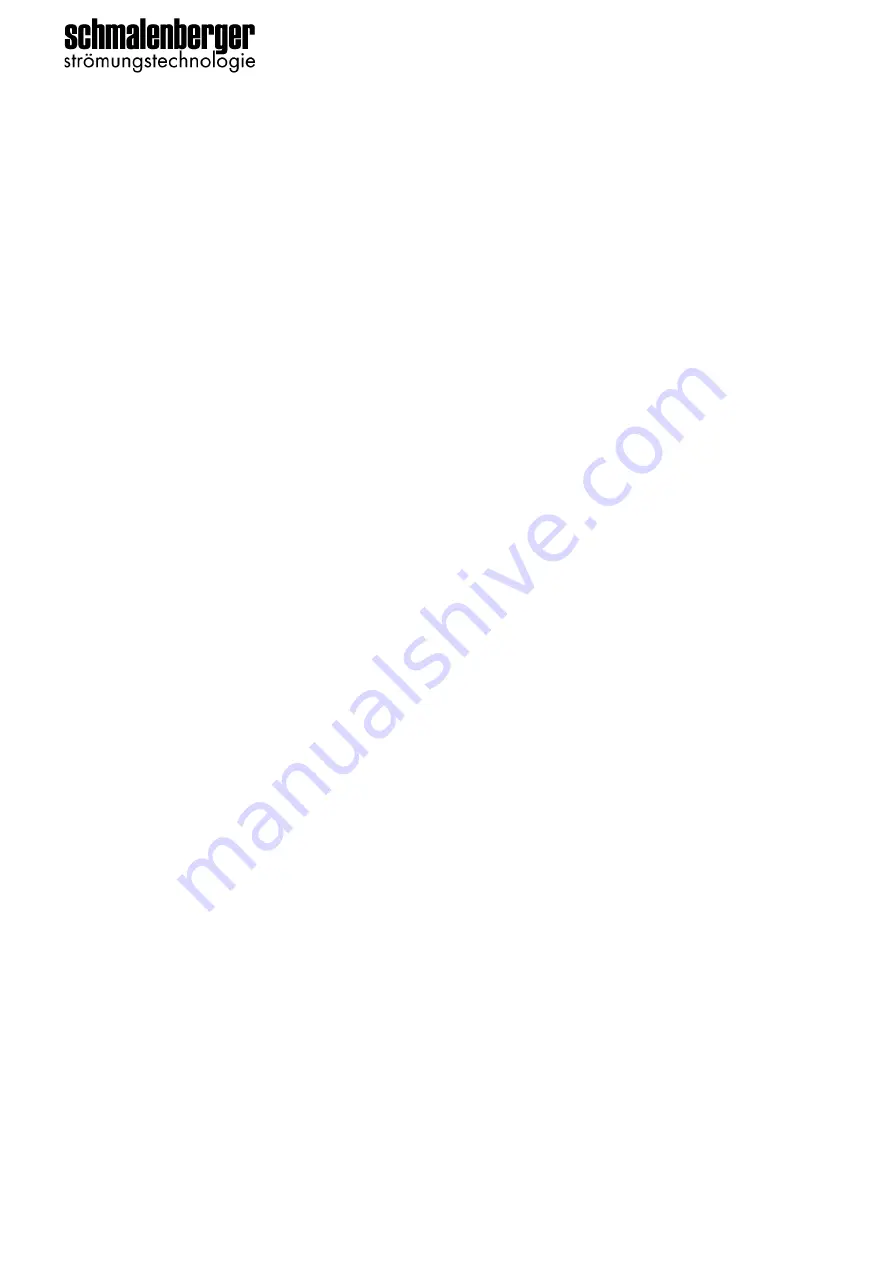
6
Pump Typ Z
Version: 27215 -G.1
Schmalenberger GmbH + Co. KG
D-72072 Tübingen / Germany
1
General Details
1.1
User Information
This operator’s manual makes it easier to
get to know the centrifugal pump and to
make full use of its facilities.
The operator’s manual contains important
instructions how to use the centrifugal
pump safely, properly and economically.
Your careful attention to these instructions
will help to avoid danger, to reduce repair
costs and breakdowns and to increase the
reliability and useful life of the centrifugal
pump.
The operator’s manual does not take
account of local regulations. The user is
responsible for ensuring that they are
complied with.
The label specifies the machine series, the
frame size, the most important operating
data and the serial number. We request
that you always quote it in case of queries,
when placing subsequent orders and
especially when ordering spare parts.
1.2
Usage Instructions
The centrifugal pump must only be used in
accordance with the original pump
specifications and the operator´s manual.
Any other usage or operation where these
figures are exceeded is not permitted. The
manufacturer is not liable for damage
resulting from such improper use.
The pump must only be operated in
applications that are described in the
relevant documents.
•
The pump must only be operated if it is
in flawless technical condition.
•
The pump must not be operated if it is
only partially mounted.
•
The pump may only be used to convey
the media described in the data sheet
or in the documentation for the relevant
design.
•
Never operate the pump without a pum-
ping medium.
•
Pay careful attention to the information
in the data sheet or documentation re-
garding minimum delivery volume (to
prevent damage from overheating, da-
mage to the bearings, etc.).
•
Pay careful attention to the information
in the data sheet or documentation re-
garding maximum delivery volume (to
prevent overheating, damage to the
mechanical seal, cavitation damage,
damage to the bearings, etc.).
•
Do not throttle the pump on the suction
end (to prevent cavitation damage).
•
Coordinate other types of operation
with the manufacturer if they are not ci-
ted in the documentation or data sheet.
Preventing foreseeable misuse
•
Never open the pressure-end shut-off
elements beyond the permissible range
- Exceeding the maximum delivery vo-
lume cited in the data sheet or docu-
mentation is not permitted (possible
cavitation damage)
•
Never exceed the permissible operating
limits cited in the data sheet or docu-
mentation in terms of pressure and tem-
perature, etc.
•
Comply with all safety instructions and
directions in this operator's manual.
1.3
Relevant Documentation
Various documents are associated with
every centrifugal pump that comprise the
technical documentation of the pump.
These are as follows:
•
Specification with all data
•
Operator’s manual
•
Declaration of conformity / Declaration
of Incorporation
•
Drive operator’s manual
•
Declaration of conformity with supple-
ment BA for ATEX-pumps