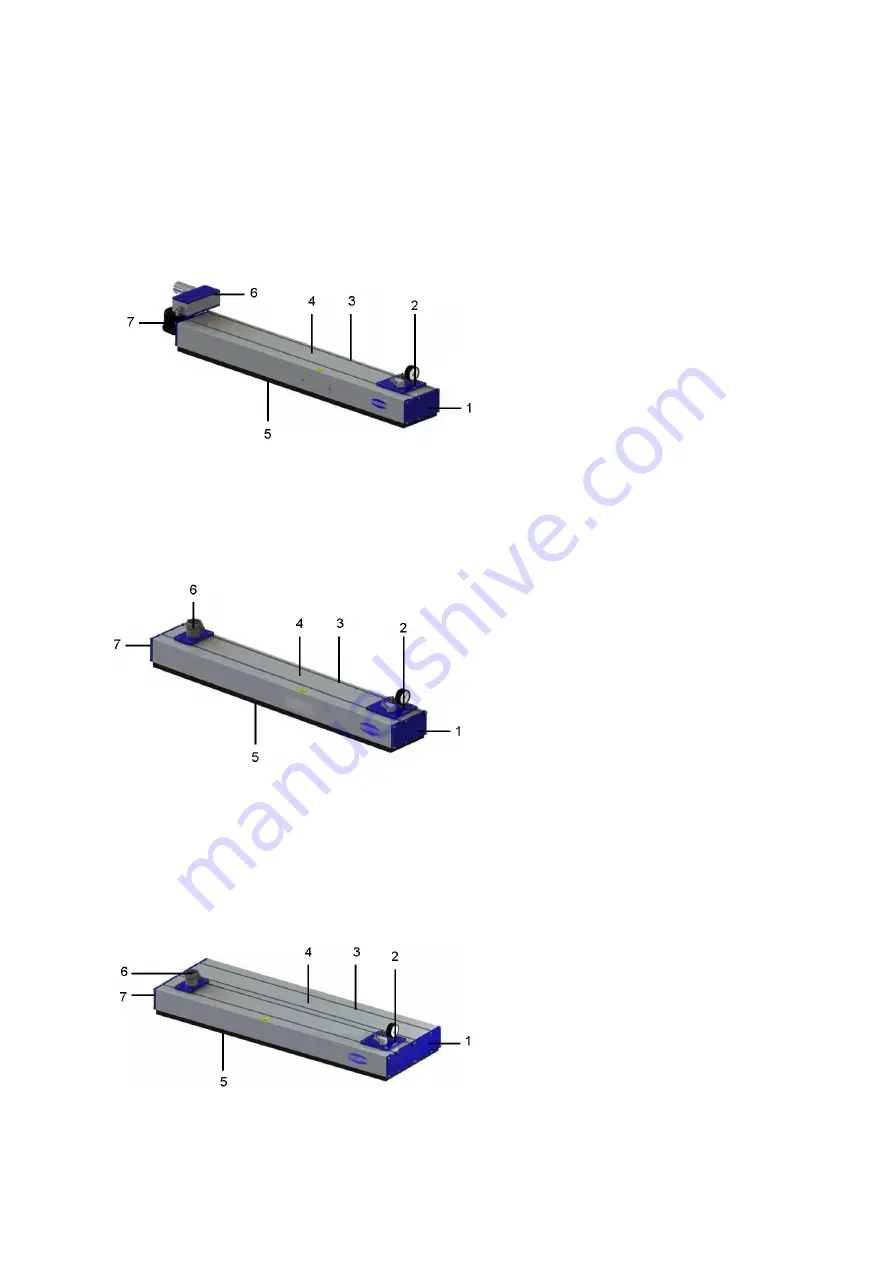
PRODUCT DESCRIPTION
10 | EN
www.schmalz.com
30.10.02.00604/02
2.3 Design
2.3.1 Ejector SBX-C 200
1. Cover
2. Connection plate
3. T-slot
4. Main body with
integrated
function modules
5. Sealing mat
6. Vacuum ejector
7. Dust filter (2.3.7)
2.3.2 Blower/pump SBX-C 200
1. Cover
2. Connection plate
3. T-slot
4. Main body with
integrated
function modules
5. Sealing mat
6. Vacuum connection
7. Cover
2.3.3 Blower/pump SBX-C 400
1. Cover
2. Connection plate
3. T-slot
4. Main body with
integrated
function modules
5. Sealing mat
6. Vacuum connection
7. Cover with
venting unit