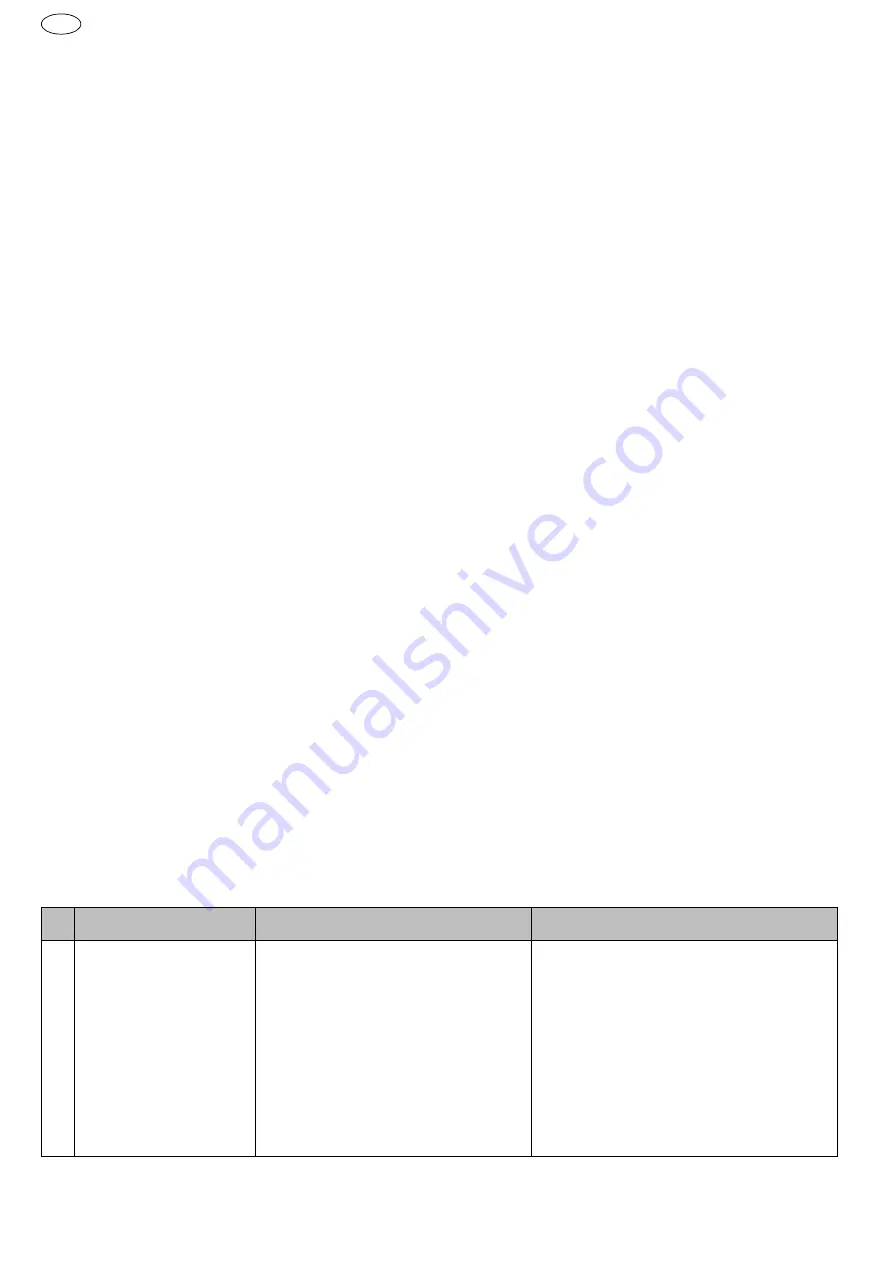
II/12
SEM
GB
4. Screw the oil drain screw closed.
5. Add the prescribed quantity of oil.
6. Check the oil level, correct if necessary.
Insert the oil filler plug or oil dipstick.
7. Dispose of used oil according to applica-
ble regulations.
L
As the mineral oil, we recommend Art. No.
B111002, synthetic oil Art. No. B111006.
Using incorrect oils shall void the warran-
ty.
Mixing synthetic and mineral oil can dam-
age the compressor!
2.6.8 Check screw fittings
1. Check all screw connections for tight fit
and retighten if necessary.
2. Observe the tightening torques (tighten-
ing torques calculated according to VDI
2230).
2.6.9 Clean intake filter
See Part 1 of the Instruction Manual.
L
Do not purge the intake opening. No for-
eign objects may enter.
Never operate the compressor without an
intake filter.
2.6.10 Cleaning/replacing the
check valve
1. Unscrew the locking screw (Figure 6a).
2. Clean the insert and seat.
3. Replace the insert in case of damage,
squeezing or hardening.
4. If the seat is damaged, replace the entire
check valve.
2.6.11 Replacing the safety valve
1. Detach the safety valve (item 11) by un-
screwing it anticlockwise.
2. Screw the new safety valve into place by
screwing it clockwise.
2.7 Decommissioning
Observe the safety instructions!
2.7.1 Preservation
Preservation of oil-lubricated compressors is
necessary if the compressor is taken out of
service for a long period (over 6 months) or
is new from the factory and will not be oper-
ated until much later.
1. Switch off the compressor. Disconnect
the power supply.
2. Allow the oil to drain. See Chap. 2.6.7.
3. Fill corrosion inhibiting oil (viscosity SAE
30). Insert the oil filler plug or oil dip-
stick.
4. Allow the compressor to warm up, switch
it off.
5. Refit intake filter, seal watertight with
Scotch tape.
6. Switch off the compressor. Disconnect
the power supply.
7. Drain condensate.
8. Depressurise the compressor.
Store the compressor dry and do not subject
it to large temperature fluctuations.
2.7.2 Disposal
Dispose of the unit and packaging materials
according to applicable regulations.
2.8 Troubleshooting
Observe the safety instructions!
Problem
Cause
Remedy
A Protective motor
switch interrupts
power supply.
In case of malfunctions (e.g.
overheating; low voltage;
extension cable too long or
with incorrect cross-section),
the protective motor switch is
tripped.
X
Switch off the compressor. Wait a
short while. For compressors
with an external protective motor
switch: actuate the switch.
Switch on the compressor.
If the protective motor switch is
triggered again: switch off the
compressor. Disconnect the pow-
er supply. Contact the service
partner.
Summary of Contents for SEM 255-10-50 W
Page 2: ......
Page 3: ......
Page 4: ......
Page 65: ...SEM II 47 RUS 1 2 3 Schneider Druckluft GmbH 1 X X X X X X X X...
Page 70: ...II 52 SEM RUS 2 8 X B X C X X X A X D X 2 4 4...
Page 71: ...SEM II 53 RUS E X X X X 2 6 5 X X F X G X 2 6 10 X H X 2 6 5 X E I X X J X X X...
Page 72: ...II 54 SEM RUS 2 9 www schneider airsystems com td Schneider Druckluft 2 10 2 1 K X X...
Page 73: ......