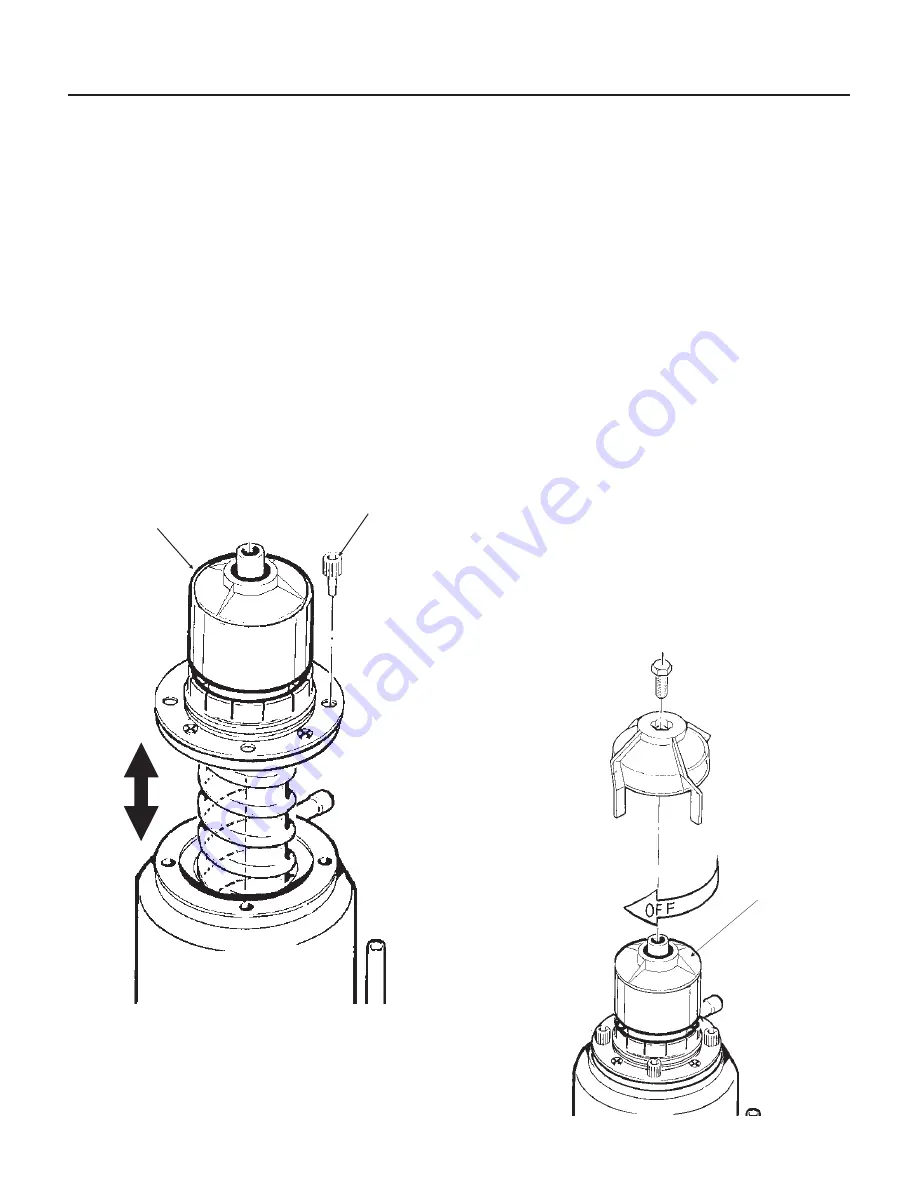
AUGER MAINTENANCE
In some installations the water supply to the ice
maker will be so concentrated with dissolved
minerals, (such as calcium carbonate) that as ice is
made, the evaporator and auger become coated
with those minerals, requiring a more frequent
cleaning than twice per year. If in doubt about the
condition of the evaporator and auger, the auger
can be removed so the parts can be inspected.
Note: Water filters can filter out suspended solids,
but not dissolved solids. “Soft” water may not be
the complete answer. Check with a water
treatment specialist regarding water treatment.
Switch off electrical power, and shut off the water
supply.
For more information on removal of these parts,
see REMOVAL AND REPLACEMENT.
1. To remove the auger, remove front and top
panel. See Removal And Replacement.
2. Push bail clamp back and remove ice chute
cover.
3. Unscrew and remove ice sweep.
4. Remove ice chute from evaporator.
5. Remove 4 allen head screws holding breaker to
evaporator.
6. Pull up on breaker to remove auger.
Allow the auger to dry, the stainless steel of the
auger and evaporator must be clean and bright.
Clean the auger and evaporator as required. DO
NOT HONE THE EVAPORATOR.
7. Replace the water seal.
8. Reverse to reassemble.
Double System RL
November 2000
Page 17
Note:
Flaker Components Shown, Nugget
Components are Similar
DIVIDER, AUGER
AND SLOTTED
COLLAR
ALLEN HEAD
SCREWS
BREAKER
COVER