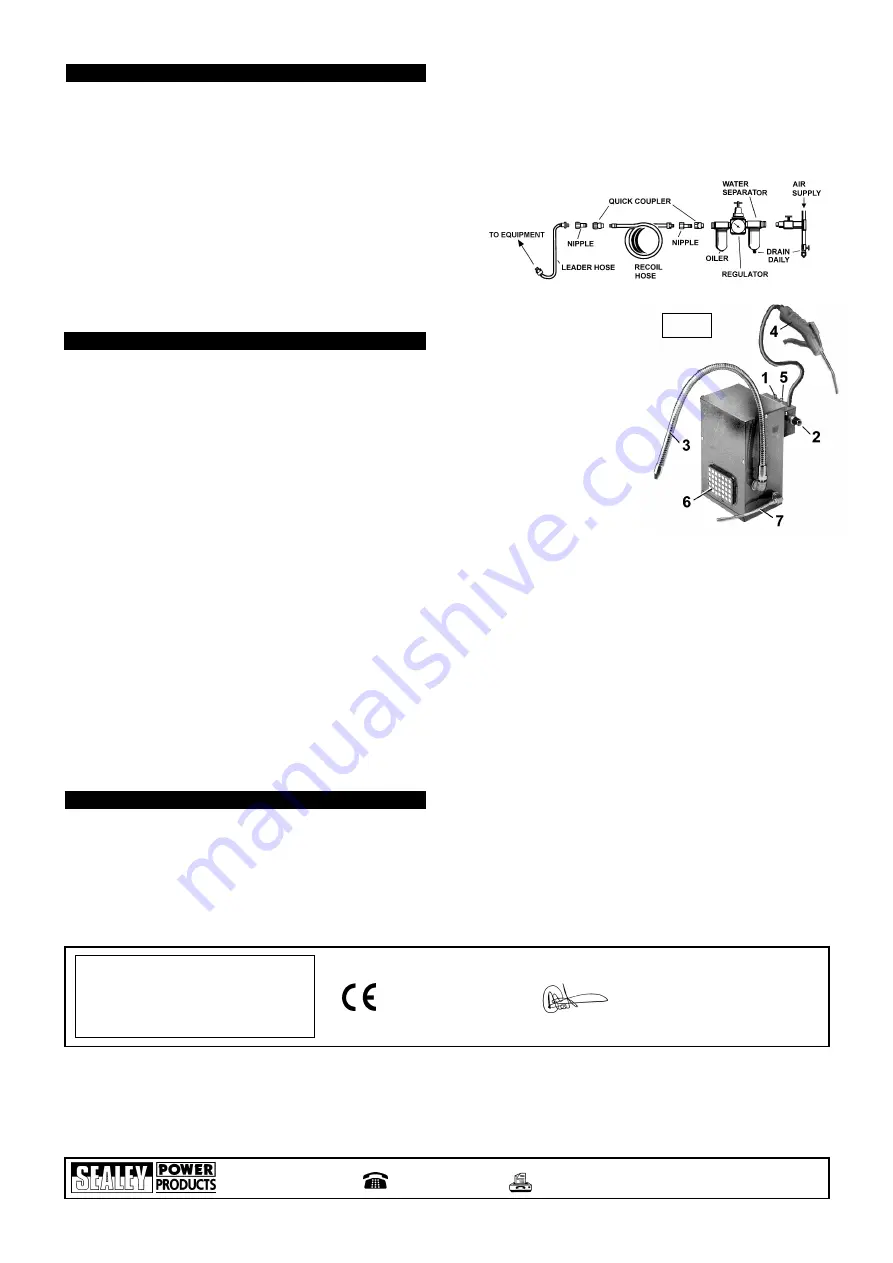
4.1. Ensure that the tank air valve is closed before connecting the air supply.
4.2. An air pressure of 65-125psi and an available air volume of 8-10cfm will be required to operate the unit.
p
WARNING! Ensure air supply is clean and does not exceed 125psi. Too high an air pressure and/or unclean air will shorten the
product life due to excessive wear and may be dangerous, causing possible damage and/or personal injury.
Air supply must be equipped with regulator, water trap and oiler.
4.3. Drain the air supply tank daily. Water in the air line will damage the unit.
4.4. Clean the air supply filter weekly. For recommended hook-up, see diagram.
4.5. Line pressure should be increased to compensate for unusually long air
hoses (over 8 metres). The minimum hose internal diameter should be
10mm and fittings must have the same internal dimension.
