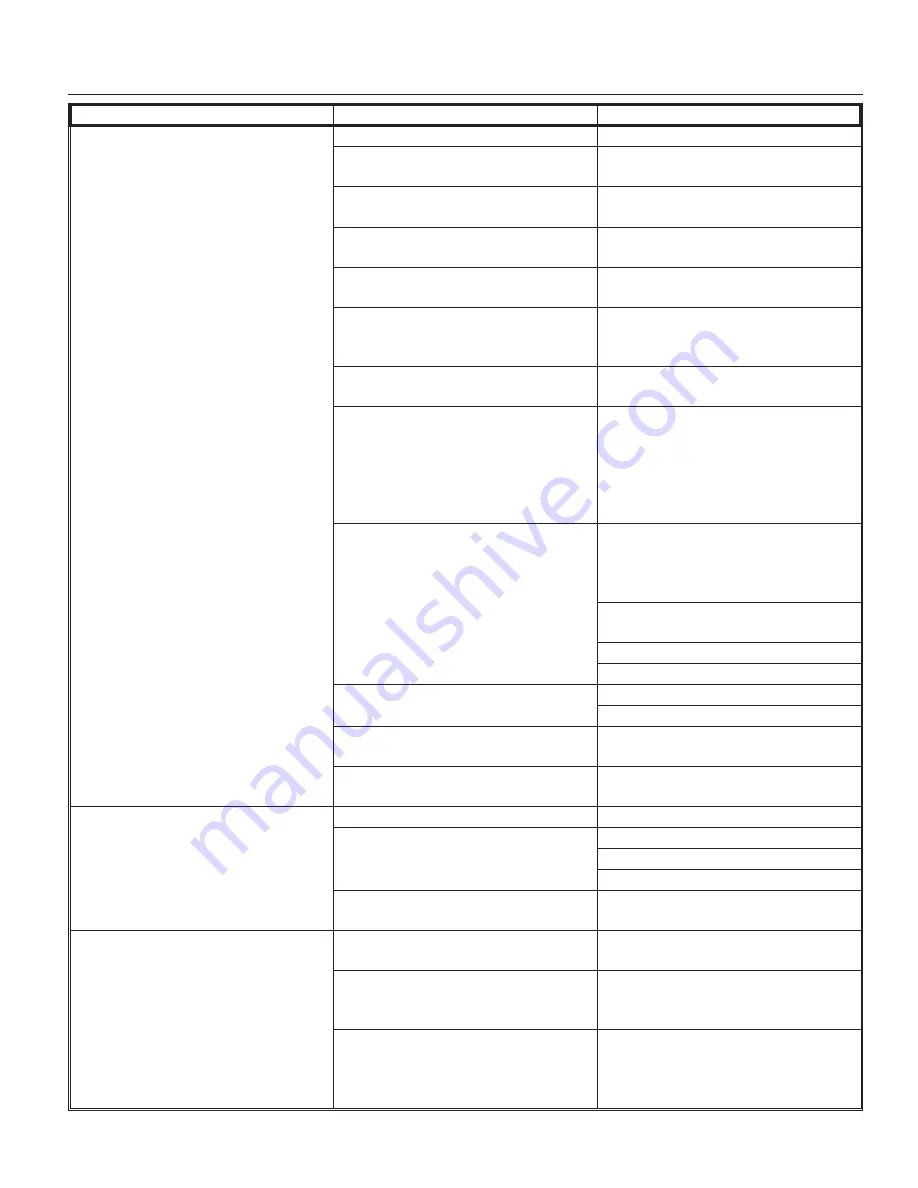
NDE754
March 2000
Page 19
SERVICE DIAGNOSIS
Symptom
Possible Cause
Probable Correction
No ice is made, nothing operates Unit off due to no power
Restore Power
Unit off due to master switch in
OFF position.
Switch master switch to ON.
Unit off due to low water level.
Check water supply, filter, strainer,
float valve. Correct water supply.
Unit off due to ice level sensors
(photo-electric eyes) blocked.
Check/clean ice level sensors.
Unit off due to scale on water level
sensor.
Clean water level sensor.
Unit off due to high pressure
control open.
Check for water interruption (water
cooled) or fan motor failure (air
cooled).
Auger motor hums but does not
turn.
Auger can’t turn. Circuit board has
not yet shut unit down.
Unit is shut down
Circuit board has shut ice machine
down due to high auger motor amp
draw. Check for cause of high amp
draw, including bearings,
gearmotor condition and scale on
auger and in evaporator.
Low pressure control open
Auger not turning due to: motor
failure; auger relay failure on circuit
board; or gears stripped. Check
drive train.
TXV restricted or not metering.
Check bulb temperature.
Lack of refrigerant. Check for leak.
Check for a restricted system
No power to circuit board.
Check harness
HI or low pressure cut out open
Circuit Board gear motor relay will
not close
Check, replace board
Water level or ice level sensor
failed.
Check, replace sensor
No ice, auger motor is turning
Compressor contactor coil is open Check/replace contactor
Compressor will not start
Check start capacitor.
Check start relay
Check compressor windings
Circuit board compressor relay will
not close.
Check, replace board
Unit makes ice, but very slowly.
High discharge pressure because
of a dirty condenser
Clean the air filter and condenser.
Low capacity because the auger
and evaporator are coated with
mineral scale
Clean the water system
Low suction pressure due to low
refrigerant charge
Locate leak. Recover refrigerant,
repair leak, replace dryer,
evacuate and weigh in the
nameplate charge