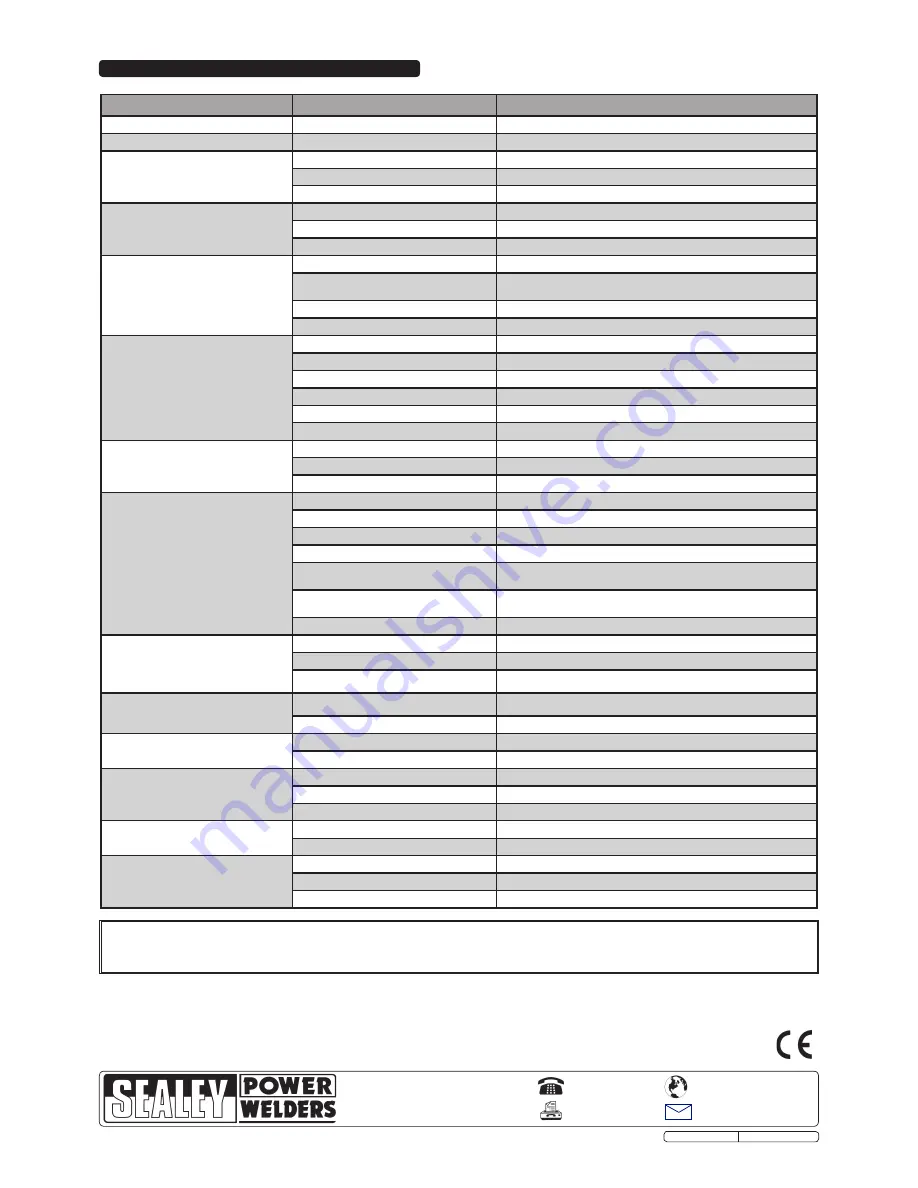
7. TROUBLESHOOTING
PROBLEM
POSSIBLE CAUSE
REMEDY
1. Power source stops
Overheating protection activated due to overload
Protection automatically resets when transformer has cooled (about 15 min)
2. No weld current
Rectifier blown
Replace rectifier.
3. No weld current
Bad connection between clamp & workpiece
Clean or grind contact surface and weld area
Break in earth lead
Repair or replace earth lead.
