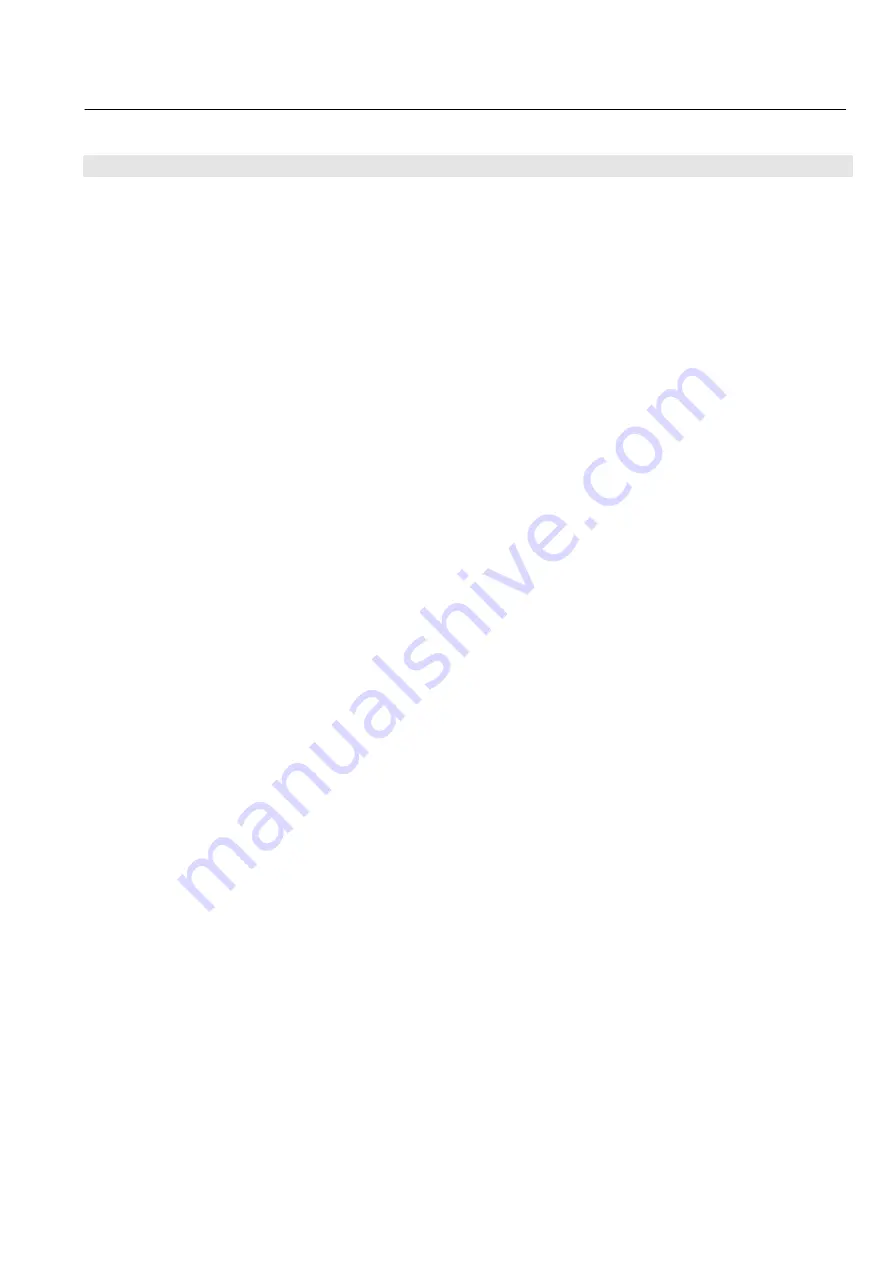
Technical Manual
Absolute Single/Multiturn Encoders
Profibus
R.000.000
1-4 of 22
1
1
General
General
PROFIBUS
‐
DP
basics
This
description
provides
information
concerning
the
implementation
of
the
PROFIBUS
‐
DP
transmission
protocol
in
the
slave
mode
in
our
devices.
