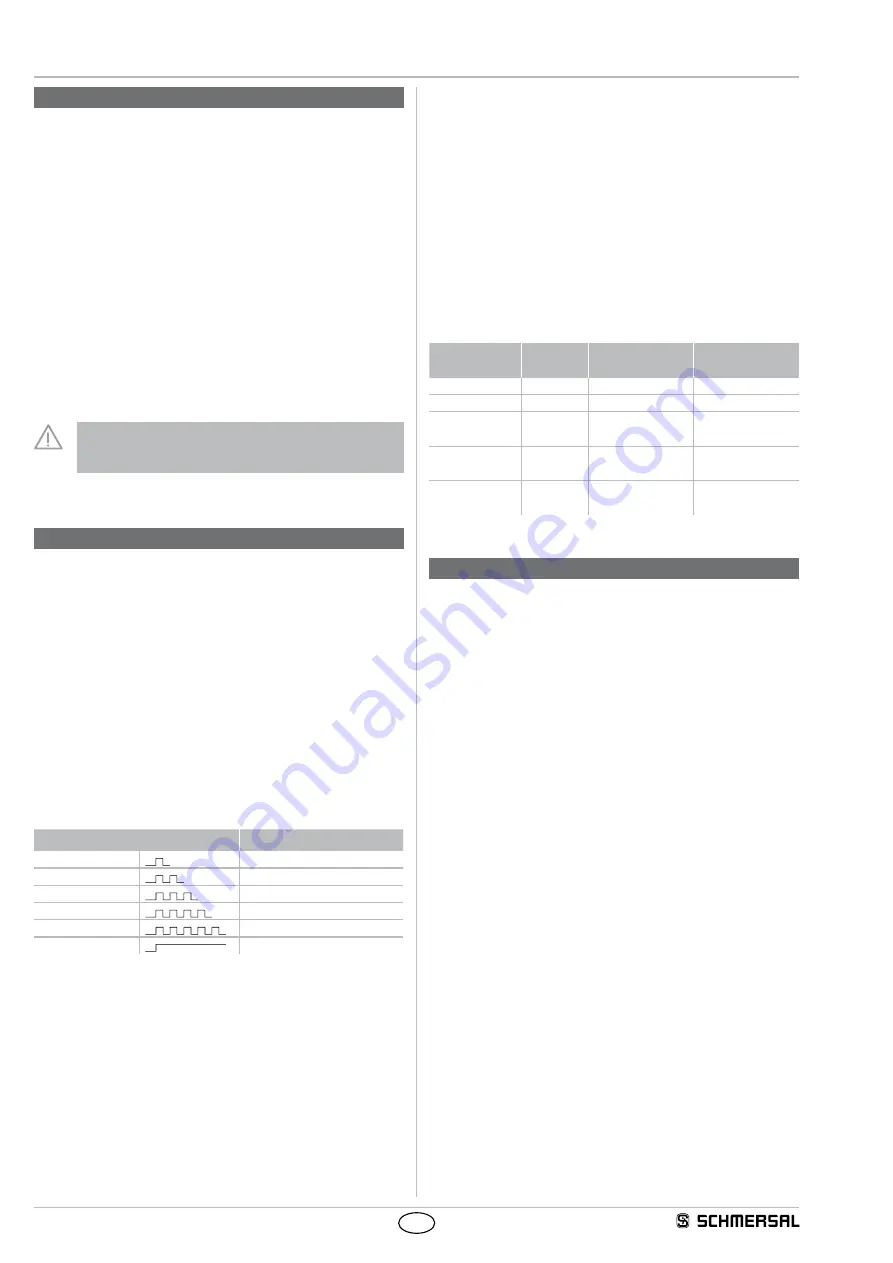
6
Operating instructions
Safety sensor
EX-CSS 180
EN
5. Set-up and maintenance
5.1 Functional testing
The safety function of the safety components must be tested.
The following conditions must be previously checked and met:
1. The installation is executed according to the instructions
2. The connection is executed correctly
3. The safety component is not damaged
4. The system is free of dirt and soiling (in particular metal chips)
5. Check cable entry and connections in a de-energised condition
5.2 Maintenance
In the case of correct installation and adequate use, the safety-
monitoring module features maintenance-free functionality.
A regular visual inspection and functional test, including the following
steps, is recommended:
1. Check the fitting and integrity of the safety sensor, the actuator and
the cable
2. Remove possible metal chips
3. Check the cable for damage
4. Check cable entry and connections in a de-energised condition
Adequate measures must be taken to ensure protection
against tampering either to prevent tampering of the safety
guard, for instance by means of replacement actuators.
Damaged or defective components must be replaced.
6. Diagnostic functions
6.1 Operating principle of the diagnostic LED's
The safety sensor indicates the operating condition and faults by means
of three-colour LED's located in the lateral surfaces of the sensor.
The green LED indicates that the safety sensor is ready for operation.
The sensor is not actuated. When the safety sensor is actuated by the
CST 180 actuator, the indication switches from green to yellow. The
safety outputs of the safety sensor are enabled. If the actuator is near
the limit of the sensor's switching distance, the yellow LED will flash.
The safety outputs remain enabled. The sensor can be readjusted
before the safety outputs are disabled, thus stopping the machine.
Errors in the coding of the actuator, at the outputs of the sensor or in
the sensor are signalled by the red LED. After a short analysis of the
active fault, signalled by the red permanent signal, the defined error is
indicated by flash pulses. The safety outputs are enabled in a delayed
manner, when the fault is active for 1 minute.
LED indication (red)
Error cause
1 flash pulse
Error output Y1
2 flash pulses
Error output Y2
3 flash pulses
Cross-wire Y1/Y2
4 flash pulses
ambient temperature too high
5 flash pulses
Wrong or defective actuator
Continuous red
Internal error
6.2 Operating principle of the electronic diagnostic output
The short-circuit proof diagnostic output can be used for central
visualisation or control functions, e.g. in a PLC.
The electronic diagnostic output signals faults before the safety outputs
are disabled, thus enabling a controlled shutdown.
The diagnostic output is not a safety-related output!
The closed condition of the safety guard, i.e. the sensor is actuated,
is indicated through a positive signal. If the sensor is operating near
the limit of its switching distance, e.g. due to the sagging of the safety
guard, the sensor will emit a 2 Hz cyclic signal before the safety outputs
are disabled. An active fault will disable the diagnostic output after a
short analysis.
Table: diagnostic information
Sensor status LED
Diagnostic
output
Safety outputs
not actuated
green
0 V
0 V
actuated
yellow
Ue2
U
e
Actuated in limit
area
flashes
yellow
2 Hz pulsed
U
e
Fault:
1 ... 5 pulses
flashes red 10 s delayed
U
e2
0 V
1 min delayed
U
e
0 V
Error
red
10 s delayed
U
e2
0 V
undelayed
U
e
0 V
7. Disassembly and disposal
7.1 Disassembly
The safety switchgear must be disassembled in a de-energised
condition only.
7.2 Disposal
The safety switchgear must be disposed of in an appropriate manner in
accordance with the national prescriptions and legislations.