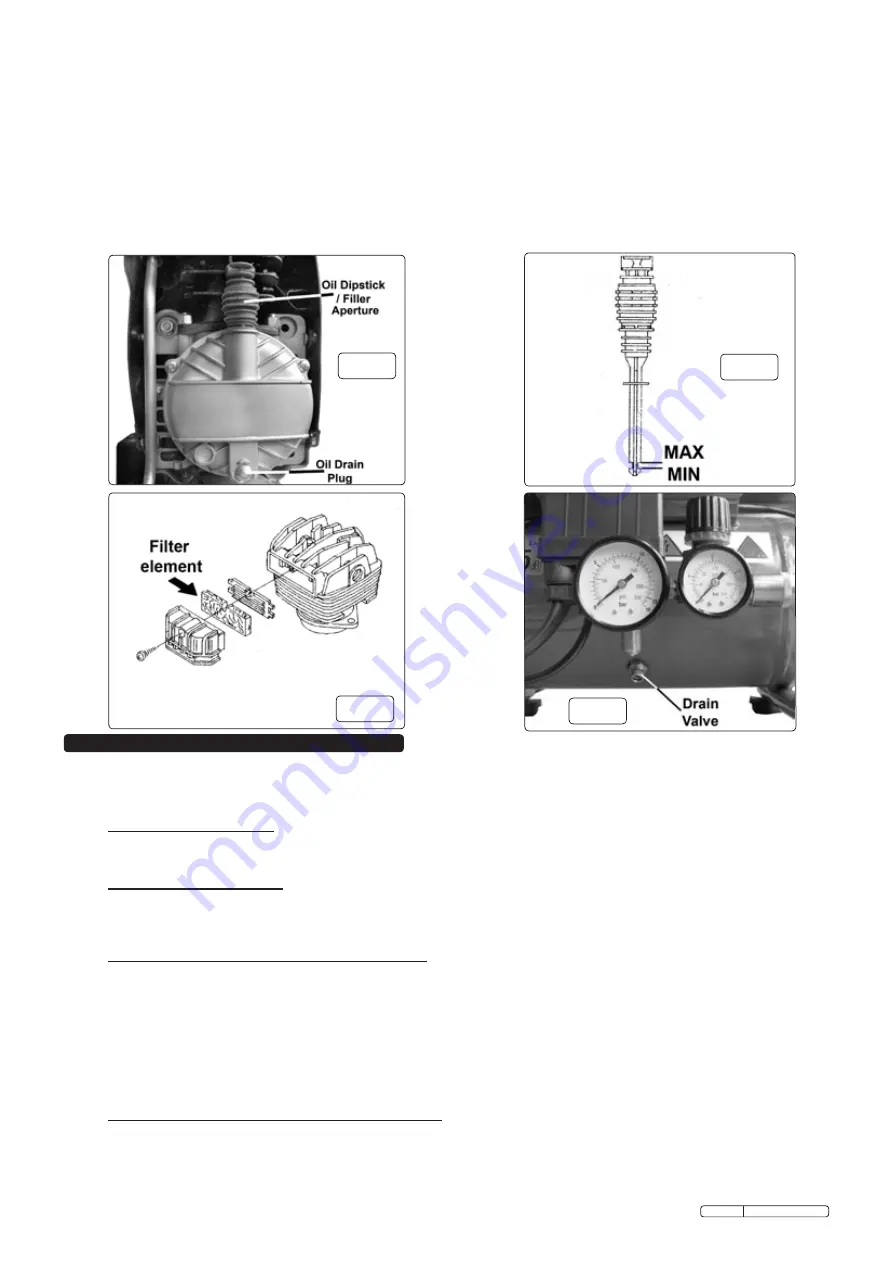
5. MAiNtENANCE
WARNiNG!
Before performing any maintenance, switch off the compressor, disconnect from the electricity supply, release all air
from the tank and turn the regulator off (fully clockwise).
In order to keep the compressor in good working condition, periodical maintenance is essential.
5.1.
After the first 100 working hours, replace the lubricating oil - see section 5.4b below.
5.2.
tO BE CARRiEd OUt dAiLY:
a) drain condensation from the tank. see 4.14. above.
b) check for oil leaks.
c) check oil level and top up if necessary.
5.3.
tO BE CARRiEd OUt WEEKLY:
a) remove the filter element (fig.4) and check its condition. unclip the end plastic safety cover (3 clips) and lift it away. remove the
cross-head screw in the filter cover and prise out the foam filter element. clean it by blowing through with an air line at low pressure,
or wash it in soapy water, rinse and dry. refit filter and the cover. do not operate the compressor without the filter as foreign matter or
dust could seriously damage the pump.
5.4.
tO BE CARRiEd OUt AFtER EvERY 100 hOURS OF USE:
a) check that the automatic cut-out at maximum pressure, and the automatic cut-in at 2bar below that, are operating correctly.
b) replace the lubricating oil. for oil specifications see below.
remove the oil drain plug (fig.2), draining the oil into a suitable container. drain when the compressor is hot so that oil drains
rapidly and completely. Incline compressor if needed to ensure complete drainage. replace the oil drain plug and pour oil through
the filler/dipstick aperture. check oil level with dipstick (fig.3) and
dO NOt
overfill.
Recommended oil:
the pump is filled with synthetic oil at the factory, if topping up or changing oil use a synthetic oil of sae
5W50 viscosity. alternatively a mineral oil can be substituted when carrying out an oil change, after ensuring that the synthetic oil has
been thoroughly drained first. use a mineral oil of sae 15W40 viscosity.
WARNiNG! do not mix different oils and do not use non-detergent/low quality oils, as the compressor may be damaged.
dispose of all waste oil responsibly, in accordance with local authority requirements.
5.5.
tO BE CARRiEd OUt AFtER EvERY 500 hOURS OF USE:
a) replace air filter.
b) check all tube fittings and electrical connections.
c) check all screws, nuts and bolts are tightly in place.
d) Inspect pressure tank inside and out for damage or corrosion.
iMPORtANt! Failure to carry out maintenance tasks may invalidate the warranty on your compressor.
Original Language Version
sa0615 Issue: 2 - 20/02/12
4.11.
When finished using the compressor, unplug the unit from the mains power supply.
4.12.
set the outlet pressure regulator to zero by turning the knob anti-clockwise.
4.13.
disconnect the air line/air tool.
4.14.
the tank must be drained, this will release the air left in the tank and drain away any condensation that may have formed within the
tank. choose a suitable location for this operation and/or make provision to collect the condensation.
Wear ear and eye protection
.
open the tank drain valve (fig.5) slowly allowing air and moisture to bleed from the tank. after bleeding, close the drain valve to
prevent debris building up in the valve.
WARNiNG! Water that is allowed to remain in the tank during storage will corrode and weaken the air tank which could cause
the tank to rupture. to avoid serious injury, drain the tank after each use or daily.
4.15.
SAFEtY FEAtURES.
thermal cut out:
If the unit overheats, the thermal cut out will operate and shut the unit down. the thermal cut out will automatically
reset when the unit has cooled down - which may take 10 to 15 minutes.
fig.4
fig.2
fig.5
fig.3