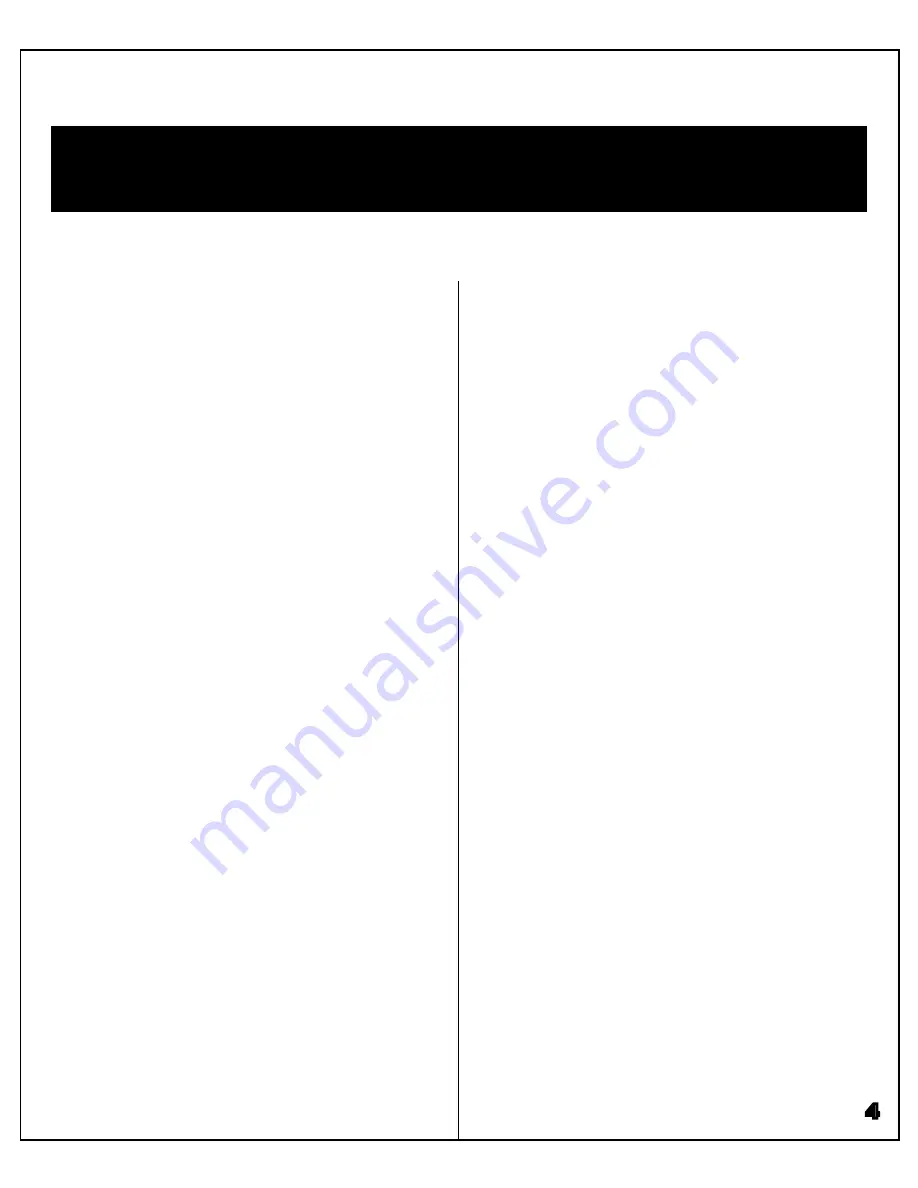
To help ensure safe operation, take a moment to learn the machine’s applications and limitations, as well as po-
tential hazards. CWI Woodworking Technologies disclaims any real or implied warranty and holds itself harmless
for any injury that may result from improper use of its equipment.
Rules for Safe Operation
12.
Do not force stock into the cutterhead. Feed stock
steadily and slowly through the machine.
13.
Avoid working from awkward or off balance positions.
Do not overreach while jointing, and keep both feet on the
floor.
14.
Keep guards in place and in working order. If a guard
must be removed for maintenance or cleaning, be sure it is
properly reattached before using the jointer again.
15.
Never leave the machine running when not in use.
16.
Use of parts and accessories NOT recommended by
CWI may result in equipment malfunction or risk of injury.
17.
Never stand on machinery. Serious injury could result
if the tool is tipped over or if the cutterhead is unintention-
ally contacted.
18.
Always disconnect tool from power before servicing or
changing accessories such as knives, or before perform-
ing any maintenance, cleaning or adjustments, or if the
machine will be left unattended.
19.
Make sure that switch is in the OFF position before
plugging in the power cord.
20.
Make sure the tool is properly grounded. If equipped
with a 3-prong plug it should be used with a three-pole
receptacle. Never remove the third prong.
21.
Do not use this jointer for other than its intended use.
If used for other purposes, CWI disclaims any real implied
warranty and holds itself harmless for any injury, which
may result from that use.
1.
Do not operate the jointer when tired, distracted, or
under the effects of drugs, alcohol or any medication that
impairs reflexes or alertness.
2.
The working area should be well lit, clean, and free of
debris.
3.
Keep children and visitors at a safe distance when the
jointer is in operation; do not permit them to operate the
jointer.
4.
Childproof and tamper proof your shop and all machin-
ery with locks, master electrical switches and switch keys,
to prevent unauthorized or unsupervised use.
5
. Give your work your undivided attention. Even a mo-
mentary distraction can lead to serious injury.
6.
Fine particulate dust is a carcinogen that can be
hazardous to health. Work in a well-ventilated area and
whenever possible use a dust collector and wear eye, ear
and respiratory protection.
7.
Do not wear loose clothing, gloves, bracelets, neck-
laces, or other jewelry while the jointer is in operation.
8.
Be sure that tools, scrap, drinks and other clutter are
removed from the table surface before operating.
9.
Keep hands away from the knives and all moving parts.
Use a brush, not your hands, to clear away chips and dust.
10.
Ensure that knives are securely installed in the cut-
terhead before operating.
11.
Always use clean, properly sharpened knives. Dirty or
dull knives are unsafe and can lead to accidents.
4