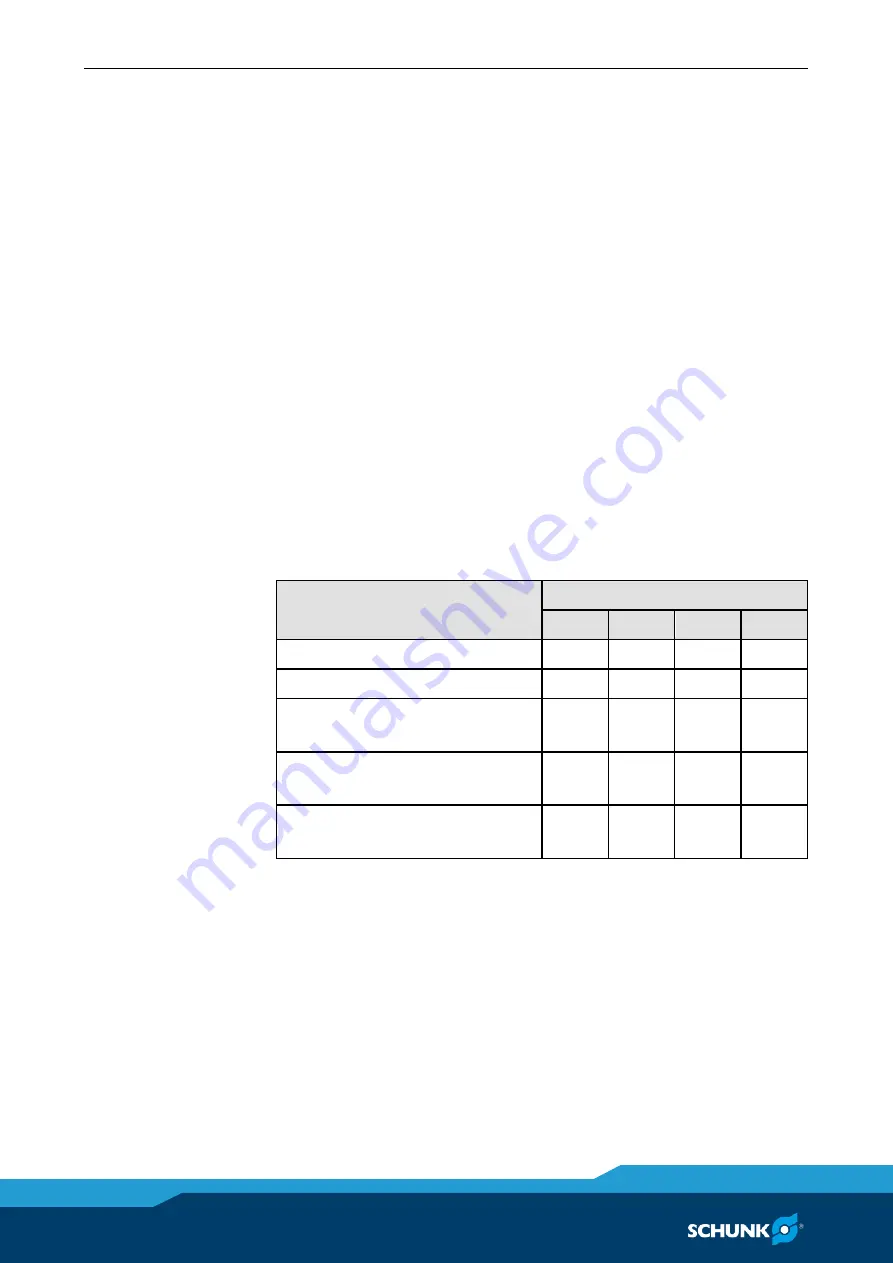
Assembly
22
02.00|PZH-plus 020-075|en
Mounting the sensor
NOTE
Observe the assembly and operating manual of the sensor for
mounting and connecting.
The product is prepared for using sensors
• Exact type designation of the compatible sensors, see catalog.
• Technical data of the matching sensors, see assembly and operat-
ing manual and data sheet.
– The assembly and operating manual and the catalogue data
sheet are included in the scope of delivery and can be down-
loaded from www.schunk.com.
• If you require further information on sensor operation, contact
your SCHUNK contact person or download information from our
homepage.
Overview of sensors
Designation
PZH-plus
20
30
50
75
Inductive Proximity Switch IN 80
x
x
x
x
Magnetic Switch MMS 22
x
x
x
x
Programmable Magnetic Switch
MMS-22 PI1
x
x
x
x
Programmable Magnetic Switch
MMS-22 PI2
x
x
-
-
Programmable Magnetic Switch
MMS-P 22
x
x
-
-
5.2
5.2.1