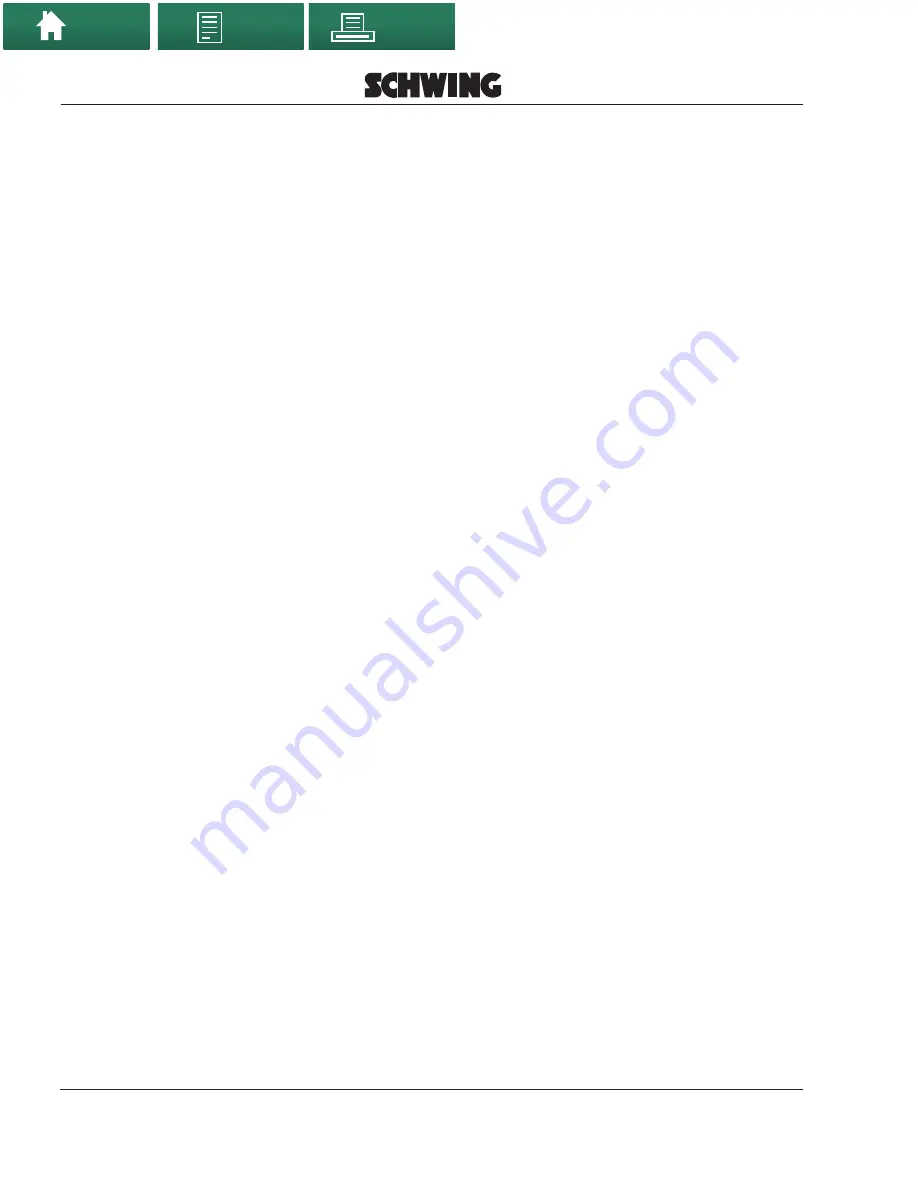
Appendix
Operation Manual - All
S
P Rock Valve Model
s
150
revD
a
te
Operational Area
The
a
re
a
a
ro
u
nd
a
working piece of
e
qu
ipment or point of di
s
ch
a
rge where
d
a
nger
s
c
a
n be enco
u
ntered d
u
e to
the n
a
t
u
re of the m
a
chinery or proce
ss
in
us
e. Do not
a
llow
u
n
au
thorized
pre
s
ence in thi
s
a
re
a
for
sa
fety re
a
-
s
on
s
.
O.
S
.H.A.
Occ
u
p
a
tion
a
l
Sa
fety
a
nd He
a
lth
Admini
s
tr
a
tion. A br
a
nch of the United
S
t
a
te
s
feder
a
l government th
a
t de
a
l
s
with job
sa
fety. They e
s
t
a
bli
s
h
a
nd
enforce
sa
fety reg
u
l
a
tion
s
for ind
us
try
a
nd b
us
ine
ss
. Among the
a
re
as
over
which they h
a
ve
au
thority
a
re con-
s
tr
u
ction job
s
ite
s
a
nd work
s
hop
s
.
