire.
•
Contact. tip damaged - replace.
•
Contact tip loose - tighten.
•
Feed rollers worn - replace.
•
Welding wire corroded - replace.
•
Pressure roller adjustment incorrect - adjust.
•
Pressure roller sticking - lubricate or replace.
•
Wire tangled on reel
Lack of weld penetration
• Welding output too low.
• Wire feed speed too low.
• Torch moved too fast.
Burning holes in work piece
• Welding out put too high.
• Torch moved erratically 0r too slowly.
No arc produced
• Earth lead or torch cable in open circuit.
• Poor earth clamp connection
Welder does not operate
(mains indicator not lit)
• Check mains connection.
• Check supply fuse.
Welder does not operate with
trigger pressed
• Check torch trigger and it's connecvtions.
• Thermal overload cut out - allow to cool.