4.6. Keep hose away from heat, oil and sharp edges. Check hoses for
wear, and make certain that all connections are secure.
4.7. The air inlet connection is 1/4BSP
.
5. OPERATING INSTRUCTIONS
6. MAINTENANCE
5.10.
SOLVENT REPLACEMENT
p
WARNING! It is operators responsibility to ensure that there is no uncontrolled discharge of any fluids used with this unit and that
appropriate arrangements have been made for correct disposal of waste in accordance with government/local authority regulations.
p
WARNING! Disconnect the air supply from the unit before changing accessories, servicing or performing any maintenance.
p
p
WARNING! Wear approved safety gloves, goggles, mask and suitable clothing.
5.10.1. To empty used solvent, loosen sediment in the bottom of the tank by use of the turbo mode, then open base plug to drain.
Completely drain dirty solvent into appropriate receptacle. Clean inside of tank and strainer before refilling with clean solvent.
5.10.2. Store the used solvent in accordance with regulations.
5.10.3. Wipe up any spillage immediately.
4. AIR SUPPLY
HOOK-UP
p
p
WARNING! Read and apply Section 1 safety instructions before using the cleaning tank.
5.1.
Check the air regulator valve (fig. 1.1) is off, and air inlet (2) is disconnected from the air supply.
5.2.
Fill the tank to appropriate capacity (See specifications) with Sealey solvent, or a general purpose
degreaser (contact your local dealer for supply). DO NOT use any other type of solvent.
CAUTION! Ensure you follow any instructions provided with the solvent.
5.3.
Connect washer to the air supply, aim flexible nozzle (3) into tank and turn valve (1) on. Check that
solvent flows freely through the flexible nozzle.
5.4.
Place parts to be cleaned into the cleaning basket. Direct spray nozzle onto parts. Ensure any
splash back stays inside the tank, if not reposition the spray nozzle. Adjust the air flow valve (1)
to give the minimum output for the task.
5.5.
The supplied brush may be attached to the nozzle to assisted cleaning if required.
5.6.
For stubborn and ground in marks, leave the parts to soak in the bottom of the tank. Place the turbo
nozzle (7) in the solvent and turn the turbo mode valve (5) on. This will agitate the solvent and assist cleaning.
5.7.
When parts are clean, turn off the pump and leave the parts to drain in the basket or on the shelf.
5.8.
To assist drying the air blow gun (4) may be used.
5.9.
When complete, turn the washer off and disconnect from the air supply.
When cleaning parts ensure that nothing in the tank, including any parts basket, is in a position that would prevent the lid from
closing fully if and when the fusible link activates.
p
WARNING! Disconnect the air supply from the unit before changing accessories, servicing or performing any maintenance.
6.1.
Keep the cleaning tank clean. Remove and clean the filter (fig 1.6) regularly for best and safest performance.
6.2.
Regularly check and top up the oil in the air supply oiler.
6.3.
Keep the outside of the unit clean.
6.4.
DO NOT modify or jam the parts washer lid open, as this will make the fusible fire link inoperative which is dangerous practice and will
invalidate the warranty and your insurance.
fig. 1
Sole UK Distributor,
Sealey Group,
Bury St. Edmunds, Suffolk.
01284 757500
E-mail:
01284 703534
NOTE:
It is our policy to continually improve products and as such we reserve the right to alter data, specifications and component parts without prior notice.
IMPORTANT:
No liability is accepted for incorrect use of this product.
WARRANTY:
Guarantee is 12 months from purchase date, proof of which will be required for any claim.
INFORMATION:
For a copy of our latest catalogue and promotions call us on 01284 757525 and leave your full name and address, including postcode.
Declaration of Conformity
We, the sole importer into the UK, declare that the product listed here
is in conformity with the following standards and directives.
The construction file for this product is held by the manufacturer and may be inspected, by a national authority, upon
request to Jack Sealey Ltd.
For Jack Sealey Ltd. Sole importer into the UK of Sealey Power Products.
23rd November 2000
WORKSHOP AIR POWERED CLEANING TANK
MODEL SM22/C
93/68/EEC CE Marking Directive
98/37/EC Machinery Directive
Signed by Mark Sweetman
SM22/C - 2 - 230805