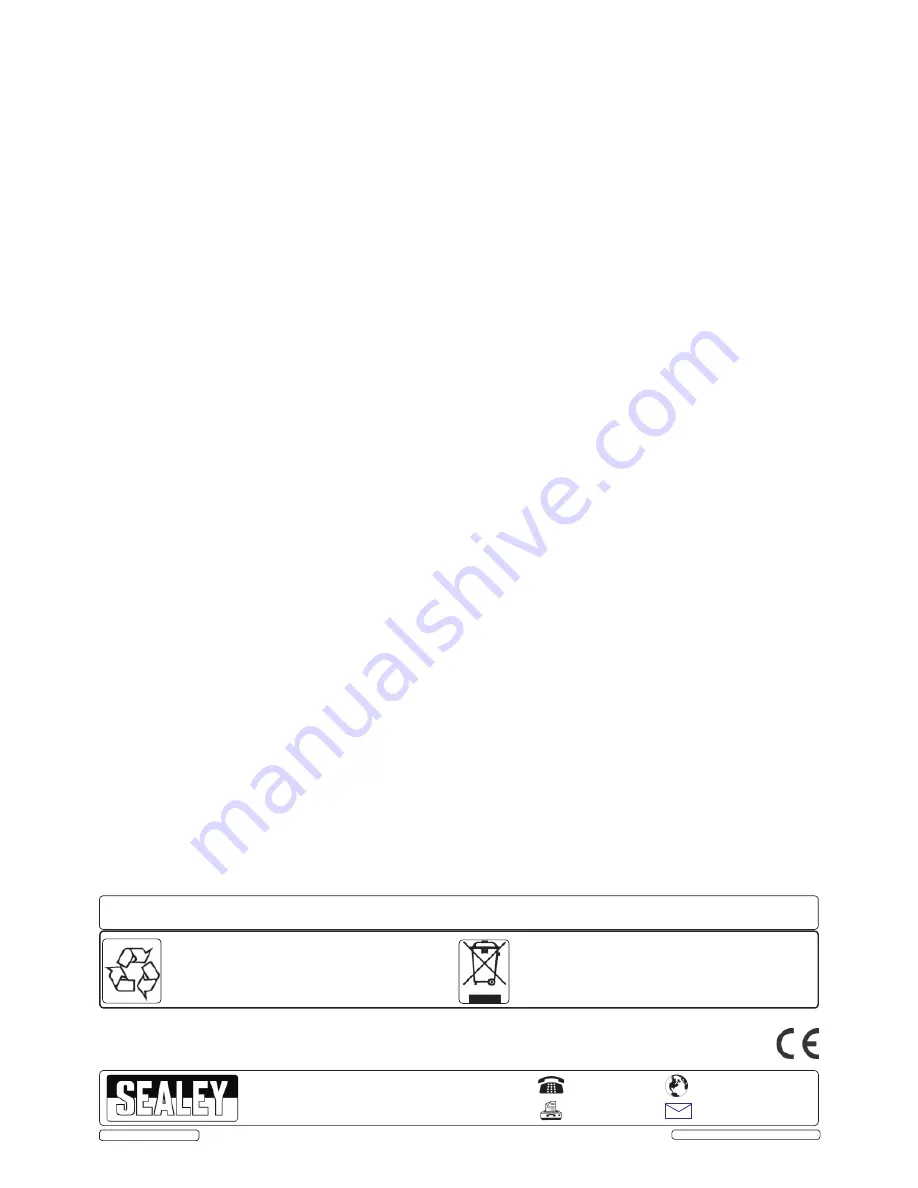
d) Safety critical equipment, e.g. security monitoring of industrial equipment.
e) The health of people in the vicinity, e.g. persons fitted with a pacemaker or hearing aid.
f) Equipment used for calibration or measurement.
g) The immunity of other equipment in the environment. The user shall ensure that other equipment being used in the environment is
compatible. This may require additional protective measures.
h) The time of day that welding and other activities are to be carried out.
11.5.
Mains supply.
The equipment should be connected to the mains supply according to these instructions. If interference occurs, it may
be necessary to take additional precautions such as filtering of the mains supply. Consideration should also be given to shielding the
supply cable of permanently installed equipment in metallic conduit or equivalent. This shielding should be connected to the power
source so that good electrical contact is maintained between the conduit and the welding power source enclosure.
11.6.
Maintenance of the equipment.
The equipment should be routinely maintained according to these instructions. All access and
service covers should be closed and properly fastened when the welding equipment is in operation. The welding equipment should
not be modified in any way except for those changes and adjustments covered in these instructions. In particular, the spark gaps of
any arc striking and stabilising devices should be adjusted and maintained according to the instructions.
11.7.
Cables.
The welding/cutting cables should be kept as short as possible and should be positioned close together, running at or close
to the floor level.
11.8.
Equipotential bonding.
Bonding of all metallic components in the welding/cutting installation and adjacent to it should be considered.
However, metallic components bonded to the workpiece will increase the risk that the operator could receive a shock by touching
these metallic components and the electrode at the same time. The operator should be insulated from all such bonded metallic
components.
11.9.
Earthing of the workpiece.
Where the workpiece is not bonded to earth for electrical safety, nor connected to earth because of its
size and position, e.g. ship’s hull or building steelwork, a connection bonding the workpiece to earth may reduce emissions in some,
but not all instances. Care should be taken to prevent the earthing of the workpiece increasing the risk of injury to others or damage
to other electrical equipment. Where necessary, the connection of the workpiece to earth should be made by a direct connection to
the workpiece, but in some countries where direct connection is not permitted, the bonding should be achieved by a suitable
capacitance, selected according to national regulations.
11.10
Selective screening and shielding of other cables and equipment in the surrounding area may alleviate problems of interference.
Screening of the entire welding/cutting installation may be considered for special applications.
Original Language Version
© Jack Sealey Limited
NOTE: It is our policy to continually improve products and as such we reserve the right to alter data, specifications and component parts without prior notice.
IMPORTANT:
No liability is accepted for incorrect use of this product.
WARRANTY:
Guarantee is 12 months from purchase date, proof of which will be required for any claim.
01284 757500
01284 703534
Sole UK Distributor, Sealey Group,
Kempson Way, Suffolk Business Park
,
Bury St. Edmunds, Suffolk,
IP32 7AR
www.sealey.co.uk
Web
Environmental Protection.
Recycle unwanted materials instead of disposing of them as
waste. All tools, accessories and packaging should be sorted,
taken to a recycle centre and disposed of in a manner which
is compatible with the environment.
WEEE Regulations.
Dispose of this product at the end of its working life in compliance
with the EU Directive on Waste Electrical and Electronic Equipment.
When the product is no longer required, it must be disposed of in an
environmentally protective way. Contact your local solid waste
authority for recycling information.
Parts support is available for this product. To obtain a parts listing and/or diagram, please log on to:
www.sealey.co.uk, email: [email protected] or phone:01284 757500.
INVMIG160 | Issue: 2S - 08/01/15