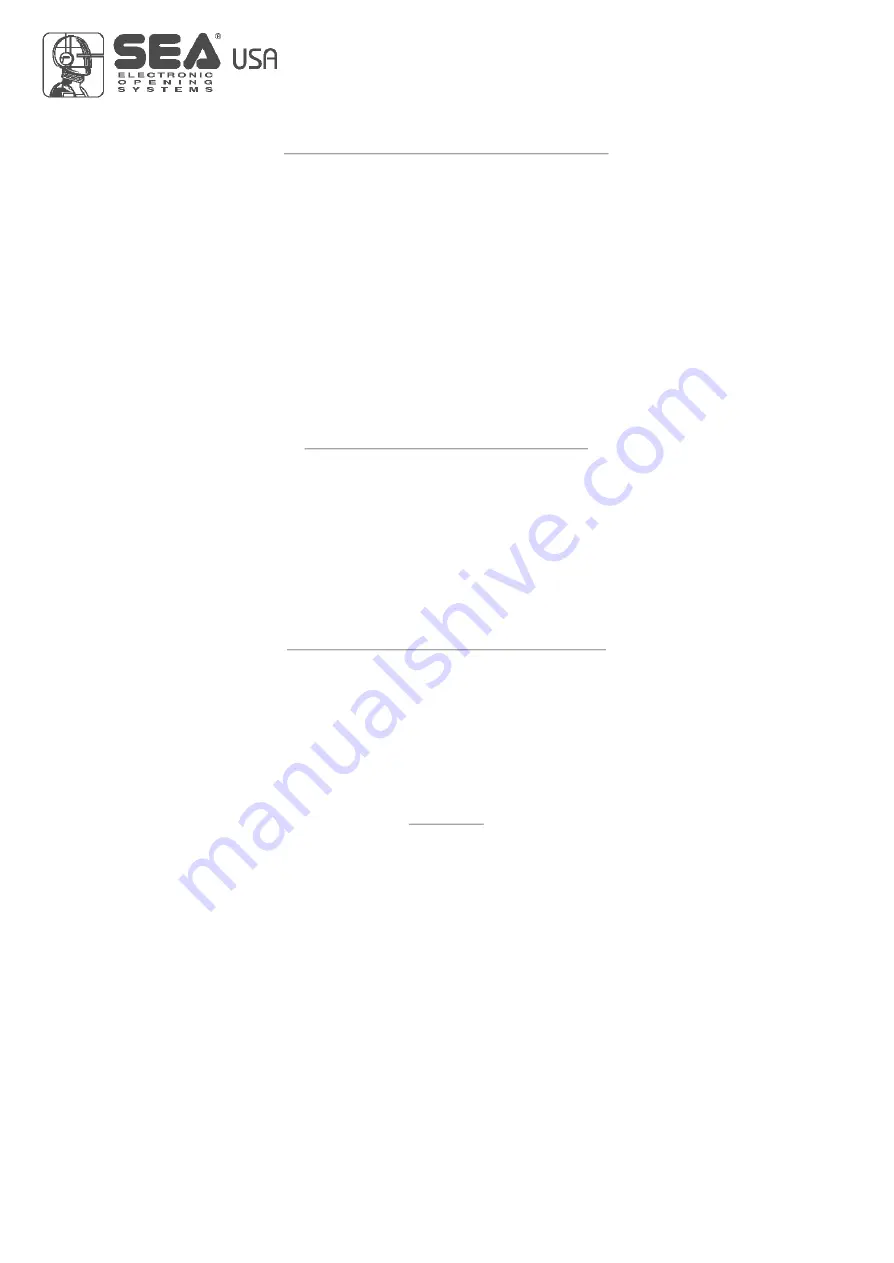
GENERAL SAFETY REGULATIONS FOR THE INSTALLER
• The installer has to read and understand the functioning of this operator system, its safety features and knowing the manual function in case of emergency.
• Do not modify in any way the automated system’s components. SEA USA Inc. declines all liability concerning the automated system’s security and efficiency if
the used components are not produced by SEA USA Inc. For maintenance, strictly use original SEA USA Inc. spare parts.
• The installer shall supply the user with all information concerning the proper operation of the product, the system’s manual functioning in case of emergency and
shall hand over to the user the warnings handbook supplied with the product.
• SEA USA Inc. recommends the system to have reversing sensor (encoder) on the drive shaft of the motor. In case of swing/linear/in-ground hydraulic
operators/barriers, SEA USA Inc. recommends to install the SAFETY GATE as an additional reversing sensor. Reversing devices are required to prevent the
system from closing on vehicular traffic and/or help to prevent injuries to pedestrians.
• It is recommended to use indicator-lights as well as warning signs for every system. Both should be visible on each side of the gate and well fixed on the frame
structure.
• Do not leave packing materials (plastic, polystyrene, etc.) within children’s reach, as they are potential sources of danger.
