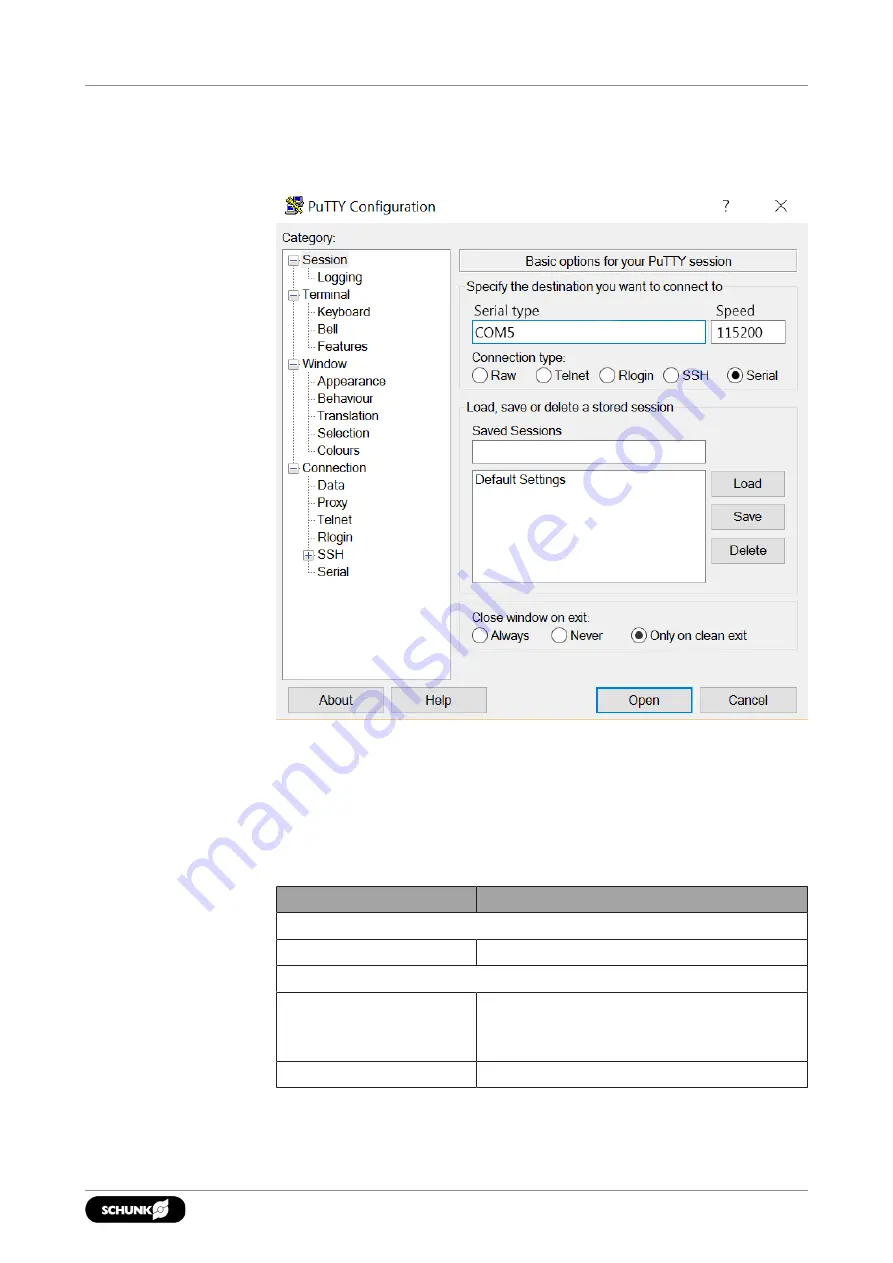
Assembly
Starting and setting up PuTTY
1. Start PuTTY (via icon on desktop or in start menu).
2. Make the following configuration settings:
Note
: The usual Windows shortcuts Ctrl+C and Ctrl+V will not
function in the console window; Ctrl+C even leads to an active
process being terminated. In order to copy text in the console
window to the clipboard, select this with the mouse. Right-clicking
will then insert the text from the clipboard. To avoid error
messages due to copied over formatting, tabs or graphics, it is
recommended that you only copy unformatted plain text.
Area / command
Setting
Configuration > Session
Connection type
Select
Serial
Configuration > Connection > Serial
Serial line
Select the COM port previously
identified as the connection interface in
the device manager.
Speed
Enter
115200
(baud rate)
31
01.00 | FTR-AXIA | Assembly and Operating Manual | en | 1398962
Summary of Contents for FTR-AXIA
Page 51: ......