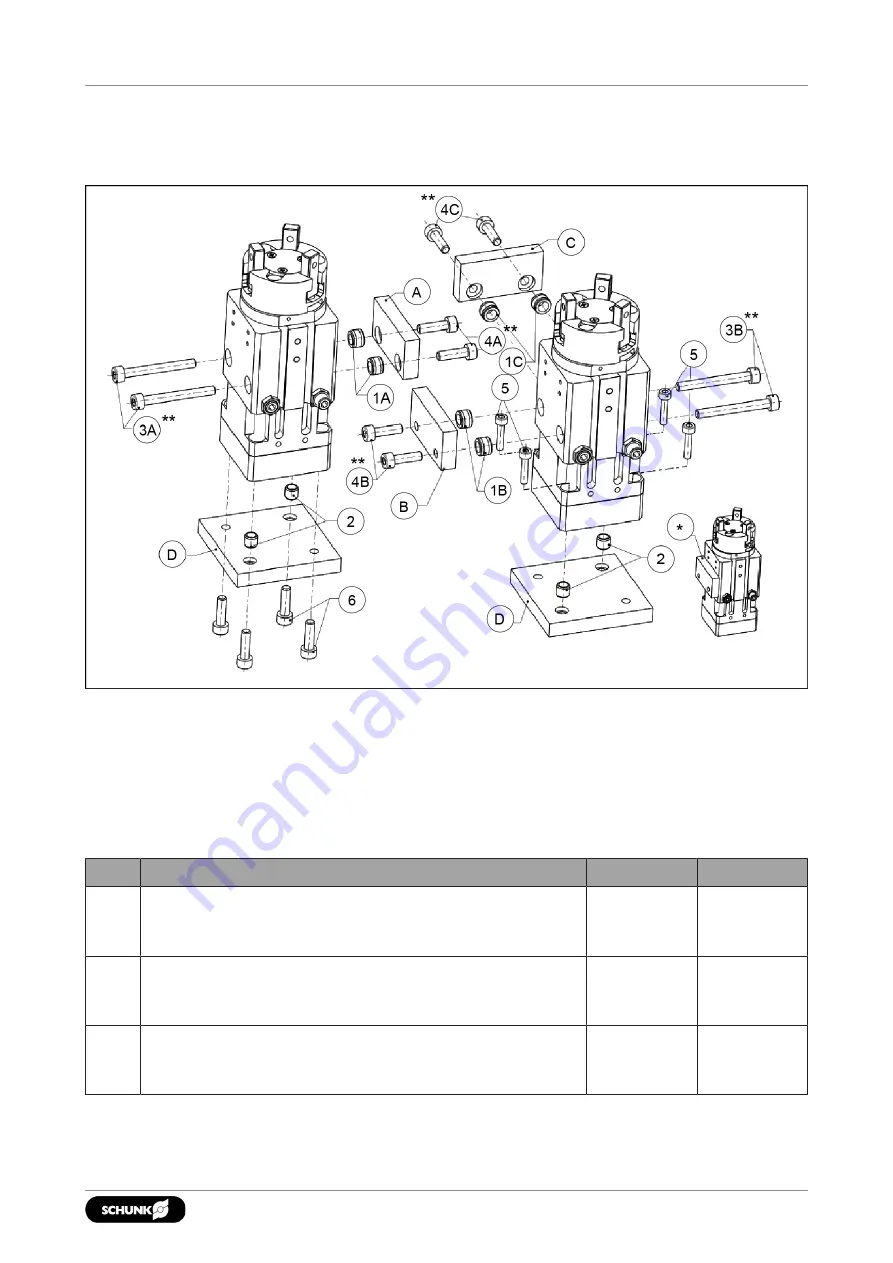
Assembly
5.2 Connections
5.2.1 Mechanical connection
Mounting the GSM on the side and base side
** To ensure the function of the sensors, the A2 screws from the
accessory pack are to be used.
For process-reliable monitoring, adapter plates should be
made of non-ferromagnetic material.
Item GSM - SFL basic size
40
64
1A
1B
1C
Centering sleeve for lateral mounting of the unit and
fitting depth in the mounting plate
Ø8
2.5 deep
Item 206
Ø10
3 deep
Item 205
2
Centering sleeve for mounting the unit on the base side
and fitting depth in the mounting plate
Ø6
2.5 deep
Item 205
Ø10
3 deep
Item 205
3A
3B
3C
Thread diameter for screwing through for mounting
the unit at the side
M4
Item 232
M5
Item 232
21
06.00 | GSM-Z | Assembly and Operating Manual | en | 389110