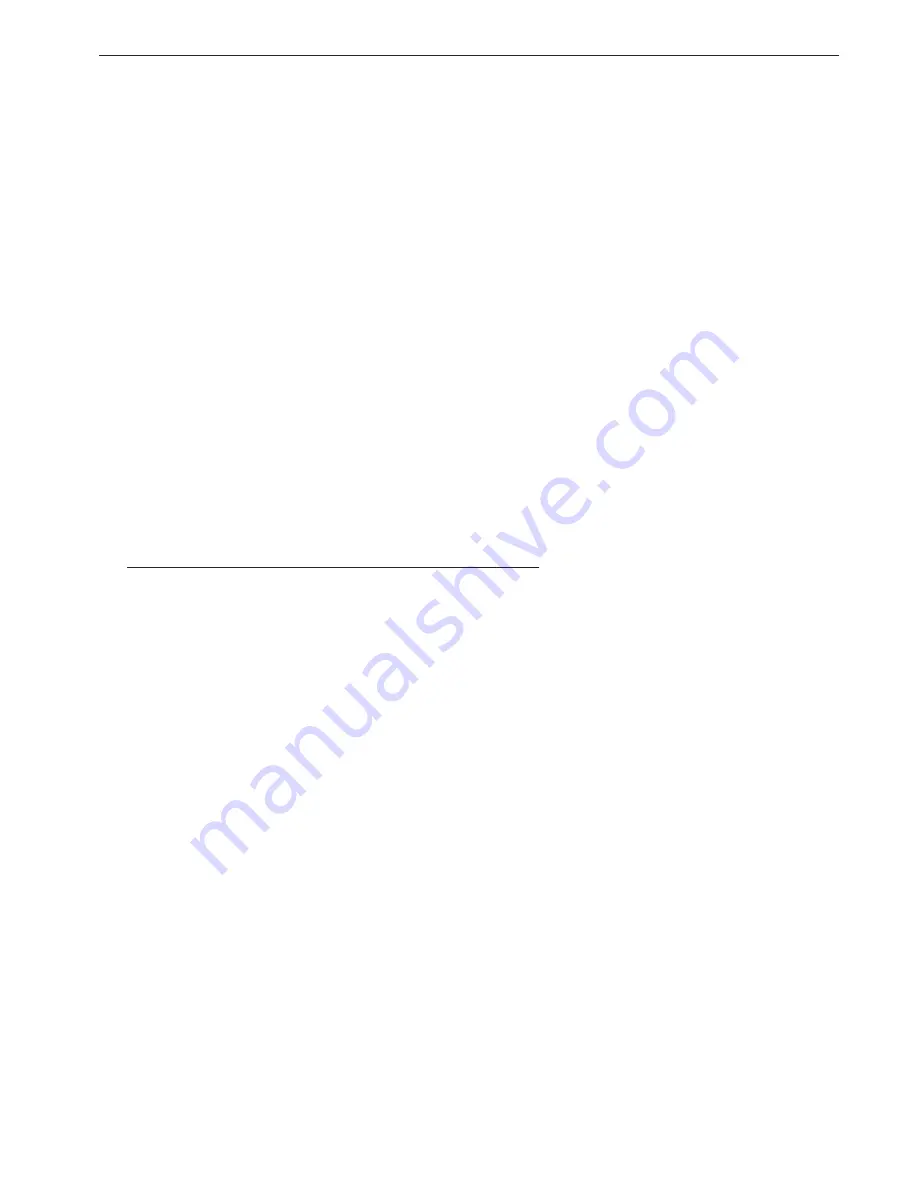
3.3 Loadcell connection
A standardized connection technique, using 6-conductor cables, is employed for load cells. Two of these
conductors are for feeding the cells, two for load signal and two for sensing the line resistance. Due to this
connection method, cable lengths up to 500 m are possible (provided the distance to parallel high power cables is
at least 2 m when cable lengths exceed a "few" metres.)
Compensation conductors begin at the load cell's fixed cable which has 4 conductors, 2 of which are branched
with jumpers. The fixed load cell cable has no compensation conductors of its own but is factory calibrated to
match the load cell and must not be shortened unless absolutely necessary.
Connection of load cell cables to the control console depend on the number of load cells plus the distance
between load cells and the control console. SEG's junction and connection box are used for splicing and
interconnection.
Belt scales generally incorporate a pulse generator for detecting belt speed. The signal from the generator is
transmitted by an extra pair of conductors in the same cable used for the load cell signal.
When connecting load cells of other brands than SEG, check that they are compatible with a 12Vdc
supply voltage, and that the max current load does not exceed 140mA (~85 Ohms).
NOTE: Screens for load cell cables are connected to ground only when connected directly to the
controller. In the case where connection boxes are used, special terminals in the connection boxes are
used for the cable shields.
Connection to the controller is made at the terminal board SPS202, Refer to fig. 3.1
Terminal connections:
Term. Function
SEG Load cell cable
1:
Feed
+
Yellow
01:
Sense
+
-
2:
Load signal
+
Red
3:
Load signal
-
Green
04:
Sense
-
-
4:
Feed
-
Blue
¤
Signal ground. Connect to separate signal ground only, if available.
For Intrinsically safe (Eex) installations: Connect protective ground from zenerbarriers.
Refer to drawing overleaf.
18-08-16
S44-H15E
3-3
S-E-G
SYSTEM A2-H15 INSTRUCTION