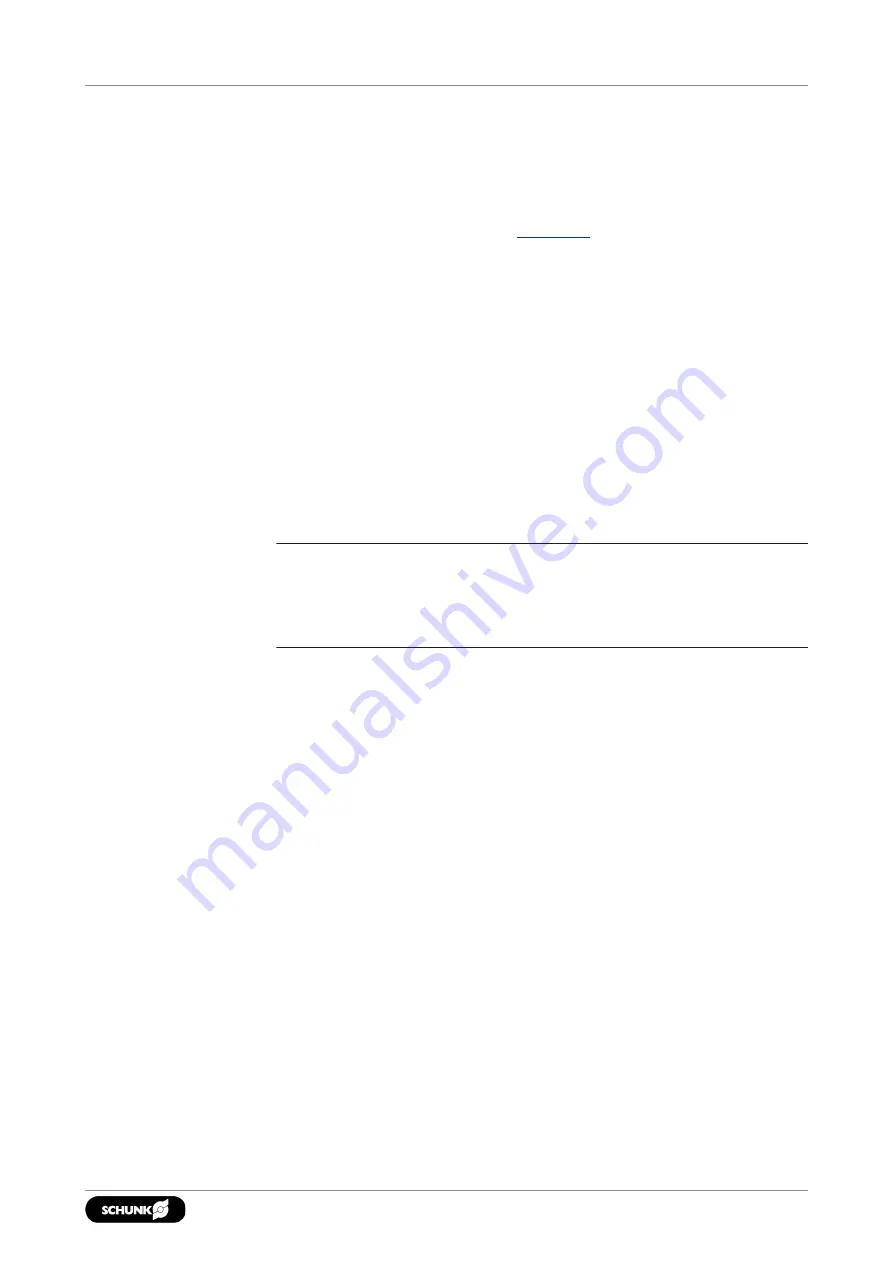
Maintenance
Clean all parts thoroughly and check all parts for defects and wear.
The unit is
assembled
in reverse order; finish by re-adjusting the
end positions Adjusting the end positions.
8.9 Replacing an elastomer for E variants
Position of the item numbers,
The elastomers have a limited lifespan, depending on the load. For
this reason, their function should be checked regularly. The
elastomer is working correctly if the unit moves gently to the end
positions. When replacing an elastomer, the complete additional
parts list for elastomer dampening should be ordered.
Proceed as follows with the replacement:
1. Remove the compressed air lines.
2. Loosen the counter nut (124).
3. Remove the shock absorber (121) from the unit and remove
the sleeve (122). If the latter cannot be loosened from the
shock absorber, it may be helpful to use a small bar magnet or
turn the unit by hand.
NOTE
If the shock absorbers are installed vertically (horizontal axis of
rotation of the module), make sure that the sleeve (122) and the
ball (142) are secured against falling out.
Clean all parts thoroughly and check all parts for defects and wear.
The unit is
assembled
in reverse order; finish by re-adjusting the
end positions Adjusting the end positions.
49
11.00 | GSM-P | Assembly and Operating Manual | en | 389104
Summary of Contents for GSM-P 32
Page 59: ......