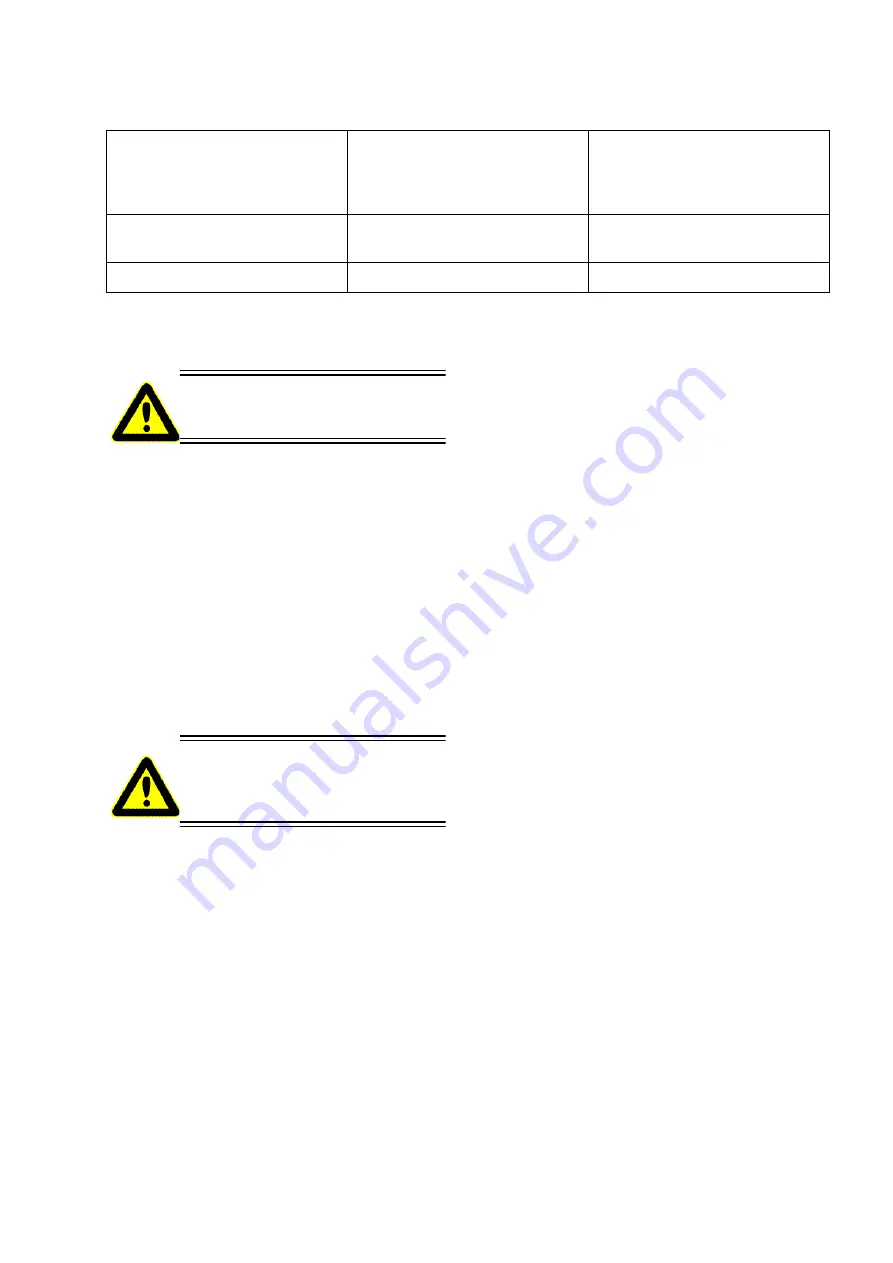
Schmid & Wezel
D75433 Maulbronn
Seite / Page
29/ 39
Ausführung / Version
05.2007
Pump is running, pressure is built
up,
but blades closely slowly or not at
all
20. Blade clearance too small
blades cannot move freely
Adjust blade clearance
see operating manual chapter
4.1.2
Moving blade has too much clear-
ance in the mounting
21. Slide bushings (37) are worn
Replace slide bushings
No cutting performance
22. Knife blade is blunt
Remove and sharpen blades
Table 1: Troubleshooting
6. Cleaning and maintenance
6.1 Daily cleaning after completion
of the slaughters
Continuous reliable operation can only be assured if
the cutter is kept hygienically clean at all times. The
machine should normally be disinfected before each
cleaning.
Observe the applicable safety and hygiene regula-
tions (DIN EN 1672)!
Disinfectants must not be allowed to come into di-
rect or indirect contact with foodstuffs. Rinse the
machine with clear water after disinfection.
6.1.1 Disinfection
Disinfect the machine during operation after every
cut with hot water (82° C).
6.1.2 Cleaning the cutter
Clean the machine after use with a cloth, brush and
warm water (40 - 55° C). Stubborn or encrusted
soiling must be soaked beforehand. Clean using a
cleaning agent, preferably as a foam, that is applied
to the surface to be cleaned and allowed to work for
15 - 20 minutes. Subsequently wash off the dis-
solved soiling manually with warm water.
Disconnect the machine from the
works mains before all cleaning
and maintenance work!
Do not use aggressive solvents!
Do not use steam or high-pres-
sure cleaners! Do not immerse
the machine in water!
Recommended cleaning agents
Diversey Lever Tego 2000: Surface-active disin-
fectant
Diversey Lever GmbH
Mallaufstr. 50-56, 68219 Mannheim
P3-topax 91: Surface-active disinfectant
Henkel-Ecolab Deutschland GmbH
Postfach 13 04 06, 40554 Düsseldorf
A cleaning plan and further details can be obtained
from the above addresses.
The above cleaning agents are only a recommenda-
tion; if other cleaning agents are used, the customer
should examine the material compatibility and the
compliance with the hygiene regulations.
6.1.3 Lubricants and hydraulic oil
The lubricant and the hydraulic oil have to meet the
regulations for the foodstuffs sector (DIN 1672).
Recommended lubricating grease
Klübersynth UH1 14-22 (1 kg special grease in can)
Grade: Approval H1
Order No.001 365 621
Air conditioner
Acid-free branded oil (001 365 612/11) with a vis-
cosity of 3-4 E/20°C, anilin point 60° C.
Oiler setting: 1 drop of oil every approx. 15 cuts
Recommended hydraulic oil
Shell Risella D15 (ISO VG 10 - ISO VG 68 to DIN
51519)
Grade: without approval H1
Order No.001 365 614