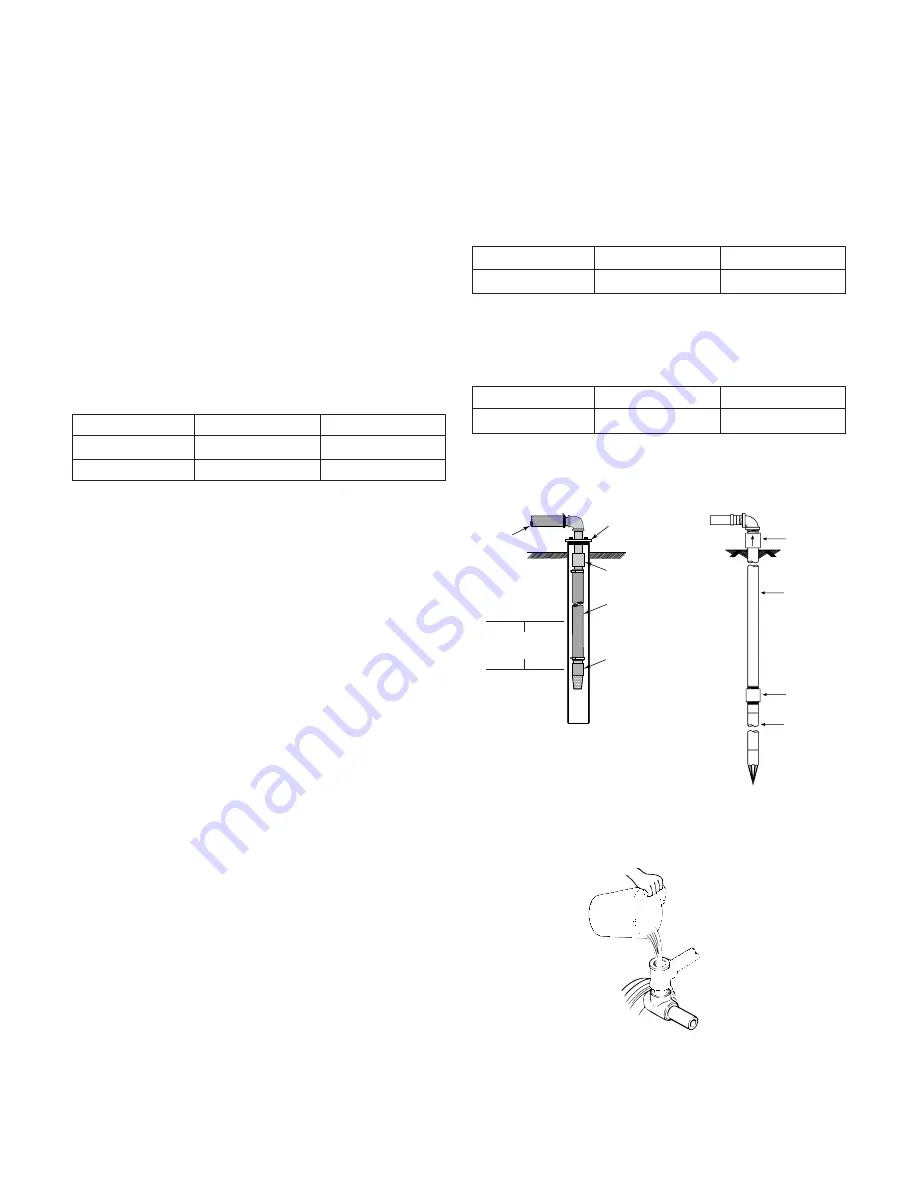
MAJOR COMPONENTS / PIPING
MAJOR COMPONENTS
AND WHAT THEY DO
NOTICE:
Use Teflon tape supplied with the pump for making all
threaded connections to the pump.
Impeller and Jet
Impeller turns with motor shaft, causing water to fly out from its
rim by centrifugal force. Impeller rotation creates a vacuum which
pulls in more water. Part of the water is diverted back to the jet
where it passes through the nozzle and venturi. This creates more
vacuum to draw in more water.
In shallow wells (less than 20 feet deep), the vacuum created at the
pump is enough to pull water to the pump. Therefore, the jet as-
sembly is built into the pump.
Air Volume Control
The air volume control (AVC) maintains the cushion of air in
Standard tanks.
Pressure Switch
The pressure switch provides automatic control.
MODEL NO.
PUMP STARTS AT
PUMP STOPS AT
390.2514
40 PSI
60 PSI
390.2518
40 PSI
60 PSI
Tank
The tank serves two functions. It provides a reservoir of water,
some of which can be drawn through the house fixture before the
pump must start. It maintains a cushion of air under pressure.
Two types of tanks are available. Captive Air
®
and Standard. No air
volume control is needed with Captive Air
®
Tanks.
PIPING IN THE WELL
A shallow well jet pump can be installed on a dug well, drilled well
or a driven point. SEARS shallow well jet pumps have a built-in
check valve. In a dug or cased well, a foot valve and strainer should
be installed for easy priming. It should be 5 to 10 feet below the
lowest level to which the water will drop while pump is operating
(pumping level) (Figure 1).
The strainer should not be too close to the bottom, or sediment
may clog it. Before installing foot valve, check to see that it works
freely.
When using a foot valve, a priming tee and plug must be included
(Figure 2).
Be sure the vertical distance (lift) from the priming level to pump
is not over 20 feet, if the pump is over well. This will be less if
pump is offset from the well. Both figures are for sea level. The
maximum lift of any pump decreases with the elevation above sea
level. This decrease is at the rate of 1 foot per 1000 feet of eleva-
tion. For example, the lift is 17 feet and your elevation is 3000 feet
above sea level. You would then be pumping 17 plus 3, or 20 feet.
This is still satisfactory for shallow well pumping.
EMERGENCY POWER
In some areas and with some installations, an emergency power
supply to guard against power failure is a good idea. If you install
an engine-generator set for emergency backup power for your
pump, supply the generator set manufacturer with the nameplate
data from the pump motor. He will then be able to provide a gen-
erator of the correct size to power your pump. Also, be sure to add
the load from any other accessories (such as lights) that may be on
the same circuit.
Horizontal Piping from Well to Pump
On well point installations where the horizontal piping is more
than 25 feet, a check valve should be installed (Figure 3).
When the pump is offset more than 25 feet from the well, hori-
zontal piping should be increased in size to reduce friction losses.
Never use offset piping that is smaller than the suction tapping of
the pump.
Horizontal Offset Piping Sizes - Shallow Well Jets
1-1/4"
1-1/2"
2"
Up to 25 ft.
25 to 50 ft.
50 to 200 ft.
Discharge Pipe Sizes
When the pump is some distance from the house or point of water
use, the discharge pipe size should be increased to reduce pressure
losses.
1"
1-1/4"
1-1/2"
Up to 25 ft.
25 to 100 ft.
100 to 600 ft.
4
Check valve
Steel drive pipe
Drive coupling
Well point
Driven point
Plastic Pipe
Plastic Pipe
Foot Valve
and Strainer
Coupling
Well Seal
Dug or Cased Well
611 1293
Figure 1
Figure 3
1-1/4”
Plastic Pipe
DUG OR CASED WELL
5’ To 10’
Pumping Level
1-1/4”
Plastic Pipe
Foot Valve
and Strainer
Coupling
Well Seal
Plastic
Pipe
NOTE: Check
valve used if hori-
zontal piping is 25
ft. or more.
DRIVEN POINT
Well Point
Drive
Coupling
Steel
Drive
Pipe
Check
Valve
183 0893
Figure 2