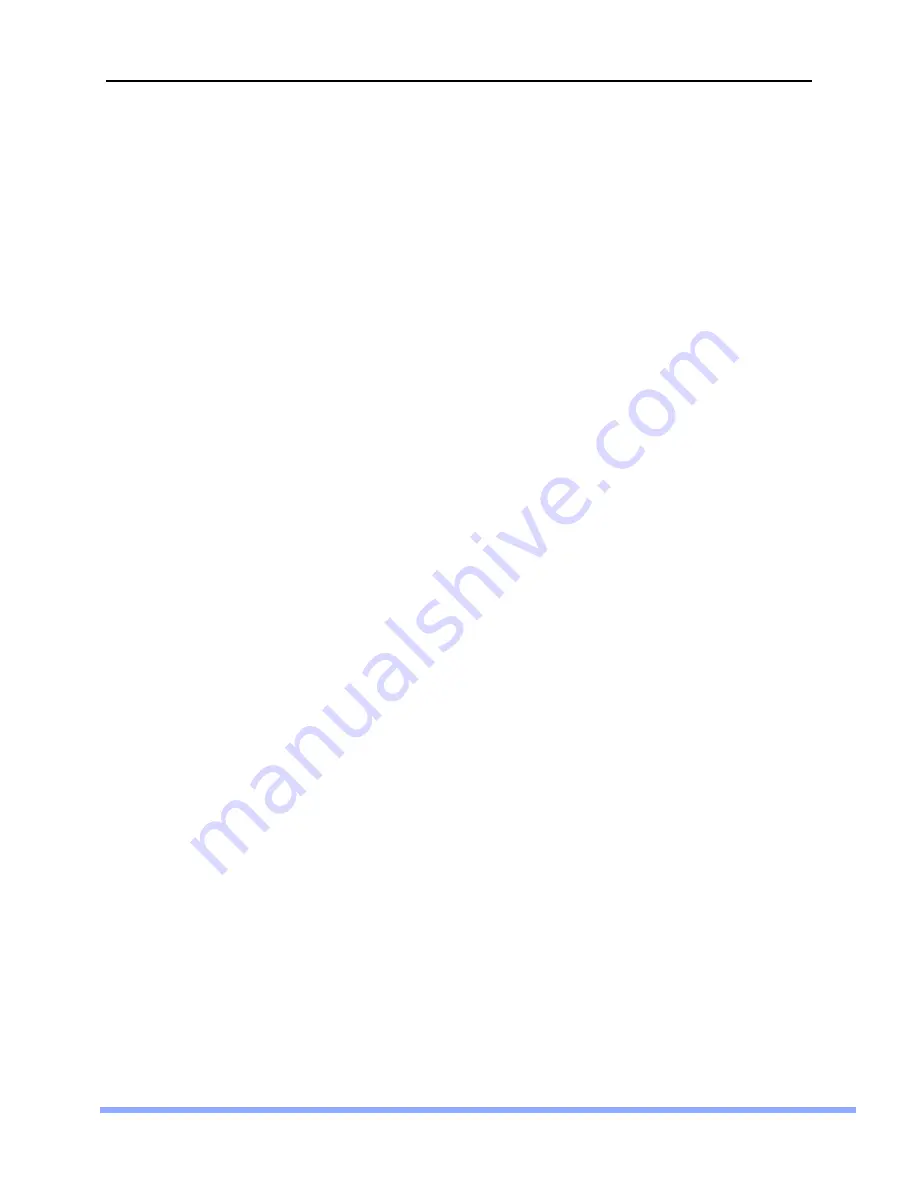
Section 2. Operating Procedures
15
4. Run the Laminator
1. Adjust the Speed Control to “1” on the dial.
2. Raise the Tension Idler and adjust brakes lightly into the Tension and Web Idlers
by turning clockwise.
3. Open the distribution valves on the applicator tube and ensure that the tips of the
flex hoses are not clogged with dried coating. Position hoses to deposit coating
on the backside of the lower draw down bar. (Some coating may begin to drain
out.)
4. Ensure that the Dryer Panel UP/DOWN switch is in the DOWN position.
5. Switch the machine into Run mode. (This will cause the Dryer Panel and the
Draw Down Assembly to lower into operating position and the Drive to begin to
move.)
Note:
At any time in machine operation the machine is sensing for movement in
the Take-up system to ensure that the media is always moving. If no
motion is sensed, a 30 second timer is initiated that will shut the machine
down if motion does not resume within the 30 second window.
6. Switch Sealant Pump ON.
7. Adjust Brake tension so that the material is pulling through smoothly with no
wrinkles.
8. Adjust speed to desired setting.
Note:
For most Superwide media a speed of 1 – 1.5M per minute (3-5 feet per
minute) will give you the best results and ensure that the coating is cured.
9. When the media being coated comes to an end, the last piece will lose tension;
you will need to manually provide back-tension as the media runs out.
10. Prior to the last piece of media going past the Draw Down Assembly the Sealant
Pump switch should be turned OFF and the Distribution Valves CLOSED.
Note:
There is usually sufficient coating on the media to shut the Sealant Pump
OFF 1M (3 feet) prior to the end of the material.
11. Once the material is through the Dryer Panel, the machine should be switched
back into Stop mode.
12. The finished material is easily unloaded by switching the Take-up into
Disengage. This disengages the Take-up Roller motor and the material can be
easily pulled off. The disengage state of the Take-up is functional in all modes,
including Stop mode.
Summary of Contents for AquaSEAL SW-4000
Page 22: ...Section 4 After Sales Support 21...