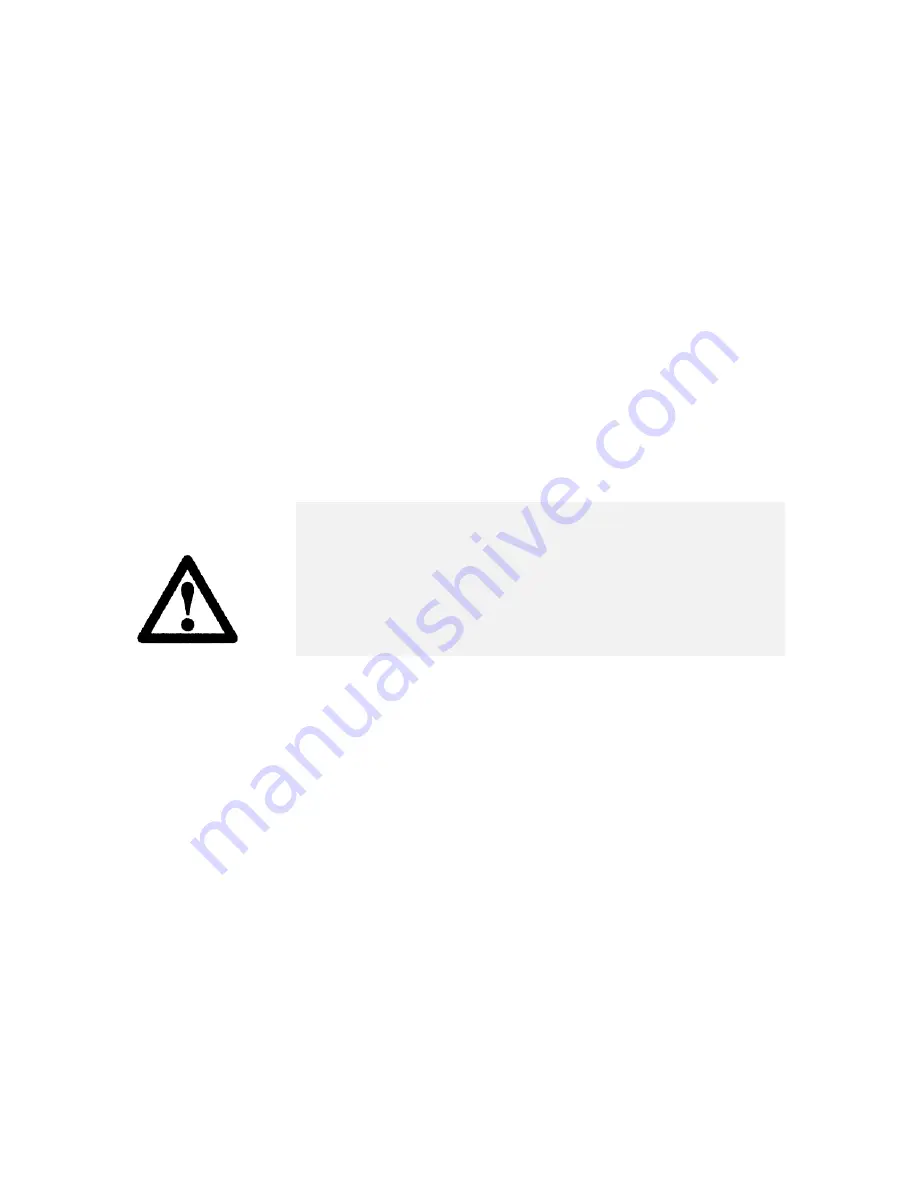
Instructions for Use SS 20.60
Page 13/16
8 Service information
Maintenance
The sensor tip must be checked regularly for contamination and
must be cleaned when required. Contamination of the sensor
element may lead to a false measurement. It is recommended to
check it once a year and more frequently if it is heavily
contaminated.
Cleaning the sensor tip
The sensor tip can be cleaned to remove dust/dirt by moving it
carefully in warm water containing (a) washing-up liquid; if
necessary a very soft brush can be used. Before putting it back
into operation, wait until the sensor tip is completely dry.
ATTENTION
Do not use strong cleaners, solvents, brush or
other hard objects
.
Recalibration
If the customer has made no other provisions, we recommend
repeating the calibration at a 12-month interval. To do so, the
sensor must be sent in to the manufacturer.