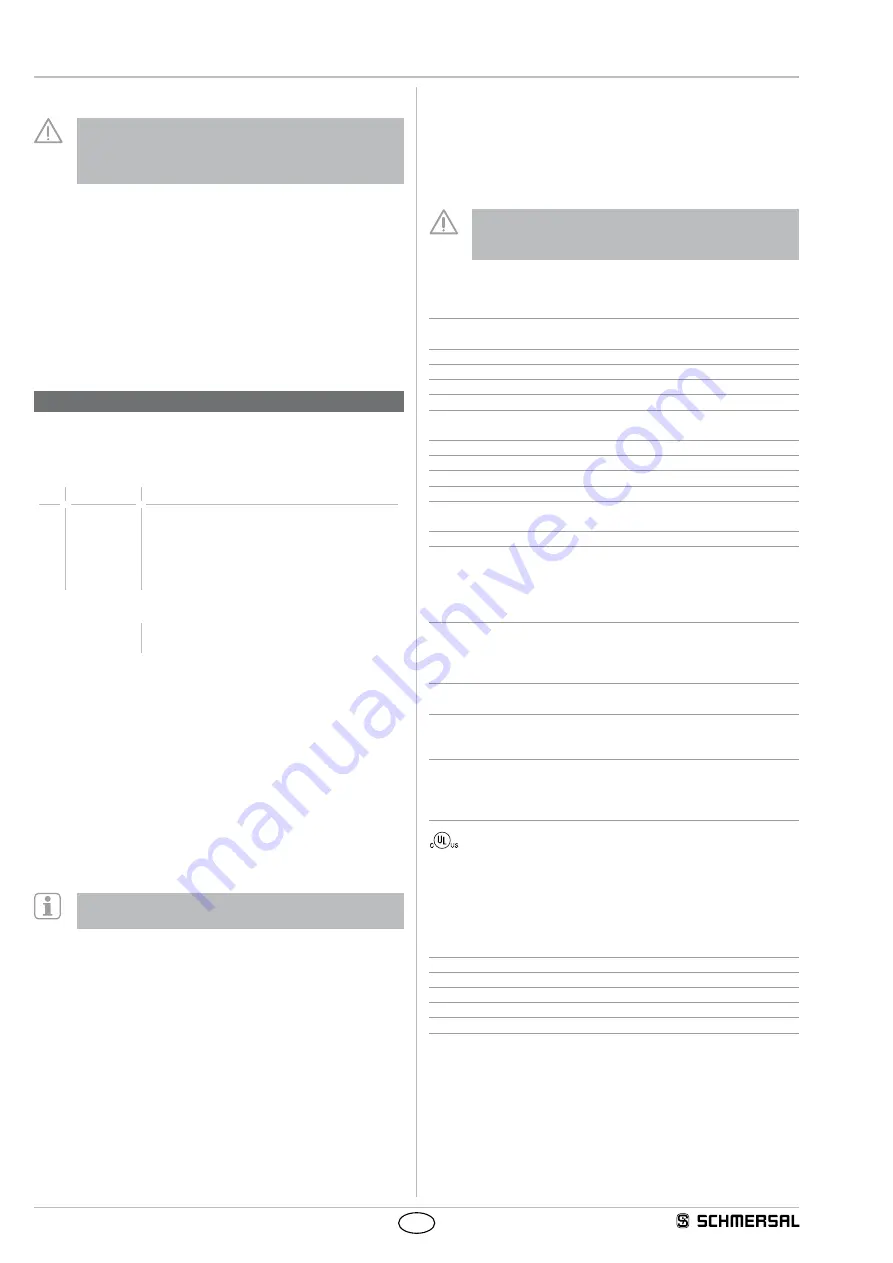
2
Operating instructions
Safety sensor
BNS 260 AS
EN
1.6 Warning about misuse
In case of improper use or manipulation of the safety
switchgear, personal hazards or damages to machinery
or plant components cannot be excluded. The relevant
requirements of the standard ISO 14119 must be observed.
1.7 Exclusion of liability
We shall accept no liability for damages and malfunctions resulting from
defective mounting or failure to comply with this operating instructions
manual. The manufacturer shall accept no liability for damages
resulting from the use of unauthorised spare parts or accessories.
