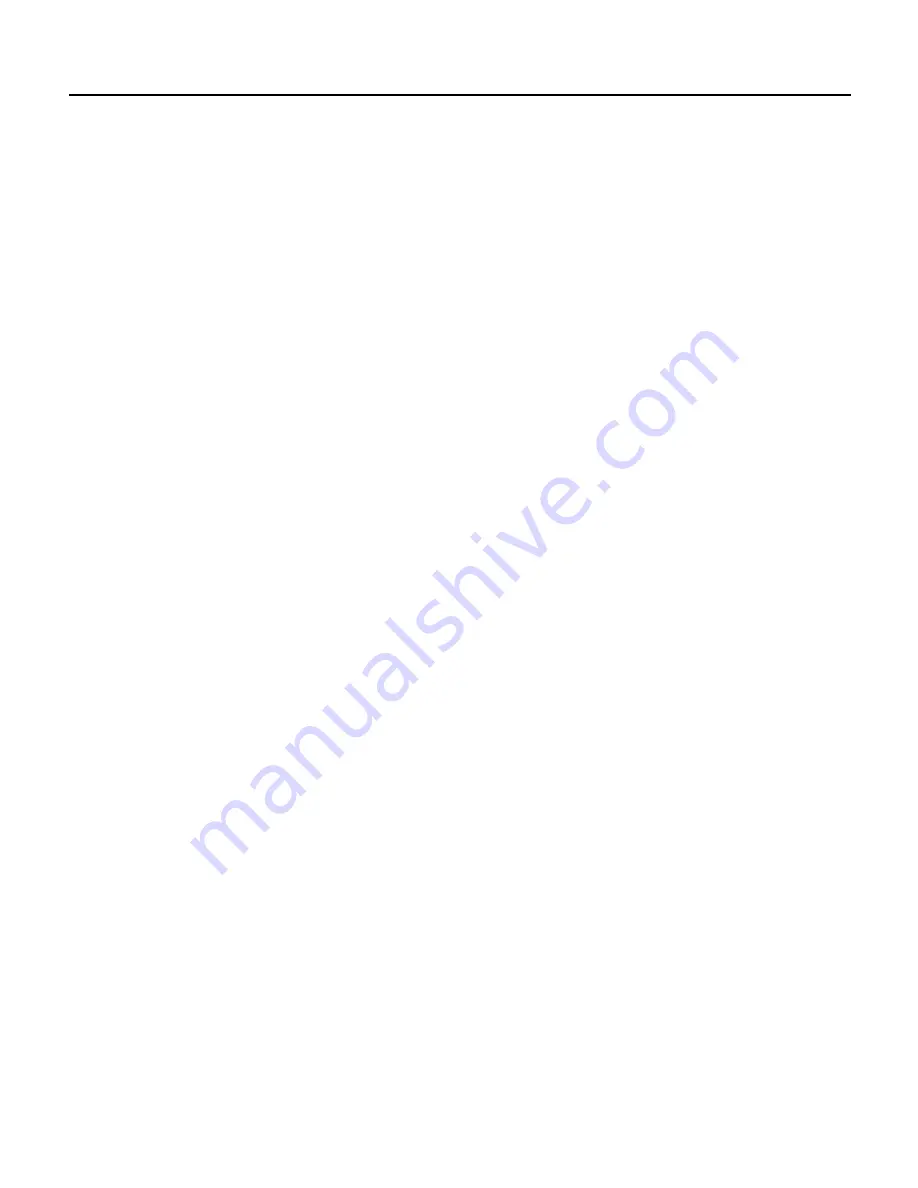
START UP
Pre-Start Inspection
1. Remove the front and side service panels.
2. Check that the styrofoam shipping blocks have
been removed.
3. Inspect the interior of the machine for loose
screws or wires. Check that no refrigerant lines
are rubbing each other. Check that the fan blade
turns freely (air cooled).
4. Check that the unit is installed correctly
according to the final check list (page 8).
Start Up
1. Go through the prestart inspection.
2. Open the hand valve, observe that water enters
the water reservoir, fills the tube from the reservoir
to the evaporator, and then shuts off. Check for
leaks.
3. Switch the master switch on.
The electrical start up sequence is now on
automatic.
A. There should be a short (15 second) delay
before the gearmotor starts.
B. After the gearmotor starts, the compressor will
start.
4. On air cooled models, the condenser will begin
to discharge warm air, on water cooled models,
the water regulating valve will open, and warm
water will be discharged into the drain.
5. The unit should soon be making ice, if desired,
the low side pressure can be checked: it should be
34 psig + or - 4 psig.
The suction line temperature at the compressor is
normally very cold, nearly to the point of frost up to
the compressor body, but not on it.
The air cooled discharge pressure will depend
upon air and water temperatures, but should be
between 220 psig and 300 psig.
The water cooled discharge pressure should be
constant at about 245 psig.
The above numbers are for new, clean machines,
you can expect to see some values higher, and
some lower between different units.
6. THERE ARE NO ADJUSTMENTS TO MAKE,
so replace the panels.
7. Clean and/or sanitize the storage bin interior,
wipe off the exterior with a clean, damp cloth.
8. Give the owner/user the service manual, instruct
him/her in the operation of the unit, and make sure
they know who to call for service.
9. Fill out the manufacturers registration card, and
mail it to the Scotsman Factory.
10. Fill out the field quality audit form, and mail it to
the Scotsman factory.
NME650 & FME800
February 1997
Page 9