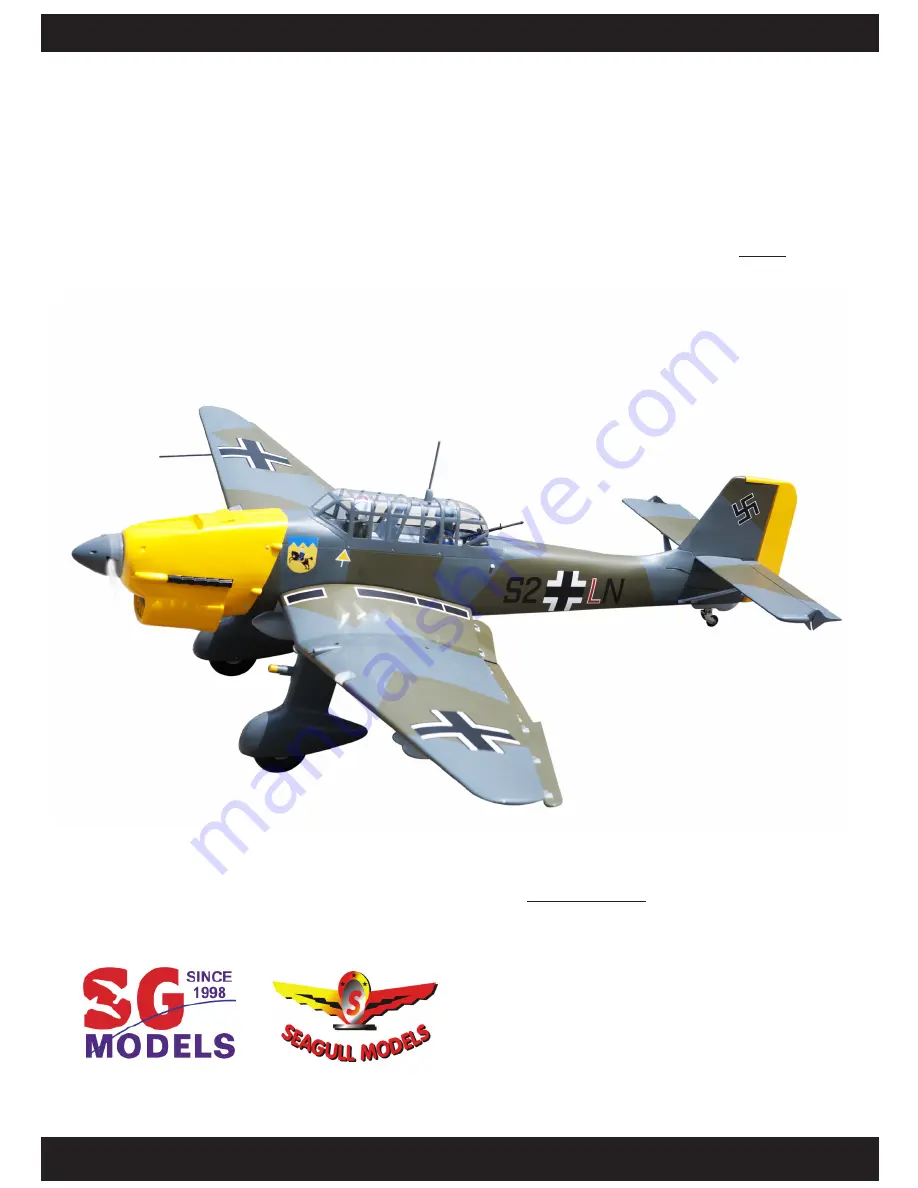
1
A S S E M B L Y M A N U A L
Code:
SEA284
“ Graphics and specifications may change without notice “ .
JU-87 STUKA GIANT SCALE
Specifications:
Wingspan---------------90 in (228.6 cm).
Wing area---------------1328.7 sq.in (85.7 sq.dm).
Weight-------------------17.6 lbs (8.0 kg).
Length-------------------68.3 in (173.4 cm).
Gasoline Engine--------38-50cc
Radio--------------------7 channels with 7 servos.
Summary of Contents for JU-87 STUKA
Page 4: ...JU 87 Instruction Manual 4 HINGING THE FLAP ...
Page 11: ...11 2mm 2mm ...
Page 12: ...JU 87 Instruction Manual 12 2mm 3x10mm ...
Page 13: ...13 2mm 3x10mm ...
Page 14: ...JU 87 Instruction Manual 14 INSTALLING THE BOMB ON THE WINGS Epoxy Epoxy ...
Page 15: ...15 Epoxy ...
Page 19: ...19 5x100 mm 8mm Blind nut 6 5 mm 6 5 mm ...
Page 32: ...JU 87 Instruction Manual 32 TAIL STRUTS INSTALLATION Epoxy ...
Page 33: ...33 SIDE FORCE GENERATOR OF STABILIZER ASSEMBLY Epoxy Epoxy ...
Page 37: ...37 Receiver Battery ATTACHMENT WING FUSELAGE Wing bolt 6x6mm ...