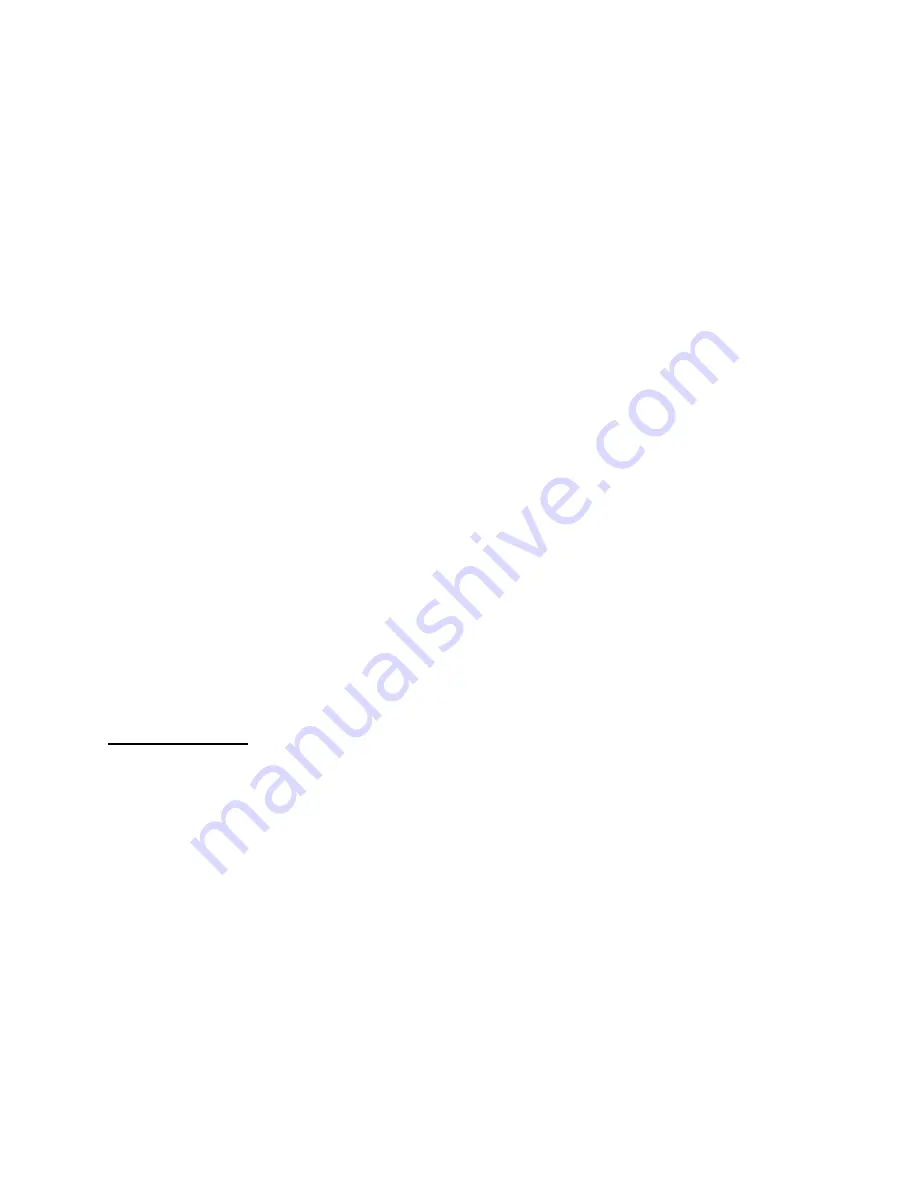
13
CRACK PRO® MASTIC MACHINE
PRE-OPERATION INSTRUCTIONS
CAUTIONS
Caution should be used when loading blocks to prevent possible
splashes of hot material. Set a material block (one at a time) on the
lid. Close the lid allowing the block to drop into the material tank.
Do not breathe joint sealing material fumes.
Do not exceed 10 mph when towing with the burner on.
Do not operate the machine in the rain.
Do not pressure wash the burner area in front of the machine.
Do not work on the machine while it is in operation.
Do not work on the machine when heat transfer oil has been
heated over 90°F.
Never expose the material tank to an open flame.
CLOTHING
Proper clothing should be worn at
all
times.
long sleeve shirt
face shield
high-temperature gloves
long pants
Summary of Contents for Crack Pro 250
Page 1: ......
Page 8: ...8 SAFETY PRECAUTIONS AND CAUTIONS FIRST AID ...
Page 20: ...20 ...
Page 21: ...21 ...
Page 22: ...22 ...
Page 23: ...23 ...
Page 24: ...24 ...
Page 25: ...25 ...
Page 26: ...26 ...
Page 27: ...27 ...
Page 37: ...37 WIRING DIAGRAMS TEMPERATURE CONTROL BOX ...
Page 38: ...38 WIRING DIAGRAMS TEMPERATURE CONTROL BOX ...
Page 39: ...39 MASTIC MACHINE CONNECTOR J1 ...
Page 41: ...41 WIRING DIAGRAMS ALL THE WIRING COMES OUT OF THE CONTROL BOX TO THE LIGHTS ...