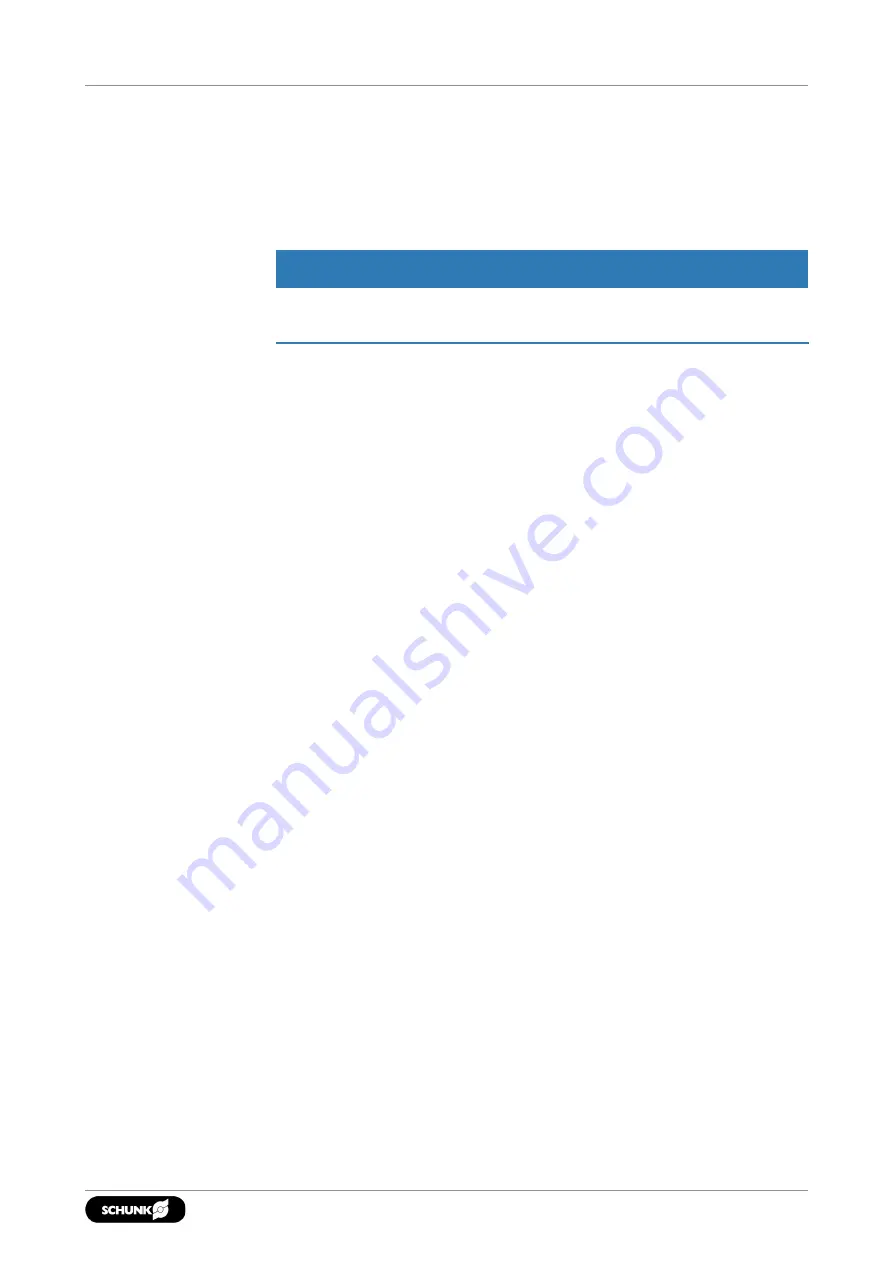
Maintenance and care
• Check the supply hose line to the pressure supply of the
clamping station for damage at regular intervals. The supply
hose line must be of the appropriate nominal hose width and be
completely inserted into the air connections and securely
clamped. Protect the supply hose line from kinking and avoid
tensile loads. After replacing the hose line, perform a leak test.
CAUTION
Only polyurethane hydrolysis-resistant air hoses with
appropriate diameters are to be used.
Detaching thread on the clamping modules
The clamping modules installed in the clamping stations have two
detaching threads located opposite each other. This allows, for
example, the clamping modules to be more easily removed from
the clamping station for performing maintenance work.
7.1 Leak test
As part of a leak test, the air and plug-in connections and the
coupling mechanism should be tested for leaks.
The following components are required for the leak test: pressure
gauge, supply line with coupling nipple.
Performing the leak test
1. Connect the components to the air connection in the following
order: pressure gauge, supply line with coupling nipple.
2. Pressurize the clamping system with compressed air.
3. Test the clamping station for leaks in both module positions.
To identify any leaks in the clamping station, no clamping pallet
should be fitted.
If the clamping system has leaks, check the entire pneumatic
system (e.g. using leak detector spray). If any leaks are identified,
check the seals and replace them if necessary. Leaks at the plug-in
connections or in the pneumatic lines, for example, must be sealed
and any defective components replaced.
35
02.00 | NST3 | VERO-S quick-change pallet system | en | 1344366
Summary of Contents for VERO-S NST3 400-250
Page 43: ......