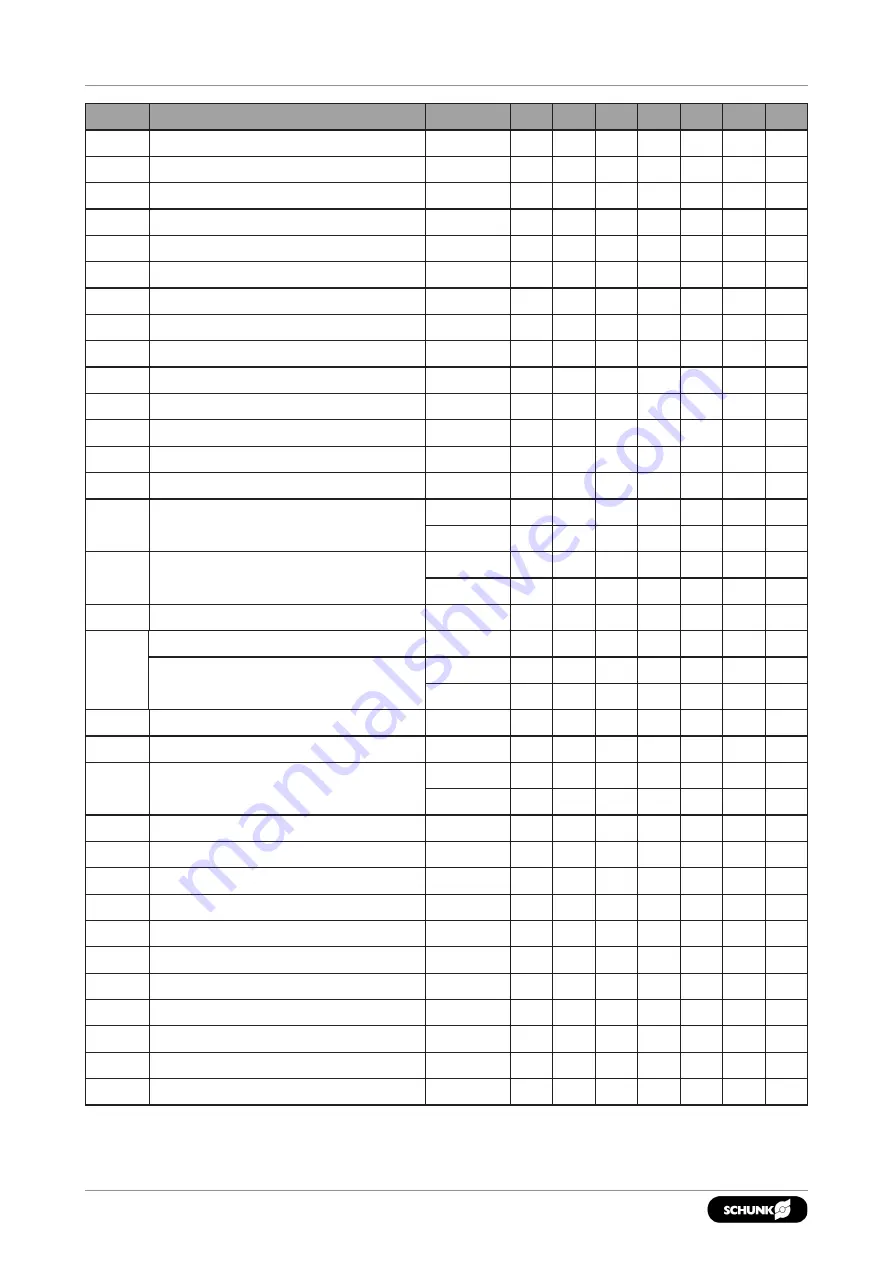
42
02.00 | KSH3 IM | Assembly and Operating Manual | en | 1477686
Sealing kits, accessory packs and parts lists
Item
Designation
Quantity
a
b
c
d
e
y
z
14
Cover
1
●
21
Cupped-type lubrication nipples
4
●
21
Conical lubrication nipple
4
●
●
●
22
Sound absorber
1
●
23
Locking screw
2
●
34
Cylindrical pin
2
●
35
Angular plug
2
●
36
Proximity switch
2
●
37
Supply cable
2
●
40
Turcon Glyd Ring
1
●
●
41
Turcon Glyd Ring
1
●
●
45
O-ring DIN ISO 3601
1
●
●
47
Sealing ring
1
●
●
48
Flat seal
10
●
●
60
Set-screw
2
●
●
●
4
●
62
Set-screw
6
●
●
●
4
●
64
Countersunk screw ISO 14581
2
●
65
Countersunk screw
9
●
Cylindrical screw
15
●
●
13
●
66
Cylindrical screw
2
●
69
Screw
1
●
70
Sealing plug
3
●
4
●
●
71
Cylindrical screw
1
●
72
Washer
2
●
81
Plug
4
●
●
82
Fitting screw
2
●
●
83
O-ring DIN ISO 3601
4
●
●
●
84
Screw
4
●
●
85
Clamping sleeve
2
●
●
86
Screw
8
●
●
87
O-ring DIN ISO 3601
10
●
●
89
Set-screw
2
●
●
93
Set-screw
2
●
●