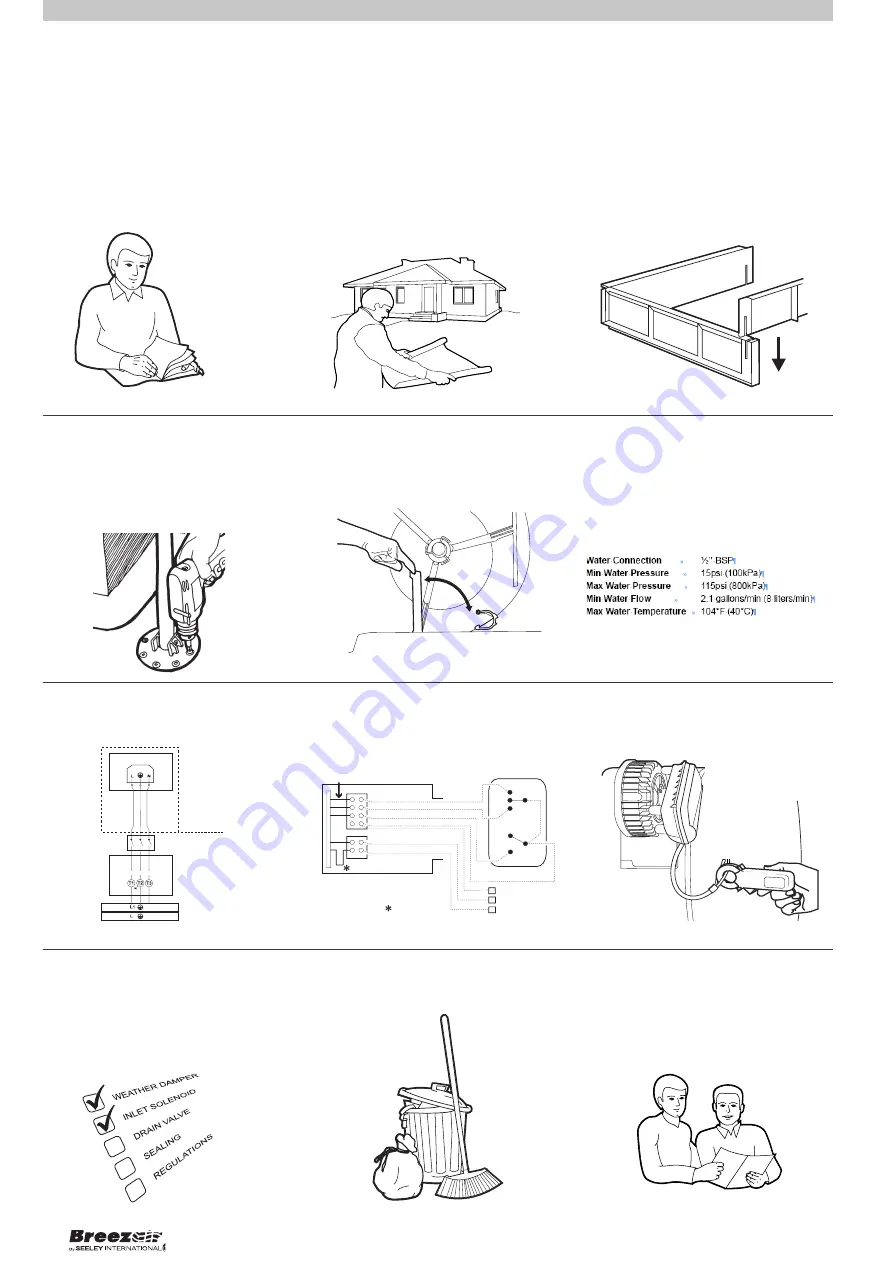
2
|
STEP 13
ELECTRICAL REQUIREMENTS
page 9
STEP 15
CHECK MOTOR AMPS
STEP 9
WATER REQUIREMENTS
Installation of the cooler water supply
must conform to local plumbing rules,
regulations and standards.
page 11
page 7
STEP 7
SECURING LEG SUPPORTS
The telescopic leg supports (with feet
attached) slide up and down inside the
four corner posts.
STEP 14
WIRING DIAGRAMS
page 9
ILL959-B
DIAGRAMA DE CABLEADO EN EL SITIO
MóDULO ELECTRóNICO
NEGRO/MARRó
N
VERDE/AMARILL
O
BLANCO/AZUL
GABINETE DEL SISTEMA
DE ENFRIAMIENTO
INTERRUPTOR DE
DESCONEXIóN OMNIPOLAR
SUMINISTRADO POR EL
INSTALADOR
CAJA DE EMPALMES
verde/amarillo
FUENTE DE ALIMENTACIóN
PRINCIPAL
L2(EE.UU.)
N(EUROPA)
HIGH
FIELD WIRING
HIGH
VENT
OFF
LOW
LOW
COOL
GROUND/EARTH
TERMINAL BOX
WALL
CONTROL
HOT WIRE/LINE VOLTAGE
USA EA WIRING DIAGRAM
- 2 SPEED
SINGLE PHASE 115V (LINE VOLTAGE
WIRED TO COOLER)
COMMON/NEUTRAL
MOTOR CURRENT (AMP)
TEST POINT
FAN
CONTROL
PUMP
CONTROL
PUMP
HOT WIRE TO WALL CONTROL
GROUND/EARTH
COMMON/NEUTRAL
FACTORY WIRING (DO NOT DISTURB)
ILL1026-A
ALTO
CABLEADO DEL CAMPO
ALTO
VENTILACIÓN
FRESCO
APAG
BAJA
BAJA
MASA/TIERRA
CAJA DE EMPALME
CONTROL
DE LA
PARED
L NEA CON CORRIENTE
Í
USA EA
-
DIAGRAMAS DE CONEXIONES ELECTRICAS DOS VELOCIDADES
115V
MONOFASICO
(LÍNEA DE SUMINISTRO CONECTADA PRIMERO AL ENFRIADOR)
COM
N/NEUTRAL
Ó
PUNTO DE PRUEBA ACTUAL DEL MOTOR
PUNTO DE PRUEBA ACTUAL DEL MOTOR
AVIENTE
EL CONTROL
CONTROL
DE LA
BOMBA
BOMBA
HILO CALIENTE AL CONTROL DE LA PARED
MASA/TIERRA
COM
N/NEUTRAL
Ó
NO INTERFIERA CON LAS CONEXIONES ELÉCTRICAS DE FÁBRICA.
ILL1026-A
OPCIÓN 1 DEL CABLEADO
page 6
STEP 1
SAFETY
Read & understand the safety section.
STEP 8
WEATHERSEAL
Check operation of the Weatherseal
STEP 2
COOLER LOCATION
Check cooler location. Consider
regulations. Discuss with customer.
STEP 3
INSTALL ROOFJACK
Install 24G metal roof jack and
seal before mounting.
page 1
page 6
page 4
ILL3363-A
page 5
STEP 22
FINAL CHECK
Test & complete the commissioning
checklist at the end of this document.
STEP 23
CLEAN UP
Clean up the site!
STEP 24
CUSTOMER HANDOVER
Show customer how to operate
the cooler. Explain maintenance
requirements.
page 16
page 16
page 16
QUICK GUIDE