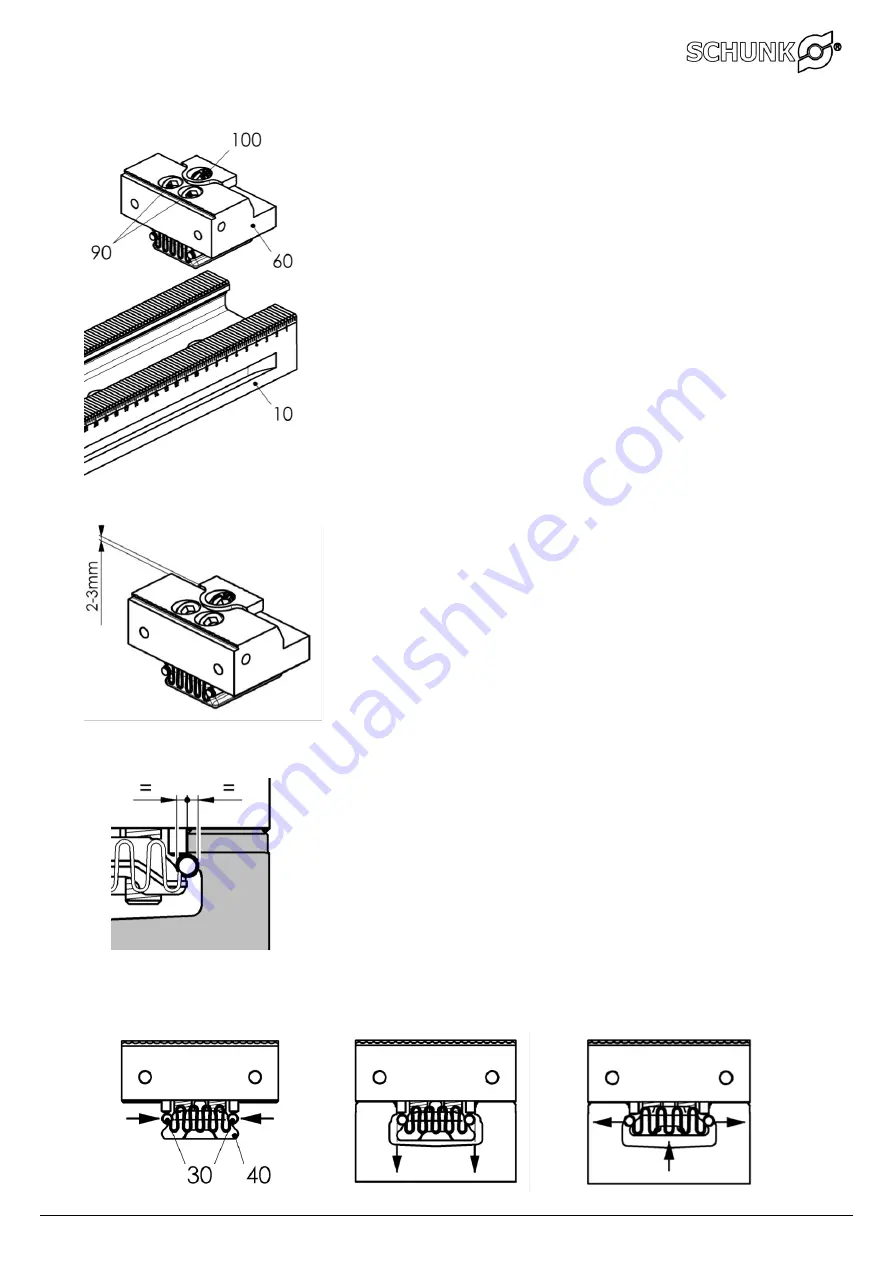
_________________________________________________________________________________________
schunk.com
XND.00019.003_A – 10/2018
32
Adjustable jaws:
4) 6) 11)
9)
2) 3)
5)
8)
1)
It is important to ensure that the gearing of the base plate
and jaws is clean and free from chips.
2)
Release the two M10 fixing screws (No. 90) far enough so that
the locking rollers with the wave springs
(No. 30) are located in the upper indent of the clamping buckle
(No. 40).
3)
When the adjustable jaw (No. 60) has already been clamped,
release the screws by approx.3 turns. This means that the
locking rollers are in open position.
4)
Use the clamping screw (No. 100) to open the clamping jaw far
enough so that the upper surface of the clamping jaw projects
by approx. 2 to 3 mm above the adjustable jaw.
5)
Insert / extend the adjustable jaw from above into the base
plate (No. 10).
6)
When positioning the adjustable jaw for the respective
workpiece size it is important to ensure that the upper face of
the clamping jaw projects by approx. 2 to 3 mm above the
adjustable jaw; if necessary, the clamping screw (No. 100) has
to be opened to achieve this.
7)
Position the adjustable jaw in the gearing to suit the clamping
opening.
8)
Tighten the two M10 fixing screws (No. 90); the clamping
buckle is pulled upwards, the locking rollers are pushed
outwards and clamped in close contact with the shape between
the clamping buckle and the base plate.
9)
Visually check that the locking is correct; the locking rollers
must make full contact on both sides with the round shape of
the base plate, which means that they are exactly half-way
under the base plate. If there is any doubt, the locking should
be released and the process repeated.
10)
Tighten the M10 fixing screws (No. 90) with a torque of 50 Nm.
11)
Use the clamping screw (No. 100) to return the clamping jaw to
its optimum home position with the top surface of the
clamping jaw protruding by 2 to 3 mm above the adjustable
jaw.