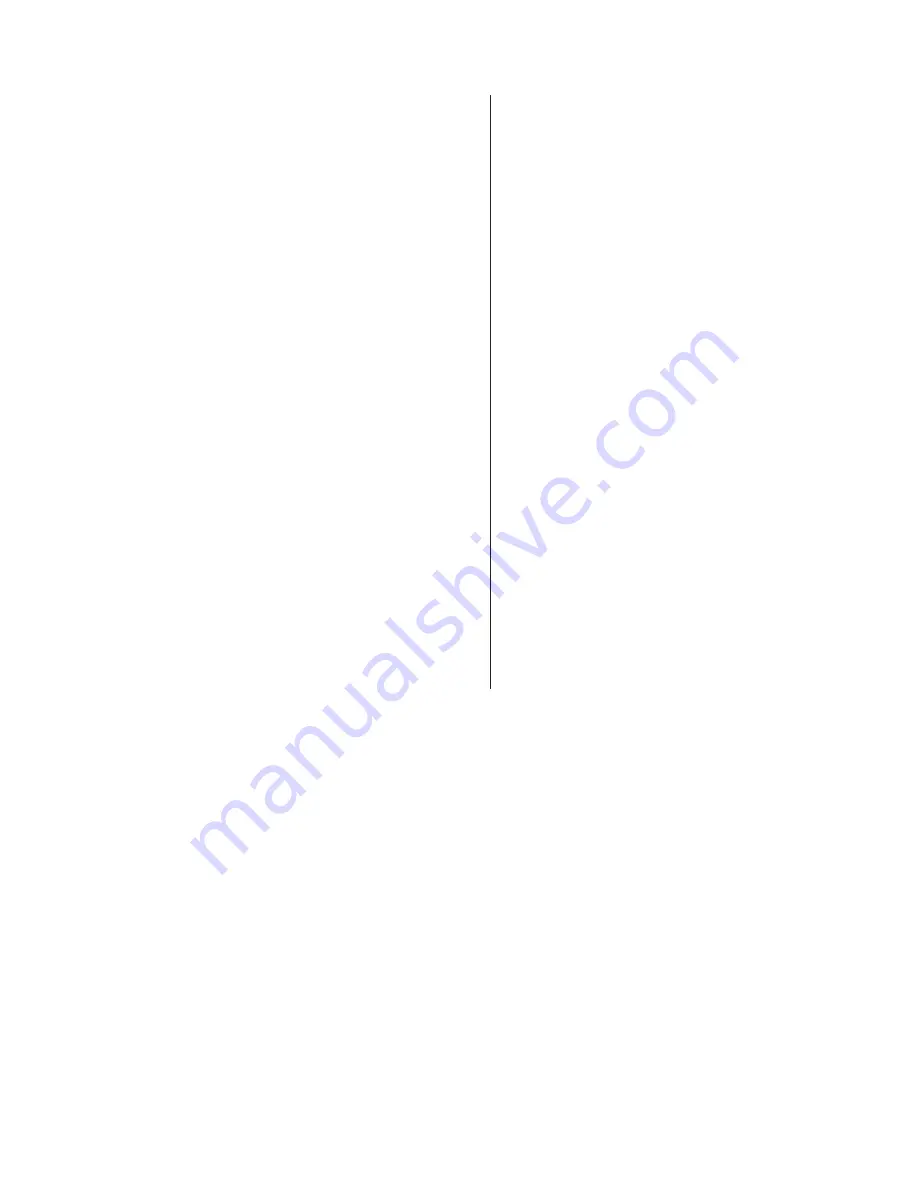
DIRECTION OF ROTATION
As the compressor starts, check the rotation of the
units, Standard rotation is clockwise, viewing the
compressor from the side of the sight glass. A rota-
tion arrow, is placed on the flywheel at the factory.
Should the rotation be incorrect, disengage the power
and correct the motor wiring.
WARNING: AFTER THE COMPRESSOR IS STARTED,
IT WILL OPERATE AUTOMATICALLY.
START-STOP (PRESSURE SWITCH CONTROL)
When the air pressure in the receiver reaches the
preset high pressure level the pressure switch opens,
electrically stopping the compressor driver motor. As
the air is used from the receiver the pressure drops
allowing the pressure switch to close at the preset
low pressure level, restarting the driver motor.
UNPACKING INSTRUCTIONS
The two stage compressor was inspected at the fac-
tory and packaged to protect against shipping dam-
age. When you unpack your unit, inspect for damaged
or missing parts. If there is any damaged or missing
part, the transportation company’s agent should make
a notation to the effect on the Bill of Lading.
Claims,
should be settled directly with
the transportation company.
INSTALLATION
The compressor must be placed in a clean and well-
ventilated room. Compressor should be located
at least 12 to 18 inches away from a wall or other
obstruction that will impede the flow of air through
the fan-bladed flywheel.
Rotation of the fly-wheel
must be in the direction of the arrow cast into the
flywheel.
The compressor should be as near a possible to air
outlets to avoid long pipe lines. Do not place com-
pressor where heat is excessive. Provide adequate
fresh air and exhaust ventilation from area in which
the compressor is located.
Place compressor on a firm, level floor. Permanent
installations should be bolted to the floor. Bolting
holes are provided in the base feet. Shim compressor
level before bolting down to floor. Avoid putting stress
on a foot by pulling it down to floor. This may cause
abnormal vibration.
Remove wood shipping skid
before installation.
INSTALLATION AND OPERATING INSTRUCTIONS
LUBRICATION OF COMPRESSOR
This compressor was shipped without oil. Before operating, fill crankcase with oil to level on oil sight gauge. Do
not over fill. Oil recommended: Premium Grade SchraderAir 826020 - 30WT Non-Detergent. Change oil every
three (3) months or 500 hours. After initial start up change oil after first two weeks of operation. If oil turns
milky replace oil and move unit to less humid conditions.
PRESSURE SWITCH ADJUSTMENT & UNLOADER
The pressure switch has a range adjustment and a differential adjustment. See instructions located under pres-
sure switch cover. The Cut-Out (Compressor Shutdown) is the pressure at which the contacts open, and the Cut-
In (Compressor Restart) is the pressure at which the switch contacts close.
Pressure switch controls the opening and closing of the contacts in the magnetic starter. Do not wire electric
motor directly to pressure switch.
The pressure switch has an unloader or bleeder valve which unloads compression from the compressor for a
loadless start-up. Each time the compressor cuts off air should be released to atmosphere from the bleeder
valve. Air will disperse from this valve for only a few seconds, then stop. (Check Daily)
AIR INLET FILTER/SILENCER
It is very important that the air inlet filter/silencer be kept clean at all times. A dirty inlet filter reduces the
capacity of the compressor.
3
Summary of Contents for SA315240H346
Page 8: ...823015 Two Stage Compressor Pump 8...
Page 10: ...10...