For safety reasons, invasive work on the device as well as arbitrary
repairs, conversions and modifications to the device are strictly
forbidden; the manufacturer shall accept no liability for damages
resulting from such invasive work, arbitrary repairs, conversions and/or
modifications to the device.
2. Product description
2.1 Ordering code
This operating instructions manual applies to the following types:
BNS 260
➀
-AS-
➁
No. Option
Description
➀
Connecting cable (2 m)
STG
Connecting cable with M12 connector (straight)
STW
Connecting cable with M12 connector (angled)
➁
L
Door hinge on the left-hand side
R
Door hinge on the right-hand side
Actuator
BPS 260 -1
Included in standard version
BPS 260 -2
Mounting angle 90°
2.2 Special versions
For special versions, which are not listed in the order code below 2.1,
these specifications apply accordingly, provided that they correspond to
the standard version.
2.3 Purpose
The safety sensor is used in AS interface systems for monitoring the
position of movable safety guards in accordance with ISO 14119 and
IEC 60947-5-3. The combination of the BNS 260 AS safety sensor,
the BPS 260-1/-2 actuator and the ASM safety monitor ensures the
safe monitoring of the condition of the corresponding safety guard. To
actuate the safety sensor, only the coded BPS 260-1/-2 actuators must
be used.
The safety switchgears are classified according to ISO 14119
as type 4 switching devices.
The safety function consists in safely switching off the code
transmission when the safety guard is opened and maintaining the safe
switched off condition for as long as the safety guard is open.
An AS-Interface Safety at Work component functions on the basis of
an individual code generator (8 x 4 bit). This safety code is cyclically
transmitted over the AS-i network and monitored by the safety monitor.
The component status can be evaluated through a PLC with AS-
Interface master. The safety-related functions are enabled by means of
the AS-i safety monitor.
LED display
The LEDs have the following meaning (to EN 62026-2):
Green LED
AS-Interface supply voltage
Red LED
AS-Interface communication error or slave address = 0
The user must evaluate and design the safety chain in
accordance with the relevant standards and the required
safety level.
2.4 Technical data
Standards:
EN 62026-2, IEC 60947-5-3,
ISO 13849-1, IEC 61508
Enclosure:
glass-fibre reinforced thermoplastic,
self-extinguishing
Coding level according to ISO 14119:
low
assured switching distance s
ao
:
5 mm
assured switch-off distance s
ar
:
15 mm
Protection class:
IP67 to IEC 60529
Termination:
cable LSYY (0.23 mm² / AWG 24);
connector M12 x 1, 4-pole
Ambient temperature:
–25 °C … +60 °C
Storage and transport temperature:
–25 °C … +70 °C
Maximum switching frequency:
1 Hz
Electrical data AS-Interface:
AS-I voltage range:
18.0 ... 31.6 VDC, through AS-Interface, reverse
polarity-proof
AS-I power consumption:
≤ 0.05 A
AS-I Specification:
(V 2.1)
AS-i slave profile: S-0.B.F.E,
IO code: 0x0,
ID code: 0xB,
ID code1: 0xF,
ID code2: 0xE
AS-interface inputs:
Contact 1: Data bits D0 / D1 = static 00 or
dynamic code transmission
Contact 2: Data bits D2 / D3 = static 00
or dynamic code transmission
Parameter port:
P0 ... P3: no function, set parameter outputs
to "1111" (0xF)
Input module address:
preset to address 0,
can be changed through AS-interface bus master
or hand-held programming device
Diagnostic indication:
AS-i LED green:
AS interface supply voltage
AS-i LED red:
AS interface communication error
or slave address = 0
For use in NFPA 79 Applications only.
Only for use in Pollution Degree 2 Environment.
Adapters providing field wiring means are available from
the manufacturer. Refer to manufacturers information.
2.5 Classification
Standards:
ISO 13849-1, IEC 61508
PL:
e
Control Category:
4
PFH:
6.21 x 10
-9
/ h for ≤ 500.000 operations / year
SIL:
suitable for SIL 3 applications
Mission time:
20 years