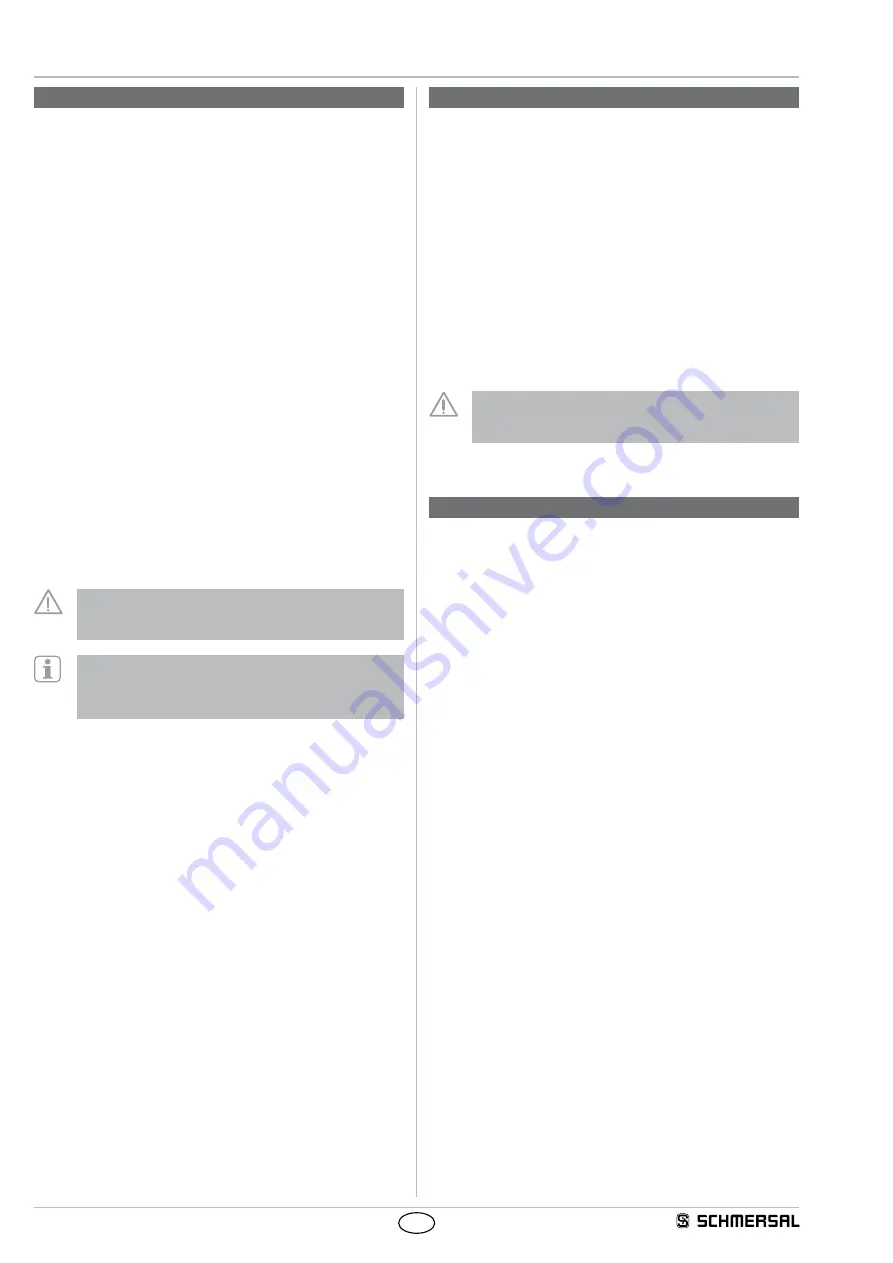
4
Operating instructions
Safety sensor
BNS 260 AS
EN
5. Configuration
5.1 Programming the slave address
The slave address is programmed through the connecting cable of the
BNS 260 AS. Depending on the variant used, every address can be
programmed between 1 and 31 through an M12 connector or an open
cable extremity.
5.2 Configuration of the safety monitor
The BNS 260 AS must be configured in the monitoring device as double
channel dependent module with start-up test.
The BNS 260 AS can be configured in the ASIMON configuration
software with the following monitoring devices (also refer to the
ASIMON manual):
Double channel dependent
• Optionally with startup test
• Synchronisation time typically 0.5 – 2.0 s
Double channel dependent with filtering
The use of this monitoring device is especially advantageous on safety
guards where bounce or vibration against the mechanical stop upon
closing is a problem.
• Optionally with startup test
• Stabilising time typically 0.5 -1.0 s
• Synchronisation time typically 5.0 – 10.0 s
The safety-monitoring module is only released after expiration of the
stabilising time; the synchronization time always must exceed the
stabilising time.
The configuration of the safety monitor must be tested and
confirmed by a qualified and authorised safety expert/safety
engineer.
During the project planning, it must be observed that the
length of the cable of each individual safety sensor is
integrated in the overall length (max. 100 m without repeater)
of the AS-Interface network.
6. Set-up and maintenance
6.1 Functional testing
The safety function of the safety components must be tested. The
following conditions must be previously checked and met:
1. Check the switch enclosure for damage
2. Fitting and integrity of the cable connections
3. Connect the BNS 260 AS to the AS-Interface network
4. Set the parameter outputs to "1111" (0xF)
5. Check the correct function of the BNS and BPS system with
configured safety monitor
6.2 Maintenance
In case of correct installation in accordance with the above-described
instructions, the component requires little maintenance. A regular
visual inspection and functional test, including the following steps, is
recommended:
1. Remove particles of dust and soiling
2. Fitting and integrity of the cable connections
Adequate measures must be taken to ensure protection
against tampering either to prevent tampering of the safety
guard, for instance by means of replacement actuators.
Damaged or defective components must be replaced.
7. Disassembly and disposal
7.1 Disassembly
The safety switchgear must be disassembled in a de-energised
condition only.
7.2 Disposal
The safety switchgear must be disposed of in an appropriate manner in
accordance with the national prescriptions and legislations.