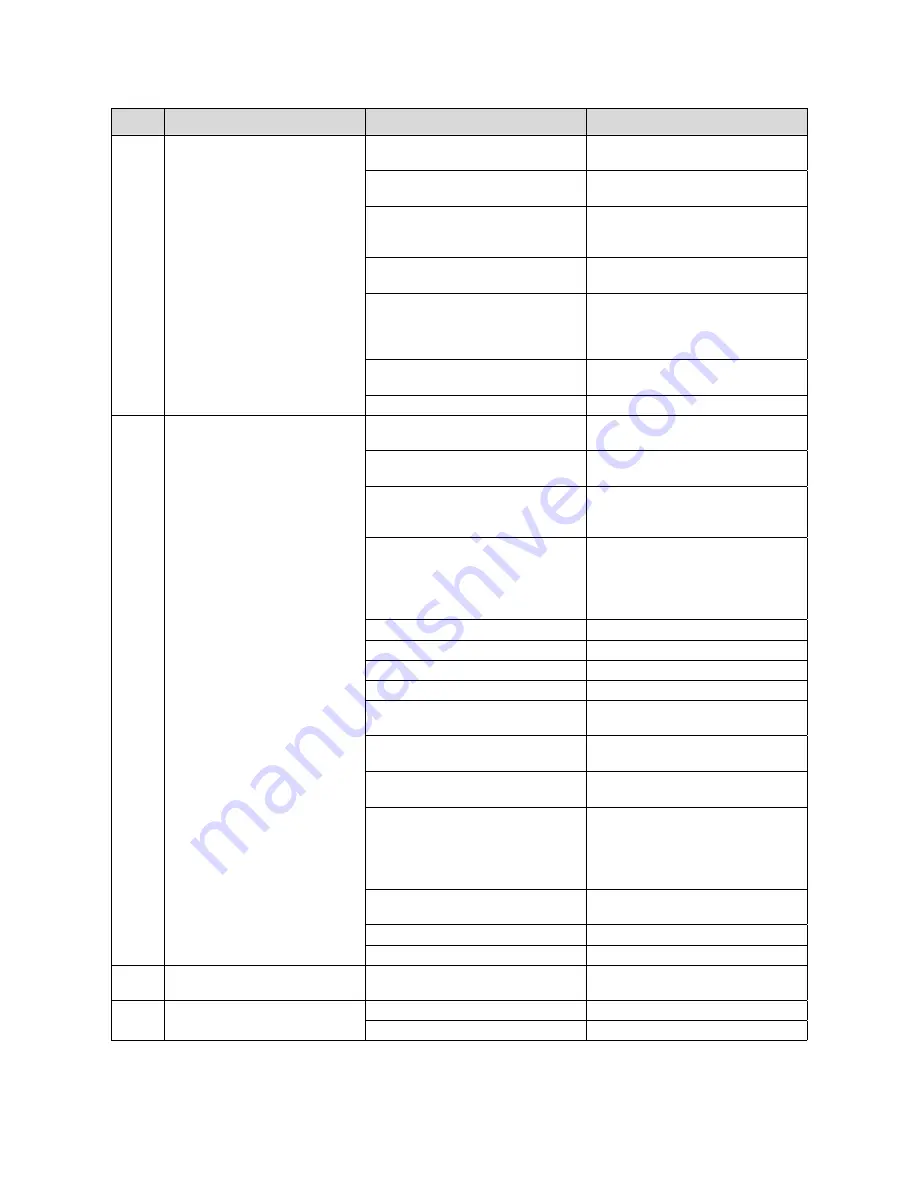
31
6.5 Troubleshooting
Problem
Probable cause
Action
6.5.1
”The sail will not unfurl or will only
partly unfurl.”
• The jib halyard is wrapped around the
luff extrusion.
• Ease the halyard slightly and try to
reverse the system.
• Another halyard is wrapped around the
luff extrusion.
• Furl the system. Free the halyard.
• The halyard shackle/knot interferes
with the top extrusion.
• Make sure tht the 15-20º requirement
is fulfilled. Check that the shackle/knot
arrangement is not too ”bulky”.
• The furling line is not free to run or has
become tangled.
• Slacken or free the furling line.
• The forestay is too slack.
• Tension the forestay, first of all by
tensioning the backstay and/or the cap
shrouds. If this doesn’t help, decrease
the length of the Furlex-system.
• Dirt and salt in the bearings.
•
Rinse the bearings with fresh water and
lubricate with Furlex grease.
• Too much strain on the halyard.
• Ease the halyard off.
6.5.2
”The sail will not furl, is hard to furl
or can only be partly furled”
• The jib halyard is wrapped around the
luff extrusion.
• Ease the halyard slightly and try to
reverse the system.
• Another halyard is wrapped around the
luff extrusion.
• Unfurl the system. Free the halyard.
• The halyard shackle/knot interferes
with the top extrusion.
• Make sure tht the 15-20º requirement
is fulfilled. Check that the shackle/knot
arrangement is not too ”bulky”.
• There is no line left on the drum.
• Unfurl the sail. Take it down and wind
more line on the drum. Alternatively,
loosen the sheet, gather the sail around
the system and wind more line onto the
drum.
• The forestay is too slack.
• Increase forestay tension.
• Excessive wind pressure on the sail.
• Let the leeward sheet off more.
• Windward sheet is not released.
•
Release the sheet.
• The sheet has become tangled.
• Sort out the sheet.
• The free turn is not functioning.
•
Rinse the bearings with fresh water and
lubricate with Furlex grease.
• Large turning angles in the furling line
route which increase friction.
•
Reroute the furling line, avoiding large
turning angles.
• Dirt and salt in the bearings.
•
Rinse the bearings with fresh water and
lubricate with Furlex grease.
• The furling line has become tangled on
the drum.
• Unfurl the sail and take it down.
Rewind the furling line. Unfurl the sail
with slight drag on the furling line in
the future and avoid having too much
line on the drum.
• The line guide fitting chafes against the
drum.
• Loosen the fastening screw below the
drum and adjust the fitting.
• The halyard swivel is upside down.
• Fit the halyard swivel correctly.
• Too much strain on the halyard.
• Ease the halyard off a little.
6.5.3
”The system ‘wobbles’ when furling
and unfurling”
• The forestay is too loose.
• Tension the backstay and/or the cap
shrouds. This will tension the forestay.
6.5.4
”The sail unfurls after reefing or
furling”
• The sail is not furled tightly enough.
• Furl with some drag on the line.
• The furling line is not belayed.
• Furl and belay the furling line.