It
should
be
noted
that
the
extent
of
the
functions
described
might
be
limited
according
to
the
device
or
application.
With
protocol
conversions
in
particular,
as
a
rule
fewer
functions
are
used!
The
profile
required
The
link
between
the
decentralized
process
operation
and
the
central
control
via
the
communication
system
takes
place
in
the
lowest
hierarchy
level
on
the
filed
or
process
bus.
At
this
level,
the
main
requirements
are
a
simple
protocol
operation
and
short
data
transmission
times
for
the
communication.
This
ensures
the
fastest
system
reaction
time
to
the
dynamic
states
of
the
peripherals.
In
addition
to
the
classic
data
exchange,
the
acyclic
transmission
of
parameter,
diagnostic
and
configuration
data
must
be
possible,
without
radically
impeding
the
real
‐
time
capability
of
the
bus.
This
is
the
only
way
to
guarantee
the
achievement
of
good
diagnostics
and
safe
operation.
Characteristics
The
main
task
of
PROFIBUS
‐
DP
is
the
cyclic
transmission
of
the
process
data
from
the
control
system
to
the
peripheral
equipment
and
vice
versa.
The
access
procedure
uses
the
Master
‐
Slave
principle.
Here
in
the
polling
operation
a
Master
communicates
with
its
assigned
slave
devices
one
after
the
other
on
the
bus.
A
data
exchange
is
initiated
by
a
request
telegram
and
ended
by
an
acknowledgement
telegram
from
the
Slave
concerned.
So,
each
Slave
only
becomes
active
after
a
call
from
the
Master.
This
avoids
a
simultaneous
bus
access.
The
hybrid
access
procedure
of
PROFIBUS
allows
a
combined
operation
of
several
bus
masters
and
even
a
mixed
operation
of
PROFIBUS
‐
DP
and
PROFIBUS
‐
FMS
within
a
bus
section.
However
the
pre
‐
requisition
for
this
is
the
correct
configuration
of
the
bus
system
and
the
unambiguous
assignment
of
the
Slave
devices
to
the
Masters.
PROFIBUS
‐
DP
distinguishes
two
types
of
Master.
The
Class
1
Master
carries
out
the
cyclic
transmission
of
the
operating
data
and
supplies
the
user
data.
The
Class
1
Master
can
be
addressed
by
a
Class
2
Master
using
certain
functions.
Direct
access
to
the
Slaves
is
not
permitted.
The
functions
are
limited
to
support
services
such
as
reading
the
diagnostic
information
of
the
slaves.
A
Class
2
Master
is
thus
also
understood
as
a
programming
or
diagnostic
device.
Protective
functions
PROFIBUS
‐
DP
is
equipped
with
many
protective
functions.
These
ensure
safe
fault
‐
free
communication
not
only
in
the
harsh
environment
of
the
decentralised
peripheral
equipment,
but
also
in
the
case
of
external
interference
or
the
failure
of
one
or
more
stations.
Wrong
parameter
settings
are
recognized
directly,
in
that
stations
having
the
wrong
parameters
are
not
integrated
in
the
operating
data
exchange.
The
Master
records
the
failure
of
any
station
and
indicates
this
to
the
user
by
means
of
a
general
diagnostic
message.
Any
breakdown
in
the
transmission
path
is
detected
by
the
Slave
by
means
of
time
monitoring
and
leads
to
the
outputs
being
switched
off.
EMV
disturbances
are
virtually
filtered
out
by
means
of
the
difference
signal,
thanks
to
the
particularly
noise
‐
immune
RS485
transmission
system.
Data
transmission
errors
are
recognized
thanks
to
frame
and
check
‐
sum
controls
and
lead
to
the
retransmission
of
the
telegram.