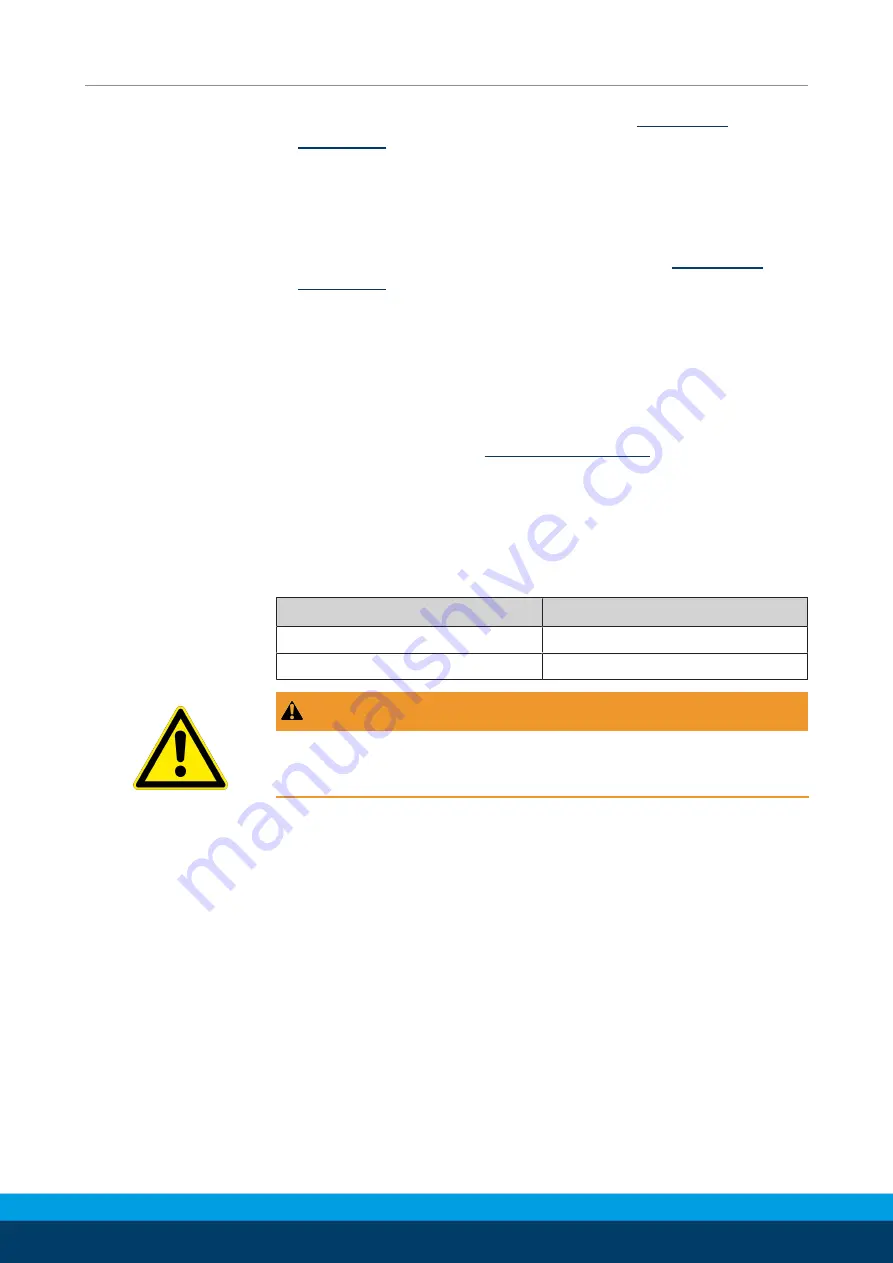
Assembly
18
04.00 | SWG | Assembly and Operating Manual | en | 389453
Ø
Check the evenness of the bolting surface,
18].
Ø
Connect the supply lines to the main air connections "A" and "B".
✓
Connect the air connections.
OR: Mount the throttle valve to throttle and/or damp the
product sufficiently.
Ø
Connect the product with the machine/system,
18] .
✓
If necessary, use appropriate connection elements (adapter
plates).
✓
Observe the maximal tightening torque, admissible screw-in
depth and, if necessary, strength class.
Ø
Connecting the sensor, see assembly and operating manual of
the sensor.
Ø
Assembling the sensor,
21].
Further information
2
[
}
20]
5.2 Mechanical connection
Evenness of the
mounting surface
The values apply to the whole mounting surface to which the
product is mounted.
Requirements for evenness of the mounting surface (Dimensions in mm)
Edge length
Permissible unevenness
< 100
< 0.02
> 100
< 0.05
WARNING
Risk of injury when the machine/system moves unexpectedly!
Switch off power supply.