Break in torch lead
Repair or replace torch
4. Feed motor not working, lamp is on
Gear damaged or worn
Replace gears. (Contact service agent)
Motor defective
Replace motor (Contact service agent)
PCB fault
Replace PCB
5. Wire does not feed, feed roller rotates
Pressure roller improperly adjusted
Adjust tension.
Dirt, copper, dust, etc, has collected in torch liner
Clean the liner from the machine forward. Use compressed air. If too much dirt,
replace the liner.
Gas cup (Nozzle) or tip defective
Replace gas cup (nozzle) and/or tip. (Section 4.1.8 to 4.1.11)
Deformed wire
Check roller tension and adjust it if necessary (Section 4.2)
6. Wire feeds unevenly
Dirt, etc, in liner
Clean the liner from the machine forward. Use compressed air
Gas cup (Nozzle) or Tip defective
Replace gas cup (nozzle) and/or tip. (Section 4.1.8 to 4.1.11).
Gas cup (Nozzle) spattered
Clean or replace gas cup (nozzle) (Section 4.1.8 to 4.1.11)
Feed roller groove clogged
Clean feed roller.
Feed roller groove deformed
Replace feed roller.
Pressure roller tension improper
Adjust tension. (Section 4.2)
7. Unstable arc
Incorrect settings
Check settings.
Impurities in weld area
Clean and/or grind workpiece.
Worn or defective gas cup (nozzle)
Replace gas cup (nozzle). (Section 4.1.8 to 4.1.11)
8. Porous weld
No gas
Open gas cylinder, regulate gas flow
Gas cup clogged
Clean or replace cup. (nozzle) (Section 4.1.8 to 4.1.11)
Draft blowing away shielding gas
Screen off welding site or increase gas flow
Rusty or dirty joints
Clean and/or grind workpiece. (Section 4.1.1)
Torch too far from or at wrong angle to work
The distance from gas cup to workpiece should be 8 to 10mm
Gas leak
Check hoses, connections and torch assembly. Press the gas cup into correct
position
Faulty Electrovalve
Clean out or replace
9. Electrode sticking in gas cup (nozzle)
Worn or defective gas cup (nozzle)
Replace gas cup (nozzle). (Section 4.1.8 to 4.1.11)
Electrode deformed
Check roller tension. (Section 3.10)
Wire speed too slow
See recommendations for wire speed
10. Irregular weld head
Torch incorrectly held
Use correct torch angle
Wire weaving in weld pool
Check roller tension and adjust as needed. (Section 4.2)
11. Weld bead too narrow and raised
Weld current too low
Increase power and wire speed.
Weld speed too high
Move torch slower and weave a little more
12. Weld bead too wide
Weld current too high
Decrease power and wire speed.
Weld speed too low
Move torch faster and weave less
Arc too long
Bring torch closer to workpiece
13. Poor penetration
Weld current too low
Increase power and wire speed.
Arc too long
Bring torch closer to workpiece
14. Excessive penetration
Weld current too high
Decrease power and wire speed.
Weld speed too slow
Move torch faster
incorrect distance of torch to workpiece
Torch distance should be 8-10mm
Parts support is available for this product. To obtain a parts listing and/or diagram,
please log on to www.sealey.co.uk, email [email protected] or phone 01284 757500.
NOTE:
it is our policy to continually improve products and as such we reserve the right to alter data, specifications and component parts without prior notice.
IMPORTANT:
No liability is accepted for incorrect use of this product.
WARRANTY:
Guarantee is 12 months from purchase date, proof of which will be required for any claim.
INFORMATION:
For a copy of our latest catalogue and promotions call us on 01284 757525 and leave your full name and address, including postcode.
01284 757500
01284 703534
Sole UK Distributor, Sealey Group,
Kempson Way, Suffolk Business Park
,
Bury St. Edmunds, Suffolk,
IP32 7AR
www.sealey.co.uk
Web
Original Language Version
MIGHTYMIG150 Issue: 2 - 26/02/10