• For products having an emergency release, it is recommended to use it only when the gate/barrier is closed.
• Remove all locks connected to the gates before installing the operator.
• Locate the control button: (a) within sight of door, (b) at minimum height of 5 feet so that small children are not able to reach it, and (c) away from all moving parts
of the door.
• Install entrapment Warning Label next to the control button in a prominent location. Attach marking next to the emegency release.
• Do not employ for any reason automatic closing devices (such as timer, loop sensors, or similar), and do not connect any other activation devices.
GENERAL SAFETY REGULATION FOR THE USER
• Sea strongly recommends to follow these instructions literally to prevent very serious damages to persons. This product was designed and built strictly for the
use indicated in this documentation. Any other use, not expressly indicated here, could compromise the good condition/operation of the product and/or be a
source of danger. SEA USA Inc. declines all liability caused by improper use or different use in respect to the intended one.
• Only qualified personnel can install, repair and periodically check this equipment.
• The User must not attempt to repair or to take direct action on the system and must solely contact qualified SEA personnel or SEA service centres. User can
apply only the emergency manual function.
• The system has been designed for the control of vehicular traffic only. Pedestrians or bicycles must have a separate access opening.
• Do not allow children or adults to stay near the product while it is operating. The application cannot be used by children, by people with reduced physical, mental
or sensorial capacity, or by people without experience or necessary training. Keep remote controls or other pulse generators away from children to prevent
involuntary activation of the system.
• Transit through the leaves or barrier is allowed only when the gate/barrier is fully open. Operate system only if it is fully visible, and free of obstructions.
• For products having an emergency release use it only when the door/barrier is closed.
ELECTRICAL CONNECTIONS - SAFETY INSTRUCTIONS
• Disconnect the battery back up, if included, before disconnecting main power supply.
• Always disconnect power supply during installation or servicing of the product.
• All electrical connections from the control panel’s to the operator’s must be made in a waterproof junction box.
• The system requires a separate power supply circuit. Check that the main power supply circuit breakers are separated, intended solely for this equipment and
rated for 15 AMPS. Visually check that the circuit breakers are in OFF position and mark the circuit breakers USED prior to installation.
• Permanent wiring must be used and installed to the operator as required by local electrical codes and It is recommended to do by a licensed electrician.
It is also recommended to check the local building code requirements before making any type of wiring to be sure that all wirings comply with them. Local building
codes will take precedence. It is recommended to use different colours for all wirings’ codes.
• Distance for low voltage control wires, i.e., open input, single leaf, open input and stop input, can run up to 3000 feet with 18 AWG wire. Low voltage controls and
communication wirings must all be separated by a minimum of 1 foot from high voltage power wiring and in a separate conduit.
GROUNDING
• Good grounding and proper surge suppression are an integral part of proper installation for all operator systems. One or all of the followings may require surge
suppressors: high voltage power lines, low voltage power lines, telephone lines, data lines, low voltage control lines and loops. Quantity of surge suppression
requires depends on susceptibility of the area to lightning and power surges. Good grounding is essential to realize maximum protection.
• If the circuit breaker box is located close to the gate/barrier operator system, for example, in a guardhouse, then the ground from that circuit can be used to
ground the gate operator system. Eliminate all 90° bends in ground wires and keep a minimum distance of three feet between the surge suppressor and the
equipment to protect.
• If the power source or circuit breaker box is not located close to the operator system, an Isolated Ground Zone (IGZ) must be created. An IGZ is an imaginary
circle drawn around the operator system. An IGZ can also be created, if the circuit breaker box is located close to the operator system. The operator system not
only includes the operator and control panel, but all accessories and devices associated with it at that controlled entry point. This includes loop detectors, card
readers, digital entries, telephone entries, any device that has or requires grounding and all the surge suppressors. The ground bus is a common ground point
called Single Point Ground (SPG). It is used to bond all the equipments and devices grounded in the IGZ together. The SPG is very important because it helps to
eliminate different ground potentials that can be present on the equipment and that could cause damages even with surge suppressors.
• Do not use or connect the ground wire coming from the circuit breaker box. By using an Isolated Ground Zone, you have to separate the operator system from
the house or building ground. This eliminates ground potentials. It is recommended the ground bus to be located in a separate NEMA type enclosure. All grounds
will be tied to this ground bus.
• Equipment ground wire should be of minimum 12 AWG. The main ground wire from the bus bar to the ground rod should be an 8 or 6 AWG copper wire.
Ground rod should be minimum 10 feet in length, (length depends on local soil conditions).
• For more information, regarding good grounding practices check: National Electric Code art. 250; IEEE Emerald Book, standard 100; International Association
of Electric Inspectors.
• Where possible, install the opener control 7 feet or more above the floor. For products having an emergency release, mount the emergency release 6 feet above
the floor.
USER 1 - 24V
International registered trademark n. 2.777.971
67411071
2
REV 01 - 05/2011