Per
s
onal Protective Apparel
Thing
s
yo
u
c
a
n we
a
r to protect yo
u
r-
s
elf from potenti
a
l d
a
nger
s
in
a
con-
crete pl
a
cing environment. Ex
a
mple
s
a
re:
•
S
n
u
g fitting work clothe
s
•
S
teel Toed work boot
s
• Lime re
s
i
s
t
a
nt glove
s
•
Sa
fety gl
ass
e
s
• E
a
r m
u
ff
s
or e
a
r pl
u
g
s
• R
u
bber boot
s
when yo
u
h
a
ve to
s
t
a
nd in concrete
• H
a
rd h
a
t
Point of Di
s
charge
The loc
a
tion of concrete exp
u
l
s
ion
from
a
delivery
s
y
s
tem. Thi
s
c
a
n be
the point of pl
a
cement (the
a
ct
ua
l form
th
a
t i
s
being filled with concrete) or the
cle
a
n-o
u
t
a
re
a
a
fter completion of the
job.
Pour
U
s
ed by the concrete p
u
mping ind
us
-
try
a
nd in thi
s
m
a
n
ua
l
as
a
no
u
n. It i
s
the
s
pecific job for the p
u
mp d
u
ring
a
ny given time period. E.g. “We’ll gr
a
b
l
u
nch right
a
fter the po
u
r
”
.
Prime Mover
The prim
a
ry power
s
o
u
rce for
a
hydr
au
lic
s
y
s
tem. The term “prime
mover
”
i
s
generic in th
a
t i
s
denote
s
neither
a
n intern
a
l comb
us
tion engine
nor
a
n electric motor.
PTO
Power T
a
ke Off. A
s
witch
a
ble o
u
tp
u
t
from the tr
a
n
s
mi
ss
ion or
a
n intermedi-
a
te ge
a
rc
as
e. On
a
concrete p
u
mp it i
s
us
ed to divert the power from the
engine
a
nd drive tr
a
in to t
u
rn the
hydr
au
lic p
u
mp
s
.
Qualified Operator
An individ
ua
l th
a
t h
as
:
• re
a
ched the
a
ge of 1
8
ye
a
r
s
,
a
nd
• i
s
phy
s
ic
a
lly
a
nd ment
a
lly c
a
p
a
ble,
a
nd
• h
as
been tr
a
ined in the proper
oper
a
tion
a
nd m
a
inten
a
nce of the
p
u
mp
a
nd pl
a
cing boom (if
a
ppli-
c
a
ble),
a
nd
• h
as
demon
s
tr
a
ted their c
a
p
a
bili-
tie
s
to their comp
a
ny in re
s
pect to
the oper
a
tion
a
nd m
a
inten
a
nce of
the p
u
mp
a
nd pl
a
cing boom,
a
nd
• c
a
n be expected to perform the
s
e
d
u
tie
s
,
as
ass
igned, in
a
reli
a
ble
m
a
nner.
Qualified Per
s
onnel
A generic term
us
ed to de
s
cribe
a
per-
s
on th
a
t i
s
qua
lified in the
a
re
a
of
a
pplic
a
tion. For ex
a
mple, h
a
ving yo
u
r
boom rep
a
ir
s
in
s
pected by “
qua
lified
per
s
onnel
”
before
us
e wo
u
ld refer to
in
s
pection by
a
certified welder or cer-
tified welding in
s
pector. H
a
ving rep
a
ir
s
to yo
u
r hydr
au
lic
s
y
s
tem done by
“
qua
lified per
s
onnel
”
wo
u
ld refer to
rep
a
ir
s
m
a
de by
qua
lified work
s
hop
per
s
onnel.
Qualified Work
s
hop Per
s
onnel
An individ
ua
l th
a
t:
• h
as
re
a
ched the
a
ge of 1
8
ye
a
r
s
,
a
nd
• i
s
phy
s
ic
a
lly
a
nd ment
a
lly c
a
p
a
ble,
a
nd
• h
as
been tr
a
ined in proper rep
a
ir,
m
a
inten
a
nce,
a
nd in
s
pection pro-
ced
u
re
s
pl
us
the pertinent
sa
fety
r
u
le
s
for concrete p
u
mp
s
a
nd
rel
a
ted e
qu
ipment,
a
nd
• h
as
demon
s
tr
a
ted their c
a
p
a
bili-
tie
s
to their comp
a
ny in reg
a
rd
s
to
the
a
bove mentioned proced
u
re
s
a
nd r
u
le
s
,
a
nd
• c
a
n be expected to perform the
s
e
Home
TOC
TOC